МИНИСТЕРСТВО ОБРАЗОВАНИЯ И НАУКИ РОССИЙСКОЙ ФЕДЕРАЦИИ
федеральное государственное бюджетное образовательное учреждение высшего образования «Казанский национальный исследовательский технический университет им. А.Н. Туполева - КАИ»
(КНИТУ - КАИ)
Альметьевский филиал
Кафедра «Конструирования и машиностроительных технологий»
КУРСОВАЯ РАБОТА
на тему:
«Нормирование точности и контроль деталей сборочной единицы»
2016 г.
Содержание
Введение 1.1 Исходные данные 1.2 Нормирование точности гладких соединений 1.2.1 Подбор посадки методом подобия 1.2.2 Назначение посадки расчетным методом 1.2.3 Контроль размеров гладкими калибрами 1.2.4 Допуски и посадки подшипников качения на вал и корпус 1.2.5 Допуски размеров, входящих в размерные цепи 1.3 Нормирование точности соединений сложного профиля 1.3.1 Нормирование точности метрической резьбы 1.3.2 Нормирование точности шпоночных соединений 1.3.3 Нормирование точности шлицевых соединений 1.3.4. Нормирование точности цилиндрических зубчатых колес 1.4 Выбор универсальных средств измерений Заключение Список используемой литературы |
Введение
Основной задачей конструктора является создание новых и модернизация существующих изделий, подготовка технической документации, способствующей обеспечению необходимой технологичности и высокого качества. Решение этой задачи связано с выбором необходимой точности изготовления изделий, расчётом размерных цепей, выбором шероховатости поверхностей, а также выбором допусков отклонений от геометрической формы и расположения поверхностей.
Успешное решение основной задачи конструктора тесно связано с повышением качества и уровня его профессиональной подготовки. Важным мероприятием, которое помогает упорядочить и облегчить работу конструкторов, является переход отечественной промышленности на Единую систему допусков и посадок (ЕСДП) и Основные нормы взаимозаменяемости (ОНВ).
В данной курсовой работе отражены вопросы взаимозаменяемости по выбору полей допусков и расчету размеров, посадок для гладких цилиндрических соединений, шарикоподшипников, шлицевых, шпоночных и резьбовых соединений, по построению схем расположения полей допусков, по определению исполнительных размеров и эскизированию гладких предельных калибров; назначены средства контроля; использован метод максимума-минимума для расчёта размерной цепи.
Основная цель курсового проектирования - привить навыки использования общих методов метрологии, стандартизации и взаимозаменяемости при синтезе различных изделий.
1.1 Исходные данные
Тема курсовой работы: «Нормирование точности и контроль деталей сборочной единицы»
На рисунке изображена часть раздаточной коробки автомобиля; эта коробка служит для передачи крутящего момента к ведущим мостам автомобиля.
Зубчатое колесо 5 включения заднего моста перемещается по шлицам передаточного вала 1 с помощью вилки 4. Правый конец вала опирается на подшипник качения, установленный в гнездо зубчатого колеса 6, изготовленного как одно целое с вторичным валом.
Левый конец вала 1 имеет подшипник 2, который закрыт крышкой 18, которая установлена на крыльчатке 19 по D3 с незначительным зазором и крепится винтами 3 с нормальной длиной свинчивания к корпусу 7.
Величина зазора должна быть строго выдержана (оговорено заданием). Гайка 20, которая закрепляет крыльчатку, имеет короткую длину свинчивания.
На хвостовике вторичного вала 6 по D2 на сегментной шпонке с незначительным зазором установлено зубчатое колесо 9 привода спидометра.
В корпус 10 установлен подшипник 8 вторичного вала. Корпус 10 точно центрируется по D1 в корпусе раздаточной коробки 7.
На шлицевом валу 15 смонтированы промежуточное колесо 13 и зубчатое колесо понижающей передачи 17. При положении, указанном на чертеже, включена прямая передача; при введении зубчатого колеса 5 в зацепление с зубчатым колесом 17, включается понижающая передача.
Шлицы в отверстиях зубчатых колёс закаливаются.
Зубчатая передача среднескоростная, колёса стальные с нагревом до +70ºC, корпус раздаточной коробки изготавливается из силумина и нагревается +60ºC.
Крышки подшипников 16 и 11 должны
свободно устанавливаться в отверстиях корпуса, так как их подтяжкой
регулируются зазоры в конических подшипниках 14. Крышки подшипников крепятся
при помощи болтов, имеющих резьбу нормальной длины свинчивания.
Подшипники качения испытывают умеренные толчки и вибрации и при работе имеют перегрузку до 300%. Между крышкой 16 и подшипников 14 предусмотрен тепловой зазор, величина которого обеспечивается расчетом размерной цепи.
Перечислим звенья размерной цепи:
А1 и А5 – высота буртиков крышек 11 и 16;
А2 и А4 – толщина прокладок;
А3 – корпусный размер;
А6 и А8 – монтажная высота подшипников;
А7 – длина шлицевой части ступени вала 15.
Часть раздаточной коробки автомобиля
Таблица 1.1
Числовые значения заданных параметров
1.2 Нормирование точности гладких соединений
1.2.1 Подбор посадки методом подобия
Таблица 1.2
Карта исходных данных по D1
Наименования исходных данных |
Значения исходных данных |
Номинальный размер соединения и его значение |
D1 = 90мм |
Название деталей, входящих в соединение |
Подшипник 8 и корпус 10 |
Требования, предъявляемые к работе соединения (из описания к рисунку) |
Корпус 10 точно центрируется по D1 в корпусе раздаточной коробки 7 |
Выбрать систему посадки
В соединение входит подшипник 8 и корпус 10. Так как внутренние поверхности более сложны в обработке, то выбираем систему отверстия СН с основным отверстием в муфте.
![]() |
Определить тип посадки
Методом подобия подбираем вид сопряжения, назначаем предпочтительную посадку H7/k6 [1, табл. 1.6]. В соединениях по переходной посадке H7/k6, вероятность получения зазоров и натягов одинакова. При L≤3d зазоры не ощущаются. Она применяется для установки зубчатых колес на валах редукторов, в станках и других машинах, передача крутящего момента обеспечивается шпонкой.
Определить предельные отклонения сопрягаемых деталей
Для отверстия: D1 =90H7; TD = 0,035 мм; ES = 0,035 мм;
D1 = 22 .
Для вала: d1 = 90k6; Td = 0,022 мм; es = 0,025 мм; ei = 0,003 мм
d1 = 90.
Назначена посадка
Ø 90 .
Определить предельные размеры отверстия и вала
Предельные размеры отверстия:
Dmax = D + ES = 90+ 0,035 = 90,035 мм;
Dmin = D + EI = 90 + 0 = 90 мм;
Dm = Dmin + TD/2 =90 + 0,035/2= 90,0175 мм.
Предельные размеры вала:
dmax = d + es = 90 + 0,025 =90,025 мм;
dmin = d + ES = 90 + 0,003 = 90,003 мм;
dm = dmin + Td/2 = 90,003+ 0,022/2= 90,014 мм.
Выполнить расчет характеристик
посадки
Определение величины натягов выполним по формулам [1].
Максимальный зазор: Smax = Dmax - dmin = 90,035-90,003=0,032 мм.
Максимальный натяг: Nmax = dmax – Dmin= 90,025-90=0,025 мм.
Средневероятный зазор:
Sm = (Smax + Nmax)/2 = (0,032 + 0,025)/2 = 0,0035 мм или
Sm = Dm – dm = 90,0175-90,014 = 0,0035 мм
Рассчитать допуск посадки по двум формулам:
TSN = TD + Td = 35+ 22= 57 мкм или
TSN = Smax – Nmax = 0,032 – 0,025 = 0,057мм.
