Федеральное агентство железнодорожного транспорта
Федеральное государственное бюджетное образовательное учреждение
высшего образования
Омский государственный университет путей сообщения
(ОмГУПС, (ОмИИТ))
Кафедра «Локомотивы»
ИЗУЧЕНИЕ ПОКАЗАТЕЛЕЙ НАДЕЖНОСТИ
КОЛЕНЧАТЫХ ВАЛОВ И ИХ ПОДШИПНИКОВ
Тематический реферат
по дисциплине «Надежность подвижного состава»
Выполнил: студенты гр. 32 А
____________И.А. Алексеев
____________А.Ф. Левченко
_____________Р.С. Кузнецов
Руководитель –
к.т. н., доцент кафедры «Локомотивы»
______________Д. В. Балагин
Омск 2016
Оглавление
Введение. 3
1. Назначение, конструкция и техническая характеристика коленчатых валов и их подшипников на примере дизеля Д100. 4
2. Характеристика работ при техническом обслуживании и текущих ремонтах коленчатых валов. 6
3. Виды повреждений коленчатых валов рядных и V-образных дизелей. 8
4. Методы повышения предела выностливости и изнсостойкости коленчатых валов 13
5. Анализ проблемы надежности подшипников. 15
Библиографический список. 19
ВВЕДЕНИЕ
Коленчатый вал дизеля работает в очень сложных и тяжелых условиях. Он испытывает значительные усилия давления газов, передающиеся шатунно-поршневым механизмом, от сил инерции поступательно и вращательно движущихся масс, а также усилия моменты, возникающие вследствие крутильных колебаний.
Учитывая сложность изготовления большую трудоемкость при замене коленчатых валов, к материалу и качеству их изготовления предъявляют высокие требования. Коленчатые валы дизелей изготовляют из стали ковкой или штамповкой либо из высокопрочного чугуна путем отливки. Стальные валы более надежны в эксплуатации, но трудоемки в изготовлении. Поэтому на тепловозах получили распространение литые валы из высокопрочного модифицированного чугуна (дизели типов Д100, Д49). За счет уменьшения отходов на их изготовление затрачивается в три раза меньше металла, чем на изготовление стальных валов. (При изготовлении стального вала дизеля ПД1М из заготовки массой 13 т в отходы идет около 86 % металла.)
Изготовление коленчатых валов литьем позволяет с наименьшими затратами получить наиболее приемлемую форму щек кривошипов и более рациональное распределение металла за счет выполнения коренных и шатунных шеек пустотелыми, что уменьшает массу валов при сохранении относительно высокой прочности. Для повышения прочности вала на изгиб галтели шеек вала специально упрочняют накаткой роликами. Шейки коленчатого вала дизелей типа Д49 азотируют для повышения износостойкости.
1. НАЗНАЧЕНИЕ, КОНСТРУКЦИЯ И ТЕХНИЧЕСКАЯ ХАРАКТЕРИСТИКА КОЛЕНЧАТЫХ ВАЛОВ И ИХ ПОДШИПНИКОВ НА ПРИМЕРЕ ДИЗЕЛЯ Д100
Коленчатый вал вращающееся звено кривошипного механизма, состоящее из нескольких соосных коренных шеек, опирающихся на подшипники, и 1 или нескольких колен, каждое из которых составлено из 2 щек и 1 шейки, соединяемой с шатуном.
Коленчатый вал вместе с блоком цилиндров является важнейшей базовой деталью дизеля, в значительной степени, определяющей срок его службы. Основными неисправностями коленчатых являются: сверхнормативный шеек; трещины и изломы, которые могут быть следствием нарушений при изготовлении или ремонте вала, в частности неправильной установки в подшипниках; выкрашивание, коррозия и износ баббитовой заливки вкладышей; износ вкладышей и потеря торцового натяга; трещины крышек кодах подшипников.