Построим схему расположения полей допусков.
Рисунок 1.1 – Схема расположения полей допусков вала и отверстия
Назначить шероховатость и допуски
формы поверхностей
Значение шероховатости поверхностей сопрягаемых деталей определяем методом подобия. Для соответствующих квалитетов при нормальном уровне относительной геометрической точности (А) [1, табл. 2.3 и табл.2.4]:
– для отверстия 7-го квалитета Ø 90: Ra = 1,6 мкм;
– для вала 6-го квалитета: Ra = 0,8 мкм .
Допуск формы поверхности - цилиндричности (круглости и допуск профиля продольного сечения) назначаем по [1, табл. 2.3]; [1, табл. 2.9]:
– для отверстия диаметром 90 H7 рекомендуется 6-я степень, при относительной геометрической точности А допуск формы имеет значение:
Tф = 10 мкм,
– для вала Ø 90 p6 требуется 5-я степень, которая при относительной геометрической точности А – Tф = 6 мкм.
Рисунок 1.2 – Эскизы деталей соединения “подшипник-корпус”
Таблица 1.3
Карта исходных данных по D2
Наименования исходных данных |
Значения исходных данных |
Номинальный размер соединения и его значение |
D2 = 42 мм |
Название деталей, входящих в соединение |
Зубчатое колесо 9 и корпус 10 |
Требования, предъявляемые к работе соединения (из описания к рисунку) |
По D2 на сегментной шпонке с незначительным зазором установлено зубчатое колесо 9 |
Выбрать систему посадки
В соединение входит зубчатое колесо 9 и корпус 10. Так как внутренние поверхности более сложны в обработке, то выбираем систему отверстия СН с основным отверстием в зубчатом колесе.
Определить тип посадки
Незначительный зазор обеспечивает посадку с зазором, поэтому принимаем посадку с зазором – Н/g.
Методом подобия подбираем вид сопряжения, назначаем предпочтительную посадку Н7/g6 [1,табл. 1.6]. Применяются в особо точных механизмах (плунжерные и золотниковые пары). Шпиндели точных станков, направляющие втулки, переключаемые шестерни на валах коробок передач, сменные направляющие втулки в кондукторах, опорные пальцы приспособлений, подшипники скольжения при малых нагрузках, для регулируемых стаканов под подшипники.
Определить предельные отклонения сопрягаемых деталей
Для отверстия: D2 = 42 H7; TD = 0,025 мм; ES = 0,025 мм; EI = 0 мм,
D2 = 42 .
Для вала: d2 = 42 g6; Td = 0,016 мм; es = -0,009 мм; ei = -0,025 мм
d2 = 42 g6
.
Назначена посадка
Ø 42 .
Определить предельные размеры отверстия и вала
Предельные размеры отверстия:
Dmax = D + ES = 42 + 0,025 = 42,025мм;
Dmin = D + EI = 42 + 0 = 42 мм;
Dm = Dmin + TD/2 = 42 + 0,025/2 = 42,0125 мм.
Предельные размеры вала:
dmax = d + es = 42 + (-0,009) = 41,991 мм;
dmin = d + ES = 42 + (-0,025)= 41,975 мм;
dm = dmin + Td/2 = 41,975 + 0,016/2= 41,983мм.
Выполнить расчет характеристик посадки
Определение величины зазоров (натягов) выполним по формулам [1].
Максимальный зазор: Smax = Dmax – dmin = 42,025 – 41,975= 0,05 мм.
Натяга нету. Smin = Dmin – dmax = 42-41,991=0,009 мм
Средневероятный зазор:
Sm = Dm – dm = 42,0125 – 41,983 = 0,0295 мм
Допуск посадки:
TSN = TD + Td = 0025 + 0,016 = 0,041 мм
TD+Td = Smax – Smin
0,041= 0,041
Построим схему расположения полей допусков.
Рисунок 1.3 – Схема расположения
полей допусков вала и отверстия
Назначить шероховатость и допуски формы поверхностей
Значение шероховатости поверхностей сопрягаемых деталей определяем методом подобия. Для соответствующих квалитетов при нормальном уровне относительной геометрической точности (А) [1, табл. 2.3 и табл.2.4]:
– для отверстия 7-го квалитета Ø 42: Ra = 1,6 мкм;
– для вала 6-го квалитета: Ra = 0,8 мкм .
Допуск формы поверхности - цилиндричности (круглости и допуск профиля продольного сечения) назначаем по [1, табл. 2.3]; [1, табл. 2.9]:
– для отверстия диаметром 42 H7 рекомендуется 6-я степень, при относительной геометрической точности А допуск формы имеет значение:
Tф = 10 мкм,
– для вала Ø 42 k6 требуется 5-я степень, которая при относительной геометрической точности А – Tф = 6 мкм.
Рисунок 1.4 – Эскизы деталей
соединения «зубчатое колесо – корпус»
1.2.2 Назначение посадки расчетным методом
Таблица 1.4
Карта исходных данных по D3
Наименования исходных данных |
Значения исходных данных |
Номинальный размер соединения и его значение |
D3 = 68 мм |
Название деталей, входящих в соединение |
втулка и вал |
Заданные характеристики для расчетного метода назначения посадок, мкм: Smax, Smin |
Smax = 71 мкм Smin = 12 мкм |
Выбрать систему посадки
В соединение (рис.3.1) входит втулка, которая перемещается по валу с зазором, так как внутренние поверхности более сложны в обработке и измерении, выбираем систему отверстия СН.
Рассчитать относительную точность посадки и определить квалитет
Рассчитаем допуск посадки:
TS = Smax – Smin = 71 – 12 = 59 мкм. По номинальному размеру Ø 68 находим единицу допуска [1, табл.1.1]:
i=1,9 мкм.
Средняя точность по числу единиц допуска посадки:
aS = TS/i = 59/1,9 = 31. Исходя из того, что aS = aD + ad, принимаем aD = ad = 16, что соответствует 7 квалитету для обеих деталей.
Определить предельные отклонения сопрягаемых деталей
Принята
система отверстия, следовательно, отверстие – Ø 68 H7.
Верхнее отклонение по модулю для вала равно минимальному зазору |es| ≈ Smin , что соответствует основному отклонению g [1, табл. 1.2] |es| = – 12 мкм, следовательно, вал имеет поле допуска g7.
Нижнее отклонение вала определим по формуле:
ei = (|es| + T7) = – (0,012 + 0,030) = – 0,042 мм.
Посадка
будет в следующем виде: Ø 68 .
Расчет характеристик посадки
Предельные размеры отверстия:
Dmax = D + ES = 68 + 0,30 =68,030 мм;
Dmin = D + EI = 68 + 0 = 68 мм;
Dm = Dmin + TD/2 = 68,015 мм.
Предельные размеры вала:
dmax = d + es = 68 + (-0,01) = 67,99 мм;
dmin = d + ei= 68 + (-0,04) = 67,96 мм;
dm = dmin + Td/2 = 67,96 + 0,030/2 = 67,975 мм.
Максимальный зазор: Smax = Dmax – dmin =68,030 – 67,96 = 0,07 мм.
Минимальный зазор: Smin = Dmin – dmax = 68 –67,99 = 0,01 мм.
Средний зазор:
Sm = (Smax + Smin)/2 = (0,07 + 0,01)/2 = 0,04 мм
Расчетный допуск посадки:
TS = TD + Td = 30 + 30 = 60 мкм
TS = Smax – Smin = 0,07 – 0,01 = 0,06 мм.
Проверка правильности расчета посадки производится путем сравнения табличных (стандартных) значений передельных зазоров с заданными:
Smax табл. = 70 ≤ Smax = 71 мкм. Smin табл. = 10 ≈ Smin = 12 мкм.
Условия правильности расчета выполнены.
Построим схему расположения полей допусков.
Рисунок 1.5 - Схема расположения полей допусков вала и отверстия
Назначаем шероховатость и допуски формы поверхностей
Технические требования на рабочие чертежи деталей определим расчетным методом для нормального уровня относительной геометрической точности (А). Коэффициенты отношения допусков размеров к допускам шероховатости и формы поверхностей принимают значения [1, табл. 2.11]: Kr = 0,05; Kф = 0,3.
Для отверстия допуск размера TD = 46 мкм, тогда Ra = Kr ∙ TD = 0,05 ∙ 46 = 2,3 мкм, принимаем для отверстия: 2,5 мкм по [1, табл. 2.2].
Для вала допуск размера Td = 30 мкм, тогда Ra = Kr ∙ TD = 0,05 ∙ 30 = 1,5 мкм, принимаем для вала: 1,6 мкм по [1, табл. 2.2].
Расчет допуска формы (допуска цилиндричности):
для отверстия Tф = Kф ∙ TD = 0,3
∙ 46 = 0,014 мм, округляем до Tф = 16 мкм [1, табл. 2.9];
для вала Tф = Kф ∙ TD = 0,3 ∙ 30 = 0,009 мм, округляем до Tф = 10 мкм [1, табл. 2.9].
1.2.3 Контроль размеров гладкими калибрами
Таблица 1.5
Карта исходных данных для проектирования калибров
Контролируемая поверхность |
Контролируемый размер |
Калибр |
Отверстие |
Ø
68 |
Пробка |
Определить допуски и отклонения гладких калибров
По номинальному размеру вала (отверстия) и по квалитету точности выбранной посадки найти отклонения и допуски для калибра-скобы (пробки), а также на контркалибры К-И, К-ПР, К-НЕ. Допуски и отклонения гладких калибров определены по ГОСТ 24853-81 [1, табл. 8.1]. Найденные значения указаны в табл. 3.5.
Таблица 1.6
Допуски и отклонения гладких калибров
Наименование параметров |
Пробка |
|
Обозначение |
Величина |
|
Размер сдвига поля допуска проходных калибров внутрь поля допуска детали |
Z |
4 |
Размер выхода допуска на износ за границу поля допуска детали |
Y |
3 |
Допуск на изготовление калибра |
H |
5 |
Допуск на изготовление контркалибра |
Hp |
2 |
Проектирование калибра-пробки
Для калибра-пробки выбираем схему
расположения полей допусков для размеров до 180 мм, квалитетов с 6-го по 8-й [1, рис.8.1, а]. Схема представлена на рис. 3.6.
Расчет исполнительных размеров калибра-пробки
Исполнительные и предельные размеры пробки согласно схеме расположения полей допусков (рис. 1.6), подсчитываются по формулам [1, табл. 8.2]:
ПРmax = Dmin + Z + H/2 = 68 + 0,004 + 0,005/2 = 68,0065 мм;
ПРmin = Dmin + Z - H/2 = 68 + 0,004 - 0,005/2 =68,0015 мм;
ПРисп = ПРmax - H =68,0065- 0,005 мм.
НЕmax = Dmax + H/2 = 68,030 + 0,005/2 = 68,0325 мм;
НЕmin = Dmax - H/2 = 68,030 - 0,005/2 = 68,0275 мм.
НЕисп = НЕmax - H = 68,0325- 0,005 мм.
Размер предельного износа пробки определяется по следующей формуле:
ПРизн = Dmin - Y = 68 - 0,003 =67,997 мм.
Рисунок 1.6 – Схема расположения
полей допусков отверстия и калибра-пробки
Технические требования к калибрам
Допуск цилиндричности (для круглых пробок) [1,4]:
TO = 1/3 H = 5/3 = 1,667 мкм. Округляем до ближайшего числа из ряда чисел:(0,8; 1; 2; 2,5; 3;4; 5; 6; 8; 10...) ТO = 2 мкм.
Шероховатость рабочих поверхностей Ra по ГОСТ 2015-84 [1, табл. 8.3]: пробки и скобы – Ra=0,05 мкм, контркалибров – Ra=0,025 мкм. Шероховатость торцов – Ra=1,6 мкм, фасок – Ra = 0,8 мкм. Размер контролируемого отверстия находится в интервале свыше 50 мм, поэтому выбираем пробки с насадками: проходную по ГОСТ 14815-69,
непроходную – ГОСТ 14816-69.
Таблица 1.7
Конструктивные размеры калибр-пробки
Рисунок 1.7 – Пробка 8133-0944 H7 ГОСТ 14810-69
Расчет контркалибров для контроля скобы
Для контроля размеров калибров-скоб используют контркалибры. Исполнительные размеры контркалибров, согласно схеме расположения полей допусков (рис. 3.8), подсчитываются по формулам [1, табл. 8.2; 4, с. 8]:
К-И = dmax + Y1 + HP/2 =67,99 + 0,003 + 0,002/2 = 67,994- 0,002 мм;
К-ПР = dmax - Z1 + HP/2 = 67,99 - 0,004 + 0,002/2 = 67,985- 0,002 мм;
К-НЕ = dmin + HP/2 = 67,96 + 0,002/2 = 67,961- 0,002 мм;
Рисунок 1.10 – Эскизы контркалибров
для скобы
1.2.4 Допуски и посадки подшипников качения на вал и корпус
Для колец заданного подшипника назначить посадки на вал и в корпус. Расшифровать условное обозначение подшипника. Построить схемы полей допусков. Вычертить эскизы подшипникового узла и посадочных поверхностей вала и корпуса под подшипник.
Таблица 1.9
Карта исходных данных для подшипников качения
Наименования исходных данных |
Значения исходных данных |
Условное обозначение подшипника |
1806608 |
Номер позиции по чертежу |
2 |
Радиальная нагрузка R, кН |
38,0 |
Режим работы подшипника, допустимые перегрузки, в % |
300 % |
Вращающаяся деталь |
вал |
Конструкция вала (по чертежу) |
сплошной |
Конструкция корпуса (по чертежу) |
сплошной |
Расшифровать условное обозначение
подшипника
Условное обозначение подшипника –1806608 подшипник шариковый однорядный радиально-упорный по ГОСТ 8338.
Расшифровка условного обозначения:
код внутреннего диаметра 08;
серия по наружному диаметру 6;
тип подшипника 6;
конструктивное исполнение 80;
серия по ширине 1;
класс точности 0.
Конструктивные размеры подшипника
Определяем параметры
подшипника: [1, табл. 4.3]. Внутренний диаметр подшипника d= 40 мм. Наружный диаметр подшипника
D = 90 мм. Ширина подшипника В = 33 мм. Радиусы
закруглений r=2,5 мм.
Рисунок 1.11 – Эскиз подшипника 8882
По ГОСТ 520 определим отклонения
внутреннего и наружного колец подшипника: [1, табл. 4.9] для нулевого класса:
L0 = LD = Δdmp = мкм;
l0 = lD = ΔDmp = мкм.
Определить вид нагружения колец
Вращающаяся деталь – вал, следовательно, внутреннее кольцо подшипника испытывает циркуляционную нагрузку, наружное кольцо испытывает местное нагружение.