У дизелей типа Д100при техническом обслуживании ТО-3 открывают верхней крышки блока и картера, убеждаются в отсутствии частиц баббита вблизи подшипников и трещин крышках, проверяют крепление гаек подшипников путем их остукивания молотком, состояние шплинтов. Шплинты в прорезях гаек должны сидеть плотно, а их концы должны быть разведены в горизонтальной плоскости. Определяют плотность посадки вкладышей в подшипниках положению стыков вкладышей, которые должны совпадать с плоскостью разъема крышки подшипника. Кроме того, плотность посадки контролируют путем обстукивания боковых поверхностей вкладышей медным молотком, прикладывая при этом пальцы руки к вкладышу и корпусу подшипника.
Осматривают маслопровод в картере и трубки, подводящие масло на смазку подшипников. Через одно ТО-3 вверяют провисание нижнего коленчатого вала для коренных шеек с 1-й 7-ю, которое не должно превышать 0,005 мм.
Рис.1- Общий вид
коленчатого вала
2. ХАРАКТЕРИСТИКА РАБОТ ПРИ ТЕХНИЧЕСКОМ
ОБСЛУЖИВАНИИ И ТЕКУЩИХ РЕМОНТАХ
КОЛЕНЧАТЫХ ВАЛОВ
Коленчатый вал в паре с блоком цилиндров являются основными базовыми деталями, определяющими срок службы дизеля. Поэтому вопросам их содержания, ухода и качественного ремонта придается большое значение. Исправная работа коленчатого вала с подшипниками зависит от правильности укладки коленчатого вала, состояния поверхности его шеек и вкладышей, подачи смазки в нужном количестве и необходимого качества и других условий. Основными неисправностями коленчатых валов являются: излом вала по шейкам или щекам (рис. 1), трещины в шейках вала, чаще по галтели, задир шеек вала, повышенная овальность коренных или шатунных шеек, повреждения элементов соединения вала с антивибратором, приводом насосов и распределительных валов, изгиб вала.
Рис. 2 – Излом коленчатого вала по щеке
Причинами излома коленчатых валов являются: высокий уровень знакопеременных напряжений от изгиба или крутильных колебаний вала, литейные дефекты и дефекты обработки вала (рыхлоты, пористости, плены, подрезы). Повышение уровня напряжений на изгиб в шейках и щеках вала происходит в результате образования ступенчатости смежных опор, увеличенного изгиба вала, нарушения уравновешенности вала (неправильный подбор поршней и шатунов по массе).
Изгиб вала бывает двух видов: упругий и остаточный. Упругий изгиб вала происходит под действием сил, действующих от шатунов и вала якоря тягового генератора, при неправильной укладке коленчатого вала в постелях блока и нарушении центровки валов: коленчатого и якоря генератора.
Остаточный изгиб коленчатого вала образуется в результате неправильной шлифовки коренных шеек (несоосность шеек) или релаксации остаточных внутренних напряжений, а также неправильной укладки вала при его хранении.
При техническом обслуживании ТО-3 и текущем ремонте ТР-1 через открытые люки блока и картера проверяют: нет ли частиц баббита вблизи подшипников, трещин в крышках, крепления гаек коренных и шатунных подшипников коленчатого вала, положение стыков вкладышей (нет ли проворота), состояние шплинтов. При техническом обслуживании ТО-3 и текущих ремонтах проверяют целостность масляного коллектора и маслоподводящих трубок. При этом прокачку масла маслопрокачивающим насосом производят от постороннего источника тока.
Зазором «на масло» называют суммарный зазор между шейкой вала и вкладышами подшипника (верхним и нижним). При отсутствии провисания шейки вала весь зазор «на масло» будет расположен между шейкой вала и верхним вкладышем. Эти зазоры измеряют щупом вдоль оси вала в вертикальной плоскости с двух сторон (со стороны генератора и со стороны отсека управления), суммируют замеренные зазоры и делят сумму на два. Суммарный зазор «на масло» в опорных и упорном подшипниках дизеля типа Д100 должен быть 0,15—0,23 мм, при выпуске тепловоза из текущего ремонта ТР-3 — 0,15—0,30, из текущего ремонта ТР-2 — 0,15—0,35, из текущего ремонта ТР-1 и технического обслуживания ТО-3 — не более 0,45 мм.