Расчет интенсивности радиальной нагрузки
Вращающееся кольцо подшипника испытывает циркуляционный вид нагружения, что требует обеспечения неподвижного соединения с сопрягаемой деталью. Величина минимального натяга зависит от интенсивности радиальной нагрузки, определяемой по формуле:
,
где Р – интенсивность радиальной
нагрузки, кН/м;
R – радиальная нагрузка на подшипник, кН;
В – ширина подшипника, мм;
r и r1 – радиусы закруглений внутреннего кольца подшипника, мм;
К1 – динамический коэффициент посадки, зависящий от допустимой перегрузки, К1 = 1,8 при перегрузке до 300 %;
К2 – коэффициент, учитывающий ослабление посадочного натяга при пониженной жесткости вала или корпуса. Для жесткой конструкции К2 = 1 [1, табл. 4.10];
К3 – коэффициент неравномерности распределения радиальной нагрузки между рядами тел качения в двурядных роликоподшипниках и сдвоенных шарикоподшипниках при наличии осевой нагрузки на опору, для однорядных подшипников К3 = 1 [1, табл.4.11]:
Выбор полей допусков
Для циркуляционно-нагруженного кольца подберем посадку в зависимости от диаметра, интенсивности радиальной нагрузки и класса точности [1,табл. 4.12] .Посадка для внутреннего кольца подшипника:
Ø 40 .
Для местно-нагруженного кольца подберем посадку в зависимости от диаметра, класса точности и величины перегрузки [1,табл. 4.13]. Посадка для наружного кольца подшипника
Ø 90 .
Определить предельные размеры
Внутреннее кольцо подшипника:
Dmax = D + ES = 40 + 0 = 40 мм;
Dmin = D + EI = 40 + (-0,012) = 39,988 мм;
Вал:
dmax = d + es = 40 + 0,0033 = 40,033 мм;
dmin = d + ei= 40 + 0,017= 40,017 мм;
Максимальный натяг: Nmax = dmax – Dmin =40,033– 39,988 = 0,045 мм.
Минимальный натяг: Nmin = dmin – Dmax = 40,017 –40 = 0,017 мм.
Средний натяг:
Nm = (Nmax – Nmin)/2 = (0,045 – 0,017)/2 = 0,031 мм
Отверстие корпуса:
Dmax = D + ES = 90 + 0,011 = 90,011 мм;
Dmin = D + EI = 90 + 0,011 = 89,989 мм;
Наружное кольцо подшипника:
dmax = d + es = 90 + 0 = 90 мм;
dmin = d + ei = 90 + (-0,015) = 89,985 мм;
Максимальный зазор: Smax = Dmax – dmin = 90,011 – 89,985 = 0,026 мм.
Максимальный натяг: Nmax = dmax – Dmin = 90 – 89,989 = 0,011 мм.
Средний зазор:
Sm = (Smax + Nmax)/2 = (0,026 + 0,011)/2 = 0,0075 мм
Построим схему расположения полей допусков.
Рисунок 1.12 – Схема расположения
полей допусков внутреннего кольца подшипника и вала
Рисунок 1.13 – Схема расположения полей допусков наружного кольца подшипника и корпуса
Технические требования на рабочие
поверхности вала и корпуса Методом подобия назначаем параметры шероховатости поверхностей сопрягаемых
деталей [1, табл. 2.3]: для вала, отверстия в корпусе Ra= 0,8 мкм, для торцов заплечиков Ra= 1,6 мкм
Допуски формы и расположения посадочных поверхностей валов и отверстий корпусов установлены ГОСТ 3325 и приводятся в [1, табл. 4.15]. Допуски круглости и профиля продольного сечения:
- для вала Tф= 4 мкм;
- для отверстия: Tф= 9 мкм.
Допуск торцового биения заплечиков:
- вала: Тб = 16 мкм;
- отверстия Тб = 35 мкм.
Размеры заплечиков и канавок определены ГОСТ 20226 и зависят от радиуса закругления торца подшипника [1, табл. 4.14]. При радиусе 2 мм определим: высоту заплечика – 3,5 мм; глубину канавки - 0,3 мм; ширину канавки на валу - 2,4 мм; ширину канавки в корпусе – 3,0 мм.
Рабочие чертежи вала и корпуса представлены на рис. 1.14 и рис.1.15, а сборочный чертеж узла с подшипником на рис.1.16.
|
|
|
|
|
|
|
|



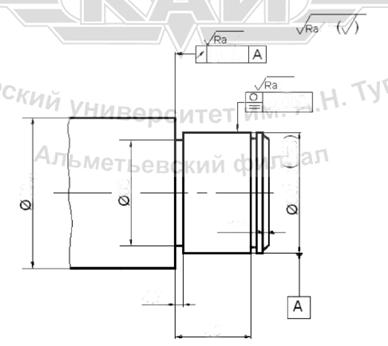
Рисунок 1.14 – Рабочий чертеж вала
|
|
|
|



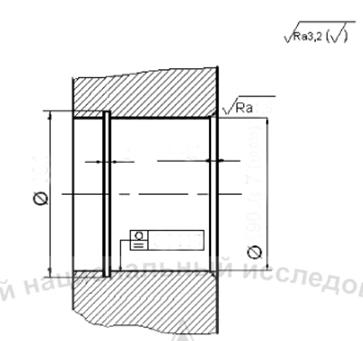
Рисунок 2.15 – Рабочий чертеж корпуса
Рисунок 1.16 – Сборочный чертеж узла с подшипником: 1) вал, 2) подшипник, 3) корпус, 4) крышка
1.2.5 Допуски размеров, входящих в
размерные цепи
На рис. 1.1 между крышкой 8 и подшипником 10 предусматривается тепловой зазор, величина которого обеспечивается расчетом размерной цепи.
Таблица 1.10
Карта исходных данных по расчету размерной цепи
Обозначения |
Наименования |
Размеры, мм |
A1 = A5 |
Высота буртиков крышек |
6 |
A2 = A4 |
Толщина прокладок |
2 |
A3 |
Размер корпуса |
216 |
A6 = A8 |
Монтажная высота подшипников |
23,75-0,25 |
A7 |
Длина шлицевой части ступени вала |
160 |
A∆ max |
Максимальный зазор |
3 |
A∆ min |
Максимальный натяг |
1 |
Составим схему размерной цепи (рисунок 1.17), методом замкнутого векторного потока
Рисунок 1.17 – Схема размерной цепи
Размерная цепь состоит из m=10 звеньев, включая и замыкающее
звено
;
;
– увеличивающие
звенья, n = 3
;
;
;
;
; – уменьшающие
звенья, p = 8, из них
k = 3 – стандартные звенья.
m = n + p +1 = 9.
Рассчитаем номинальный размер, допуск и предельные отклонения замыкающего звена:
(
+
+
) – (
+
+
+
+
) =
= (2 + 216 + 2) – (6 + 6 + 23,75 + 160 + 23,75 ) = 0,5 мм,
TΔ = A∆ max – A∆ min = 3 – 1 = 2 мм,
ESΔ = A∆ max – A∆ = 3 – 0,5 = 3,5 мм,
EIΔ = A∆ min – A∆ = 1 – 0,5 = 0,5 мм,
Замыкающее звено имеет
вид – A∆ = 0,5 .
Определим средний квалитет размерной цепи по среднему числу единиц допуска, приходящемуся на одно звено, включая стандартные (подшипники):
am=
Назначаем квалитет по расчётному значению аm [1, табл. 1.1]: принимаем 12 квалитет, (аm = 160).
Найдем стандартные поля
допусков по назначенным квалитетам для каждого размера. Основные отклонений
следует назначать так, чтобы допуск был направлен «в тело» детали, то есть в
зависимости от вида поверхности (размера): охватываемый, охватывающий,
остальные. Таким образом назначаем основные отклонения для размеров ;
;
;
как на основной
вал (h) и поле допуска h12, а на размеры ;
как на остальные (js) и поле допуска js12. Результаты
расчётов сводим в табл. 2.10.
![]() |
Согласовать расчетное поле допуска с заданным
Определить расчётное поле допуска замыкающего звена:
(0,12+0,12+0,1+0,1+0,46+0,4+0,25+0,25) =1,8.
Необходимо обеспечить выполнение условия: расчетный допуск замыкающего звена должен быть меньше или равен заданному допуску замыкающего звена. Если условие не выполняется, то требуется изменить точность одного или двух размеров, изменив квалитет.
По расчету получилось: ω∆< T∆ , т.е. 1,8 < 2. Разность ω∆ – T∆ = 0,2.
Для
более точного согласования допусков изменим квалитеты звеньев с 12-го на 13-ый.
Разница допусков при этом составит:
Для звена : IT12 – IT13 = 120 - 180
= 60 мкм.
Таким образом, ω’∆ = 1,86 ≈ 2.
Проверим соответствие предельных отклонений размеров составляющих звеньев требованиям замыкающего звена
(0 + 0+ 0) – ((-0,09)
+ (- 0,09) + (– 0,25) + ( – 0,4) + (– 0,25)) = 1,08 мм,
((- 0,1) + ( – 0,46)
+ ( – 0,1)) – (0.09 + 0,09 + 0,25 + 0 + 0,25 ) = = -1,34 мм.
Из сравнения видно, что
нижнее отклонение замыкающего звена A∆ = 0,5,
соответствует заданному A∆ = 0,5
, а верхнее не
соответствует. Для согласования предельных отклонений необходимо решить
обратную задачу. Для этого нужно в формулу для верхнего предельного отклонения
подставить требуемое значение и определить новое верхнее предельное отклонение
одного из составляющих звеньев, выбранного в качестве согласующего.
Возьмем для этой цели
звено , которое является
уменьшающим.
Выполним пересчет верхнего отклонения
звена
:
+2,5 = (0 + 0 + 0) – (-(0,09) + EIA5
+ ( - 0,25) + ( – 0,4) +
( – 0,25)) = 1,94 мм,
EIA5 = -1,51
+0,5 = ((-0,1 + (-0,46) + (-0,1))
– (0,09 + ESA5 + 0,25 + 0 + 0,25)
ESA5 = -1,75
Таким образом, для звена устанавливаем
нестандартное поле допуска
=
0,5
. Результаты
поэтапных и окончательных расчетов сводим в таблицу 1.10.
Таблица 1.10
Сводная таблица к расчету размерной цепи
Обозначение и вид |
Номинальный размер звена, мм |
Значение единицы допуска ij |
Принятые значения звеньев размерной цепи |
||
После назначения полей допусков по расчетному значению am |
После согласования значений допусков |
После согласования предельных отклонений |
|||
|
6 |
0,8 |
6Js12 (±0,06) |
6Js13 (±0,09) |
6Js13 (±0,09) |
|
2 |
0,6 |
2 h12(-0,1) |
2 h12(-0,1) |
2 h12(-0,1) |
|
216 |
2,9 |
216h12(-0,46) |
216h12(-0,46) |
216h12(-0,46) |
|
2 |
0,6 |
2 h12(-0,1) |
2 h12(-0,1) |
2 h12(-0,1) |
|
6 |
0,8 |
6Js12 (±0,06) |
6Js13 (±0,09) |
6Js13 (±0,09) |
|
23,75(±0,25) |
- |
23,75(±0,25) |
23,75(±0,25) |
23,75(±0,25) |
|
160 |
2,5 |
160h12(-0,4) |
160h12(-0,4) |
160h12(-0,4) |
|
23,75(±0,25) |
- |
23,75(±0,25) |
23,75(±0,25) |
23,75(±0,25) |
A∆ |
0,5 |
- |
- |
0,5 |
0,5 |
1.3 Нормирование точности соединений
сложного профиля
1.3.1 Нормирование точности метрической резьбы
Таблица 1.11
Карта исходных данных для метрической резьбы
Наименования исходных данных |
Значения исходных данных |
Условное обозначение резьбы |
М16x1,5 |
Номер позиции по чертежу |
18 |
Наименование деталей входящих в соединение |
Вал 1 |
Длина свинчивания |
N (нормальная) Свыше мм |
Действительный средний диаметр |
14,9 мм |
Накопленная погрешность шага |
∆PП = 15 мкм |
Погрешности угла профиля |
∆α/2пр = - 8 мин |
∆α/2лев = - 6 мин |
Расшифруем условное обозначение резьбы и определим ряд предпочтительности:
Резьба метрическая, номинальный диаметр d = 16 мм, шаг мелкий p = 1,5 мм. По ГОСТ 8724 [1, табл. 5.1] определяем ряд предпочтительности диаметров – второй.
Определим размеры резьбового соединения.
По ГОСТ 24705 [1, табл. 5.2] определяем основные размеры профиля резьбы в зависимости от шага:
- наружный диаметр резьбы: d = 16 мм;
- внутренний диаметр: D1 =d1 = d – 2 + 0,376 = 14,376 мм;
- средний диаметр: D2 = d2 = d – 1 + 0,026 = 15,026 мм;
- диаметр по дну впадин: d3 = d – 2 + 0,160 = 14,16 мм;
- теоретическая высота витка: H = 0,866 × P = 0,866 × 1,5 = 1,299 мм;
- рабочая высота витка: H1 = 0,541 × P = 0,541 × 1,5 = 0,8115 мм.
|
|
|
|
|



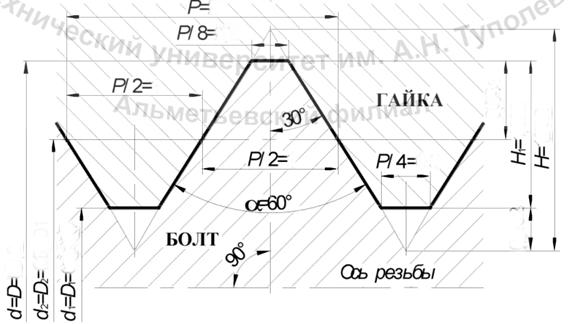
Рисунок 1.18 – Профиль резьбы
Назначим степень точности и поля
допусков на детали резьбового соединения.
Определим поля допусков резьбы по ГОСТ 16093 [1, табл. 5.8]. Учитывая, что средний класс точности по ГОСТ 16093 получил наибольшее распространение, и задана длинная свинчиваемость, выбираем предпочтительные поля допусков: резьбы болта – 6g; резьбы гайки – 6H.
Определяем числовые значения допусков и отклонений и заносим в табл. 1.12.
Таблица 1.12
Значение отклонений и допусков
резьбового соединения
Номинальный размер, мм |
Обозначение поля допуска |
Величина допуска T, мкм |
ES, мкм |
Наибольший предельный размер, мм |
EI, мкм |
Наименьший предельный размер, мм |
d = 16 |
6g |
236 |
- 32 |
15,968 |
-268 |
15,732 |
d2 = 15,026 |
6g |
140 |
- 32 |
14,994 |
-172 |
14,854 |
d1 = 14,376 |
- |
- |
- |
14,376 |
- |
- |
D = 16 |
- |
- |
- |
- |
0 |
16 |
D2 = 15,026 |
6H |
190 |
190 |
14,836 |
0 |
15,026 |
D1 = 14,376 |
6H |
300 |
300 |
14,076 |
0 |
14,376 |
Допуск среднего диаметра болта 6 степени: для диаметра 16 и шага 1,5 равен 140 мкм [1, табл.5.3].