3. ВИДЫ ПОВРЕЖДЕНИЙ КОЛЕНЧАТЫХ ВАЛОВ РЯДНЫХ И V-ОБРАЗНЫХ ДИЗЕЛЕЙ
Несмотря на низкий процент поломок и отбраковки по трещинам коленчатых валов, их абсолютное количество, заменяемое новыми, ежегодно достигает нескольких сотен. Большинство отбракованных коленчатых валов тепловозных дизелей является валами рядных дизелей типа Д100.
Анализ статистических данных, поступающих от тепловозо-ремонтных заводов и линейных мастерских (локомотивных депо), показывает, что большинство трещин и поломок коленчатых валов имеют усталостный характер и чаще всего возникают в галтелях, т. е. в сопряжении шейки со щекой. При продолжительной работе вала с такими трещинами они распространяются на щеки с выходом на противоположные галтели.
Большой опыт эксплуатации этих валов на магистральных тепловозах показывает, что трещины и места поломок валов распределяются хотя и неравномерно, но по всем без исключения шейкам и щекам, т. е. по всей длине вала (рис.3) и это дает основание считать, что коленчатые валы дизелей типа Д100 являются достаточно равнопрочной конструкцией. Анализ причин разрушения, а также расчет коленчатого вала на прочность подтвердили указанный вывод.
Было также установлено, что разрушение валов происходит как при малых, так и при сравнительно больших пробегах тепловоза, т. е. при малых и больших износах коренных шеек и коренных вкладышей. Однако большая часть разрушений имела место после длительной работы дизеля, соответствующей четырем-пяти годам работы тепловоза.
Исследования большого количества изломов показали, что лишь небольшой процент общего числа поломок зависит от дефектов литья в виде пористости, шлаковых включений, плен и т. п. Изломы по перечисленным причинам происходят в основном на ранней стадии работы вала, т. е. при пробеге тепловоза 50—150 тыс. км, что соответствует первому году работы дизеля.
Большая часть поломок валов, кроме случаев хрупких разрушений, вызванных повреждениями смежных узлов дизеля, происходит из-за низкого предела выносливости всего вала, который, как показали испытания натурных валов до их упрочнения, не превышает 350 МПа. Разрушения такого характера происходят после возникновения неравномерного по длине вала износа рабочих вкладышей коренных подшипников или коренных шеек и образования завышенной суммарной ступенчатости между смежными коренными шейками вала.
По данным статистики, установлено, что наибольший процент поломок коленчатых валов дизеля типа ДЮО происходит по щекам 19 и 20 верхнего коленчатого вала. Из общего количества верхних коленчатых валов, вышедших из строя по трещинам и поломкам, 55—60% приходится на валы, забракованные по указанным двум щекам. Значительное количество разрушений верхних и нижних коленчатых валов встречается в щеках 14, 15, 16 и 6, 7, 8 обоих валов (см. рис. 3).
Изучение характера и причин разрушения валов по этим сечениям показало, что почти во всех случаях они связаны с интенсивным износом рабочих канавочных коренных вкладышей соответствующих шеек. Эта выработка вкладышей всегда предшествует возникновению трещин вала. Возникновение усталостных трещин может быть только на тех шейках, где суммарная разница (ступенчатость), состоящая из износа смежных коренных рабочих вкладышей и соответствующих коренных шеек, достигает значительных величин. Дальнейшее развитие трещин снижает жесткость вала по данному сечению и увеличивает интенсивность износа соответствующих вкладышей. Нередко можно видеть, что при длине трещины 100 мм и более разница в толщинах вкладышей уже достигает 0,3—0,5 мм и более.