Допуск среднего диаметра гайки 6 степени для диаметра 16 и шага 1,5 равен 190 мкм [1,табл.5.4].
Допуск наружного диаметра болта для 6 степени с шагом 1,5 равен 236 мкм [1, табл.5.5].
Допуск внутреннего диаметра гайки для 6 степени с шагом 1,5 равен 300 мкм [1,табл.5.5].
Основные отклонения диаметров болта es = -32 мкм, а для гайки EI = 0 [1, табл.5.6].
Рассчитать приведённый средний диаметр резьбы болта и сделать заключение о годности резьбы
Рассчитываем приведенный средний диаметр и строим схему расположения полей допусков по среднему диаметру (рис. 2.19) и по профилю (рис. 2.20):
d2пр = d2изм + (fp + fα)
Погрешность наклона боковой стороны половины угла профиля:
∆α/2пр =
мин,
Диаметральная компенсация погрешностей половины угла профиля fα:
fα = 0,36P × ∆α/2пр = 0,36 · 1,5 · 7 = 3,78 ≈ 4 мкм,
Диаметральная компенсация погрешностей половины угла профиля fp:
fp = 1,732P × ∆Pn = 1,732 · 15 = 25,98 ≈ 26 мкм,
d2пр = d2изм + (fp + fα) = 14,9 + (0,026 + 0,004) = 14,93 мм.
Условие годности резьбы по среднему диаметру для болта:
d2изм ≥ d2min; d2пр ≤ d2max;
Условие прочности выполняется:
14,9 ≥ 14,854.
Условие свинчиваемости также обеспечивается:
14,93 ≤ 14,994.
Таким образом, болт годен.
Рисунок 1.19 – Схема расположения полей допусков по среднему диаметру болта. D
|
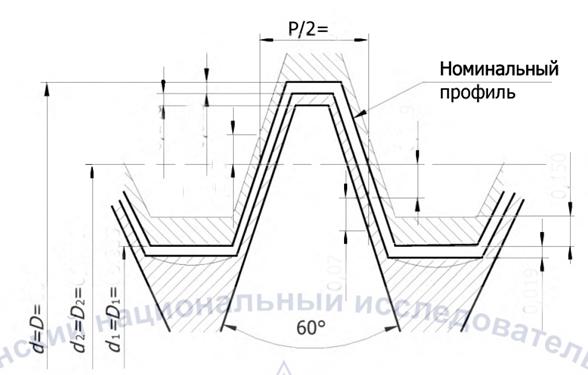
Рисунок 1.20 – Расположение полей допусков
по профилю резьбы болта 6g и гайки 6H
1.3.2 Нормирование точности шпоночных соединений
Таблица 1.13
Карта исходных данных шпоночного соединения
Наименования исходных данных |
Значения исходных данных |
Диаметр соединения d, мм |
42 |
Ширина и высота шпонки (ГОСТ 23360), b×h, мм |
12×8 |
Шпонка |
направляющая |
Тип производства |
серийное |
Количество шпонок в соединении |
одна |
Размеры шпоночного соединения определяем по ГОСТ 23360-78 [1, табл. 3.1].
d = 42 мм – диаметр вала;
b = 12 мм – ширина шпонки;
h = 8 мм – высота шпонки;
Smin = 0,4 – фаска;
S1 max = 0,4 – радиус закругления r или фаска;
l = 28…140 – интервал длин шпонки;
t1 = 5,0+0,2 – глубина шпоночного паза с отклонением на валу;
t2 = 3,3+0,2 – глубина шпоночного паза с отклонением во втулке;
Выбор посадок шпонки в пазы вала и втулки
Предельные отклонения шпонки:
- на ширину шпонки b = 12 h9 (-0,043);
- на высоту шпонки h = 8 h11 (-0,090);
- на длину шпонки l = 40 h14 (-0,62);
- на длину паза под шпонку на валу L = 40 H15 (+1).
Посадка шпонки в пазы вала и втулки зависит от типа производства и назначения шпонки. В данном соединении шпонка направляющая, соединение свободное, производство серийное.
Принимаем по [1, табл. 3.2]: паз вала - 12 H9(+0,043);
паз
втулки – 12 D10()
Рисунок 1.21 – Схема полей допусков по ширине шпонки
В соединении шпонки с валом Smin = 0; Smax = 0,086 мм; в соединении с пазом
втулки Smin = 0,05 мм; Smax = 0,17 мм, что обеспечивает
свободное перемещение зубчатого колеса вдоль вала.
Расчет допуска взаимного расположения шпоночного паза
Допуск параллельности равен 0,5Т9, а допуск симметричности Т9. Рассчитываем и округляем до стандартных значений [1, табл. 2.8 и 2.9], указываем на эскизах вала и втулки. T// = 0,5 · 43 = 21,5 мкм; по номинальной длине шпоночного паза, ближайший допуск – 20 мкм.
T= = 43 мкм, по номинальному диаметру ближайшим допуском будет 50 мкм. Допуск симметричности зависимый, т.к. производство серийное.
|
|
|
|
|
|
|
|


|
|
|
|
|
|
|
|
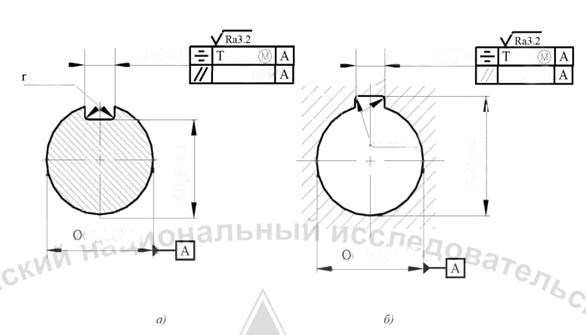
Рисунок 1.22 – Поперечные сечения: а) вала, б) втулки
|
|
|

|
|
|
|
|

|
|
|
|
|
|
|
|
|
|
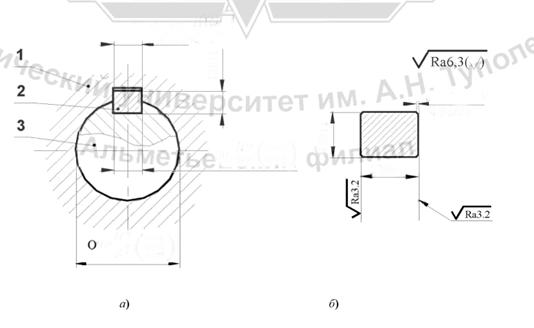
Рисунок 1.23 – Шпоночное соединение: а) поперечное сечение (1 – втулка, 2 – шпонка, 3 - вал), б) сечение шпонки
1.3.3 Нормирование точности шлицевых
соединений
Таблица 1.14
Карта исходных данных шлицевого соединения
Наименования исходных данных |
Значения исходных данных |
z × d × D, мм |
8 × 46 × 54 |
Соединение работает с реверсом или с вращением в одну сторону |
С реверсом |
Соединение вдоль оси подвижное или неподвижное |
неподвижное |
Шлицы в отверстии втулки: закалены или не закалены |
закалены |
Определим параметры шлицевого соединения:
z = 8 - количество шлиц;
d = 46 мм - внутренний диаметр шлиц;
D = 54 мм - наружный диаметр шлиц;
b = 9 мм - ширина шлиц;
с = 0,3+0,2 мм - фаска;
r = 0,3 мм - радиус закруглений
Шлицевое соединение 8 × 46 × 54 относится к легкой серии ГОСТ 1139 [1, табл. 3.3].