![]() |
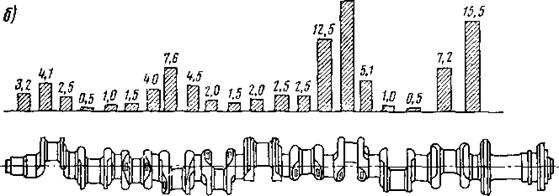
Частые разрушения нижнего вала в щеках 19, 20 имеют другую причину. Эти разрушения вызваны не столько разницей в интенсивности износа смежных рабочих вкладышей коренных шеек 10 и 11, сколько износом рабочих вкладышей шейки 12. Установлено, что рабочий вкладыш коренной шейки 12 нижнего вала изнашивается в несколько раз интенсивней, чем шейки 11. Вследствие этого ступенчатость между 11-й и 12-й опорами вала в период работы дизеля до первой переборки (текущего ремонта тепловоза) только по вкладышам достигает 0,1—0,15 мм (при норме 0,08), причем опора 11 всегда оказывается выше опоры 12. Это происходит в связи с тем, что коренная шейка 12 нижнего вала поддерживает тяжелый ротор тягового генератора. Под действием веса ротора эта шейка всегда находится прижатой к нижнему (рабочему) вкладышу, что и вызывает изгиб вала на участке коренных шеек 10—12 с провисанием его на опоре 10. Такое провисание достигает порядка 0,12—0,16 мм и более и складывается из износа шейки и вкладыша этой опоры. При работе дизеля под действием цилиндровых сил это провисание полностью выбирается, что приводит к циклическому знакопеременному изгибу на участке щек 19—20. Такой изгиб коленчатого вала способствует возникновению и развитию по указанным сечениям усталостных трещин и изломов коленчатого вала. Как и в предыдущем случае, такие трещины развиваются по галтелям коренных шеек с выходом через щеку на галтель шатунной шейки 10.
Сокращение числа поломок вала по коренным шейкам 10 и 11 может быть достигнуто недопущением в эксплуатации ступенчатости, превышающей 0,08 мм между вкладышами 11 и 12, а также опорами 10 и 11, т. е. своевременной заменой рабочих вкладышей этих постелей.
Важным фактором, способствующим сокращению таких поломок, является и соблюдение соосности якоря тягового генератора и коленчатого вала на всем протяжении эксплуатации тепловоза. Эта несоосность контролируется разностью в толщине эластичной муфты тягового генератора вверхней и нижней ее частях. Большая величина разнотолщинности свидетельствует о значительном износе шейки 12 нижнего коленчатого вала и ее рабочего вкладыша, т. е. о нарушении соосности якоря и коленчатого вала.Исследования напряженного состояния изношенных коленчатых валов дизелей типа Д100 показали, что при суммарной ступенчатости по смежным опорам вала, равной 0,14 мм, запас прочности снижается на 25%, а при ступенчатости 0,53 мм — почти в 2 раза. Ориентировочно можно считать, что наличие суммарной ступенчатости по смежным опорам, равной расстоянию между серединами двух смежных коренных шеек, приводит к снижению запаса прочности этого вала на 100%.
Таким образом, строгое соблюдение установленных допусков на износ коренных шеек вала и коренных рабочих вкладышей способствует значительному снижению числа случаев поломок коленчатого вала.
4. МЕТОДЫ ПОВЫШЕНИЯ ПРЕДЕЛА ВЫНОСТЛИВОСТИ И ИЗНСОСТОЙКОСТИ КОЛЕНЧАТЫХ ВАЛОВ
Повысить прочность коленчатых валов можно путем поверхностного упрочнения.
В практике дизелестроения существуют хорошо зарекомендовавшие себя способы упрочнения коленчатых валов, изготовленных из высокопрочного чугуна с глобулярным графитом, к которым относятся прежде всего накатывание (пластическая деформация) галтелей роликами, азотирование, а также хромирование рабочих поверхностей шеек.
Накатывание роликами галтелей чугунных коленчатых валов, изготовленных из ВПЧ, повышает их предел выносливости на 50% и более.
На заводе «Русский дизель» чеканка галтелей крупных многоопорных стальных коленчатых валов значительно увеличила их надежность. Для упрочняющей обработки этих валов был применен метод поверхностного упрочнения при помощи вибрирующего ролика. Кроме того, для повышения износостойкости и предела выносливости коленчатых валов из высокопрочного чугуна широкое распространение получило азотирование. Установлено, что предел выносливости образцов, вырезанных из натурных коленчатых валов, в результате их азотирования повышается со 165 до 355 МПа, т. е. в два с лишним раза. Однако горячая правка образцов снижает их предел выносливости с 355 до 255—235 МПа, т. е. на 28—34%, в зависимости от остаточной стрелы прогиба после правки.