Выбор вида центрирования, назначение посадок
В зависимости от условий работы механизма (отсутствие реверса) и отсутствие закалки шлиц выбираем вид центрирования шлицевого соединения и назначаем посадку по ГОСТ 1139-80 [1, табл. 3.4]. Выбираем центрирование по наружному диаметру – D, так как втулка не закалена.
Назначаем посадки на элементы шлицевого соединения:
- по внутреннему диаметру
d: Ø 46 - посадка
предпочтительная;
- по наружному диаметру D: Ø 54
- посадка
предпочтительная;
- по ширине b: 9 - посадка
предпочтительная;
Таким образом, условная комплексная запись шлицевого соединения будет иметь вид:
D - 8 × 46 × 54
× 9
.
Строим схемы расположения полей допусков и рассчитываем предельные значения зазоров и натягов.
Рисунок 1.24 – Схема расположения полей допусков по наружному диаметру D
Рисунок 1.25 – Схема расположения полей
допусков по ширине b
Рисунок 1.26 – Схема расположения полей допусков по внутреннему диаметру d
|
|
|
|
|
|
|
|
|
|
|
|
|
|
Рисунок 1.27 – Поперечное сечение шлицевого
соединения: а) шлицевое соединение в сборке; б) сечение вала D-8×46f7×54
×9
; в) сечение втулки D-8×46 H7×54
H12×9
.
1.3.4. Нормирование точности цилиндрических зубчатых колес
Таблица 1.15
Карта исходных данных для зубчатой передачи
Наименования исходных данных |
Значения исходных данных |
Вид изделия |
Часть раздаточной коробки автомобиля |
Номер позиции по чертежу |
5 |
Межосевое расстояние а, мм |
120 |
Модуль зубчатой передачи m, мм |
4 |
Исходный контур |
ГОСТ 13755-81 |
Коэффициент смещения исходного контура x |
0 |
Окружная скорость V, м/с |
12 |
Число зубьев z |
24 |
Температура допустимого нагрева зубчатой передачи |
t1 = + 70ºC |
Температура допустимого нагрева корпуса |
t2 = + 60ºC |
Определяем геометрические параметры зубчатого колеса
Диаметр делительной окружности d = m · z = 4 · 24 = 96 мм.
Диаметр окружности выступов dа = d + 2 · m = 96 + 2 · 4 = 104 мм;
Диаметр окружности впадин df = d - 2,5 · m = 96 - 2,5 · 4 = 86 мм;
Диаметр основной окружности dа = d · cos α = 96 · cos 20º = 90,24 мм;
Ширина зубчатого венца b = 10· m = 10 · 4 = 40 мм;
Количество охватываемых зубьев при измерении длины общей нормали zw = 3;
Длина общей нормали W = 4 · 7,716 = 30,864 мм.
Назначим степень точности зубчатой передачи
Передача является кинематической. В этом случае наиболее важной является кинематическая точность, она назначается на одну степень точнее, чем нормы плавности и контакта зубьев.
По заданной окружной скорости,
согласно [1, табл.6.3], рекомендуется степень точности по нормам плавности –
6.
Принимаем степень кинематической точности – 5, степень точности по нормам контакта зубьев – 6.
Вид сопряжения определяется наименьшим гарантированным боковым зазором jn min. Гарантированный боковой зазор получается как сумма:
jn min ≥ jn1 + jn2
Для кинематической передачи jn1 = 0,01 m = 0,01 · 4 = 0,04 мм.
Боковой зазор соответствующей температурной компенсации определяется но формуле:
jn2 = a [α1 · (t1 – 20º) – α2 (t2 – 20º)] · 2 sin α ,
где а – межосевое расстояние в передаче, мм;
α1 и α2 – коэффициенты линейного расширения для материалов зубчатых колес и корпуса;
t1 и t2 – предельные температуры, для которых рассчитывается боковой зазор, для зубчатых колес и корпуса соответственно.
При t1 = + 70ºC, t2 = + 60ºC, α1 = 11,5 · 10-6 (для закаленной стали), α2 = 23 · 10-6 (для чугуна) получим:
jn2 = 120 [11,5 · 10-6 · (70º – 20º) – 23 · 10-6 (60º – 20º)] · 2 sin 20º = -0,028 мм.
jn min = 0,04 + (-0,028) =0,012 мм.
Определяем вид сопряжения D с учетом межосевого расстояния в передаче по [1, табл. 6.4].
Полное обозначение точности передачи:
5–6–6–D ГОСТ 1643
Определим исполнительный размер длины общей нормали
Верхнее отклонение EWs = 10 мкм по [1, табл. 6.10] для вида сопряжения D, 6-й степени точности, d = 96 мм.
Допуск на длину общей нормали TW = 40 мкм по [1, табл. 6.11] для Fr= 28 мкм [1, табл. 6.6].
Нижнее отклонение EWi = |EWs| + TW = 10 + 40 = 50 мкм.
Исполнительный размер
длины общей нормали – W =
30,864 .
Определим требования к базовым поверхностям зубчатого колеса.
Требования к точности заготовок под операцию зубонарезание определяются по рекомендациям (1, табл. 6.14].
Базовое отверстие должно
быть выполнено по 6-му квалитету: Ø54H6 , так
как по нормам плавности 6-я степень.
Диаметр вершин зубьев
используется по 2-му варианту (как измерительная база для выверки заготовки на
станке), следовательно, его точность - Tda = 0,01 · m = 0,04 мм; Ø104 h7
Допуск на радиальное биение по вершинам зубьев: Fd = 0,6 · Fr = 0,6 · 28 = 16,8 мкм.
Принимаем Fd = 20 мкм по [1, табл.2.9(гл.2)].
Торцовое биение базового торца на диаметре 0,75d = 0,75 · 96 = 72 мм находим расчетом, определив Fβ = 9 мкм, по [1, табл.6.9]:
FT = (0,5·Fβ·dб)/В = (0,5·9·72)/40 = 8,1 мкм, по [1, табл. 2.9] принимаем FТ = 16 мкм.
Все расчетные параметры указываем на чертеже зубчатого колеса (рис 1.28).
Выбираем контрольный комплекс зубчатого венца
Учитывая, что плавность работы и контакт зубьев заданы по 6-й степени, выбираем 1-й комплекс. Для контроля кинематической точности зубчатого колеса принимаем кинематическую погрешность зубчатого венца F"i. Числовые значения F"i определяются как сумма: F"i = Fp + ff. Накопленная погрешность шага зубчатого колеса Fp = 32 мкм [1, табл.6.5].
Погрешность профиля зуба ff = 8 мкм [1, табл. 6.7], следовательно, F"i = 32 + 8 = 40 мкм. Контрольный комплекс и необходимые приборы указаны в табл. 1.16.
![]() |
Контрольный комплекс для зубчатой
передачи 5–6–6–D
Наименование контролируемых параметров |
Обозначение допусков |
Допускаемые значения, мкм |
Применяемые средства измерения |
|
Колебание длины общей нормали |
FvW |
22 |
Нормалемер |
|
Длина общей нормали, мм |
W |
W = 30,864 |
||
Допуск на длину общей нормали |
TW |
40 |
||
Кинематическая погрешность зубчатого колеса |
F"i |
40 |
Прибор для однопрофильного контроля |
|
Местная кинематическая погрешность зубчатого колеса |
f"i |
18 |
||
Погрешность эвольвентного профиля |
ff |
8 |
Эвольвентомер |
|
Суммарное пятно контакта, % |
По высоте |
- |
50 |
Контрольно-обкатный станок |
По длине |
- |
70 |
||
Погрешность направления зуба |
Fβ |
9 |
Ходомер |
|
На корпус передачи |
||||
Отклонение от параллельности осей |
fx |
9 |
Специальное приспособление для контроля расположения отверстий в корпусе |
|
Перекос осей |
fy |
4,5 |
||
Предельные отклонения межосевого расстояния |
±fa |
28 |
Для контроля точности по нормам
плавности принимаем местную кинематическую погрешность зубчатого колеса f"i = 18 мкм [1, табл.6.7].