Процент снижения предела выносливости на образцах может быть отнесен и к натурным коленчатым валам, так как в процессе правки вала на поверхности его шеек, особенно в местах концентрации напряжений, могут возникнуть остаточные растягивающие напряжения, а также микротрещины.
Чтобы избежать прогиба вала во время его азотирования, в настоящее время разработан такой технологический процесс, который предусматривает вращение вала в период всего цикла азотирования, что почти полностью исключает необходимость его правки.
Как показывает практика применения различных методов поверхностного упрочнения шеек валов против износа, хорошие результаты дает хромирование, которое наряду с повышением износостойкости шеек уменьшает интенсивность нарастания ступенчатости между соседними опорами вала, снижает величину изгибающих моментов и замедляет усталостные процессы. Хромирование не вызывает коробления вала, что очень важно при его упрочнении. Однако этот способ упрочнения валов дизелей большой и средней мощности не получил широкого распространения из-за высоких затрат на его выполнение. Но учитывая успехи физики металлов и гальванотехники, значительное увеличение производства электроэнергии и хромового ангидрида признано целесообразным; для дизелей малой мощности более широко применять хромирование как при изготовлении новых валов, так и при их ремонте.
5. АНАЛИЗ ПРОБЛЕМЫ НАДЕЖНОСТИ ПОДШИПНИКОВ
«ВНИИЖТом» был выполнен анализ проблемы надёжности подшипников дизелей тепловозов. В результате исследований была выявлена связь дефектов подшипников с параметрами дизеля и системы охлаждения, а также с нововведениями, реализованными изготовителями в целях повышения топливной экономичности. Предложенные для устранения дефектов технические решения были рассмотрены заказчиком, специалисты которого в дальнейшем контролировали выполнение согласованных мероприятий.
Увеличение интенсивности впрыска топлива путём применения шайб топливных насосов высокого давления (ТНВД) с «вогнутым» профилем при одновременном повышении максимального давления сгорания 7,0 до 8,2 МПа вызвало увеличение удельных давлений в шатунных и коренных подшипниках. Критерием механической нагруженности шатунных подшипников коленчатого вала является значение максимальной нагрузки на подшипник, отнесённое к площади проекции подшипника на плоскость, нормальную направлению усилия:
Р = р2 х F/ D х L,
где pz - максимальное давление сгорания в цилиндре дизеля;
F - площадь поршня;
D, L - диаметр и ширина рабочей поверхности вкладыша подшипника соответственно.
При максимальном давлении сгорания pz, равном 8,2 МПа, величина среднего удельного давления Р в шатунных подшипниках достигла 19,4 МПа вместо 15,6 МПа при pz = 7,0 МПа. Увеличение нагруженности подшипников на 18% не могло не сказаться на их работоспособности, поскольку рекомендуемые значения среднего удельного давления для вкладышей с заливкой баббитом БК2 не превышают 14,0 - 15,0 МПа.
При работе на 7 и 8 позициях контроллера машиниста средние значения удельных давлений превысили указанный предел. Поэтому было рекомендовано понижение максимального давления сгорания до 7,5 - 7,7 МПа путём уменьшения угла опережения подачи топлива, поскольку в этом случае снижается и скорость нарастания давления в цилиндре при сгорании - «жёсткость» рабочего процесса.
Снижение максимального давления сгорания восстановило соответствие уровня механической нагруженности подшипников физическим свойствам материала антифрикционного слоя при температурах, на превышающих 90 0С. Поскольку уменьшение опережения впрыска топлива увеличивает кпд дизеля на режимах с низкими и средними частотами вращения коленвала, эксплуатационный расход топлива тепловозов, работающих на маневровых режимах, при этом не возрастает.
Анализ температурных условий работы подшипников, в том числе непосредственные измерения температуры баббита в зоне несущего масляного клина, выполненные в условиях заводского дизельного стенда, показали, что повышение температуры масла в несущем слое подшипника по отношению к температуре поступающего масла, составляет 20 - 22 0С. При температуре масла на входе в подшипники, равной 80 - 85 0С, рабочая температура антифрикционного слоя может превышать 100 - 105 0С, т. е. быть на 10 - 15 0С выше уровня, допустимого для баббита БК2.