Измерение обоих параметров производится на приборе для однопрофильного контроля.
По нормам контакта зубьев принимаем Fβ для колеса (прибор ходомер), а для передачи fx и fy: Fβ =fx = 9 мкм; fy = 4,5 мкм [1, табл.6.9].
Контроль контакта зубьев также может быть выполнен по суммарному пятну контакта, которое составит для 6-й степени точности 50% по высоте зубьев и 70% по ширине зубьев [1, табл. 6.9].
Нормы бокового зазора косвенно оцениваются по предельным отклонениям межосевого расстояния fa = ±28 мкм [1, табл. 6.4] или по измерению длины общей нормали нормалемером.
1.2.4 Выбор универсальных средств измерений
Таблица 1.17
Карта исходных данных по выбору средств измерения
Наименования исходных данных |
Значения исходных данных |
Контролируемая поверхность |
отверстие |
Исполнительный размер D3 |
Ø 68 |
Коэффициент
технологической точности |
4,5 |
Тип производства |
серийное |
Выбрать универсальное средство измерения для цехового контроля Выбор средств измерений зависит (СИ) от ряда факторов:
- организационно экономических (тин
производства, вид взаимозаменяемости, стабильность технологического процесса,
стоимость, наличие СИ и др.);
- конструкторских параметров изделия (габариты, масса, жесткость, вид контролируемой поверхности и др.);
- метрологических (пределы и диапазон измерения, цена деления, класс точности, погрешность СИ и др.).
Универсальные СИ находят широкое применение во всех типах производств, так как имеют низкую себестоимость.
Произведем выбор СИ по метрологическим факторам, учитывая, что контролируется отверстие. Считаем, что некоторые систематические погрешности (температурная, погрешность базирования и др.) устранены до начала процесса измерения. Допускаемая погрешность метода измерения должна быть больше неисключенной систематической погрешности СИ. По ГОСТ 8.051 определим для размера 68 допуск на изготовление (IT) и допускаемую погрешность измерения (δ), согласно [1, табл. 7.1]:
IT = 0,030 мм; δ = 9 мкм.
Выбираем возможное измерительное средство: [1, табл.7.2]. Это код 18 - нутромер индикаторный НИ-70 ГОСТ 9244 со следующими техническими характеристиками:
- цена деления отсчетного устройства: i = 0,001мм;
- предельная погрешность измерительного средства: Δ = 5,5 мкм;
Метод измерения прямой, контактный, относительный.
Для настройки на ноль требуются концевые меры длины 3-го класса точности.
Определим значения параметров разбраковки. Оценка влияния погрешностей измерения на результаты разбраковки выполняется по относительной томности метода измерения:
Амет(σ) = σмет · 100/ IT = 2,8 · 100/ 30 ≈ 10% ,
где σмет=Δ/2=5,5/2=2,8
мкм - среднее квадратичное отклонение погрешности измерения принятого средства
измерения.
Для 7-го квалитета стандарт рекомендует принять Амет = 16%.
По заданному коэффициенту
технологической точности =
4,5 по графикам [1, рис. 7.1) определяем
параметры разбраковки:
- необнаруженный брак (риск заказчика) m = 1,2%;
- ложный брак (риск изготовителя) n = 4,3%;
- вероятностный выход размера за границу поля допуска с/IT = 0,1 %, C = IT · с/IT = 30 · 0,1 ≈ 3 мкм.
Оценка годности деталей производится по предельно допустимым размерам:
Dmax = 68,030 мм; Dmin = 68, мм.
Среди годных деталей могут оказаться бракованные детали (не более 1,2 %), у которых размеры выходят за границы поля допуска на величину до 3 мкм. Это риск заказчика. Риск изготовителя не более 4,3 %.
Выполнить расчет производственного допуска. Принимаем условие недопустимости риска заказчика при Δ>δ и проводим расчет производственного допуска для измерения СИ по коду 17. Это индикаторный нутромер НИ-70 ГОСТ 868, который имеет цену деления индикатора 0,01 мм и предельную погрешностью Δ =20 мкм:
TПР = IT – 2 · C = 30 – 2 · 3 = 24 мкм
Предельно допустимые размеры с учетом производственного допуска:
Dmax = 60,030-0,03 = 68,027 мм;
Dmin = 68 + 0,03 = 68,003 мм
Варианты установления приемочных границ даны на рис. 3,29.
Выбор средств измерения для арбитражной перепроверки. При разногласиях между рабочим и контролером требуется арбитражная перепроверка.
Допускаемая погрешность при
арбитражной перепроверке:
Δарб= 0,3 · δ = 0,3 · 9 = 2,7 мкм.
Выбираем измерительное средство с кодом 21 [1, табл. 7.2]. Пневмопробки с отсчетным прибором с ценой деления 0,0005 мм и предельной погрешностью 3 мкм. Настройка прибора производится по установочным кольцам. Метод измерения: относительный, прямой, бесконтактный.
Заключение
В результате выполнения курсовой работы выполнено следующее:
- при нормировании точности гладких соединений подобраны посадки методом подобия, назначены посадки расчетным методом, выполнен контроль размеров гладкими калибрами, рассчитаны допуски и назначены посадки подшипников качения на вал и корпус, определены допуски размеров, входящих в размерные цепи;
- при нормировании точности соединений сложного профиля проведено нормирование точности метрической резьбы, шпоночных и шлицевых соединений, цилиндрических зубчатых колес;
- произведен выбор универсальных средств измерений.
Список используемой литературы
1. Егорова Е.И., Д.Н. Ларионов, Д.О. Фирстов Нормирование точности в машиностроении. Методические указания по выполнению курсового проекта. – Алметьевск, 2012.
2. Кайнова В.Н., Гребнева Т.Н. Нормирование точности изделий в машиностроении.
3. Анухин, В.И. Допуски и посадки [Текст]: Учебное пособие для вузов / В.И. Анухин. – СПб.: Питер, 2004. – 208 с.
4. Радкевич, Я.М. Метрология, стандартизация и сертификация [Текст]: Учеб. для вузов / Я.М. Радкевич, А.Г. Схиртладзе, Б.И. Лактионов. – М.: Высш. шк., 2004. 767 с.: ил.
5. Торопов, Ю.А. Припуски, допуски и посадки гладких цилиндрических соединений. Припуски и допуски отливок и поковок [Текст] / Ю.А. Торопов. – СПб.: Профессия, 2007. – 688 с.
6. Никифоров, А.Д. Взаимозаменяемость, стандартизация и технические измерения [Текст] / А.Д. Никифоров. – М.: Высш. шк., 2007. – 510 с.
7. Палей, М.А. Допуски и посадки [Текст]: Справочник в 2-х ч. – Ч.1./ М.А. Палей, А.Б. Романов, В.А. Брагинский. – СПб.: Политехника, 2001. – 558 с.
8. Палей, М.А. Допуски и посадки [Текст]: Справочник в 2-х ч. – Ч.2./ М.А. Палей, А.Б. Романов, В.А. Брагинский. – СПб.: Политехника, 2001. – 558-1184 с.
![]() |