ОАО ВНИКТИ было предложено ограничить рабочую и максимальную температуру масла на входе в двигатель величинами соответственно 70 0С и 75 0С, для чего на всех тепловозах типа ТЭМ18(Д, ДМ) в эксплуатации релейная система регулирования температуры масла была дооборудована. На тепловозах новой постройки охладители масла дизеля включены в холодный контур охлаждения дизеля, что исключило возможность превышения установленного ограничения температуры масла. Было установлено, что указанное ограничение температуры должно строго соблюдаться так же при ручном управлении системой охлаждения, допускаемом в случае нештатных ситуаций.
Рост температуры в нагруженной зоне подшипника вследствие тепловыделения, равный 20 - 22 0С, мог быть ограничен увеличением протока масла через подшипник. С этой целью были предложено и реализовано увеличение давления масла на входе в дизель путём увеличения затяжки пружины стравливающего клапана нагнетательной масляной магистрали. Открытие клапана при давлении 0,3 МПа ограничивало расход масла через подшипники дизеля при работе на верхних позициях контроллера. Повышение давления открытия клапана до 0,45 - 0,50 МПа сократило бесполезный слив масла в масляную ванну. Проток масла через подшипники был увеличен на 10 -15 %, что способствовало увеличению теплоотвода и стабилизации масляного клина в подшипниках.
На вновь изготавливаемых дизелях были в два раза увеличены проходные сечения трубок, подводящих масло из нагнетательного канала к коренным подшипникам коленчатого вала. Установка реле остановки дизеля по давлению масла в конце масляной магистрали изменена с 0,15 до 0,18 МПа.
Снижение температуры масляного слоя в подшипниках повысило вязкость масла и толщину несущего масляного клина. Механические свойства антифрикционного сплава в нагруженной зоне подшипника также улучшились. По экспериментальным данным твёрдость баббита, равная 18 - 20 НВ при температуре до 90 0С, с повышением температуры выше 100 0С уменьшается до 11-13 НВ - до границы работоспособности. Соответственно зависят от температуры предел текучести и усталостная прочность сплава.
Было установлено, что содержание кальция в баббитовой заливке, меньшее 0,15%, в случае выхода вкладыша из строя даёт основание для рекламационных претензий изготовителю. Учитывая предстоящую многолетнюю эксплуатацию тепловозов этого типа, вполне обосновано предложение о лабораторной и эксплуатационной на партии тепловозов проверке вкладышей с повышенным до 0,25% - 0,35% содержанием кальция в баббите антифрикционного слоя. При этом содержание в сплаве натрия должно оставаться в ранее установленном диапазоне 0,20 - 0,40 %, что исключает старение сплава.
Исследования условий смазки подшипников в предпусковой и пусковой период выявили необходимость увеличения времени предпусковой прокачки дизеля маслом, что было реализовано изменением установки реле времени (не менее 40 с). При предпусковой прокачке дизеля маслопрокачивающим насосом отсутствие клапана на линии отвода масла к центробежному фильтру приводило к бесполезному сливу 30 -40% масла через фильтр. Установка перед центрифугой клапана, закрывающего проход масла к центрифуге в период работы маслопрокачивающего насоса перед запуском дизеля и открывающегося под давлением, превышающим 0,2 МПа, позволила использовать для предпусковой смазки подшипников дизеля производительность маслопрокачивающего насоса полностью.
Выводы. При анализе причин дефектов подшипников было обращено внимание на завышенное значение допускаемой величины дисбаланса коленчатого вала, равное 15 кг см. Технология статической балансировки не обеспечивала контроля дисбаланса по длине вала. Следствием являлась дополнительная нагрузка на коренные подшипники в зоне повышенного дисбаланса. Рекомендация о снижении допуска вдвое была реализована введением динамической балансировки коленчатых валов. Допуск на дисбаланс, измеряемый в трёх поперечных плоскостях, был уменьшен до 6 кгсм. При этом требования к ограничению разновеса комплектов шатун - поршень, устанавливаемых на дизель, не были снижены.
Библиографический список
1. ПУШКАРЕВ И. Ф., ПАХОМОВ Э. А. Контроль и оценка технического состояния тепловозов. — М.: Транспорт, 1985, 120с.