Состав, принятый для стекла каждой марки, обеспечивает получение установленных ГОСТ 3514-94 оптических констант при соблюдении некоторых средних условий производства. При любом отступлении от них оптические постоянные отклоняются от номинальных значений. Это определяет чрезвычайно жесткие требования к точности и качеству приготовления шихты.
В методических указаниях к лабораторным работам и курсовому проектированию «Химический состав оптических стекол» (сноска) приведены составы всех марок, применяющихся в оптической промышленности стекол.
Бесцветное оптическое стекло. Настоящий отраслевой стандарт ОСТ 3-4931-81 распространяется на бесцветное оптическое стекло серии 100. Синтетический состав установлен применительно к технологическому процессу изготовления стекол, утвержденному на производстве.
Цветное стекло. Отраслевой стандарт 3-4375-79 распространяется на оптическое цветное стекло, и устанавливает химический синтетический состав. Синтетический состав установлен применительно к технологическому процессу изготовления стекол, утвержденному в установленном порядке.
2. Выбор сырьевых материаловВыбор сырьевых материалов производится по нормативным документам: ГОСТам, ОСТам и ТУ. При этом учитываются:
- содержание примесных компонентов и, в первую очередь, оксидов железа, придающих стеклу цветной оттенок;
- влияние сырьевых материалов на скорость процесса стекловарения;
- необходимость поддержания определенных условий варки (окислительных, восстановительных) или ускорения стекловарения;
- стоимость сырьевых материалов;
- дальность перевозки от баз до проектируемого завода или цеха, в первую очередь, для основных компонентов шихты (кварцевый песок, сода, известняк, свинцовый сурик, поташ).
Химический состав сырьевых материалов для расчета шихты стекла приведен в методических указаниях «Сырьевые материалы для производства оптических стекол». (сноска)
Выбор сырья следует начинать с кварцевого песка. В ГОСТе 22551-77 изложены требования к химическому составу кварцевых песков в зависимости от вида и качества изделия из стекла. Для установленного ранее ассортимента подбирают необходимую марку кварцевого песка с указанием по химическому составу. Содержание примесных оксидов, которые не лимитируются ГОСТом (CaO, MgO, Na2O, K2O), может приниматься с учетом химических характеристик кварцевых песков различных месторождений.
Можно принять, что содержание Fe2O3 в готовой продукции из стекла не должно превышать максимально допустимое значение Fe2O3 в кварцевом песке, идущем на производство этой продукции, т.е. руководствоваться ГОСТ 22551-77, поскольку содержание Fe2O3 в готовой продукции нормативными документами не лимитируется. Исходя из принятого условия, вслед за песком выбирают другие природные и технические сырьевые материалы, учитывая содержание в них оксидов железа и приближенно оценивая возможные их качества в шихте, а также максимально возможное содержание Fe2O3 в готовом стекле.
Во избежание использования случайных анализов, химический состав природных и технических сырьевых материалов принимается по данным нормативных документов. При этом берутся минимально возможные содержания основного вещества и максимально возможные содержания примесей. Это позволит, во-первых, без дефицита рассчитать в дальнейшем потребность в сырьевых материалах и, во-вторых, прогнозировать наиболее неблагоприятный случай.
Сумма компонентов в составе сырьевых материалов всегда меньше100%, т.к. не учитывает потери при прокаливании, некоторые летучие вещества и многие малые примеси.
Влияние сырьевых материалов на интенсивность и условия варки учитывается на основе теоретических представлений о стекловарении и практики стекольного производства. По-разному влияют на интенсивность варки щелочесодержащие материалы (сода, сульфат натрия), материалы, содержащие Al2O3 (полевошпатовые и кварц-полевошпатовые концентраты, технический глинозем, глины, каолины). Окислительные условия варки многих стекол (хрустали, ряд цветных и других стекол) требуют введения селитр или других окислителей. Для поддержания восстановительных условий варки (ряд цветных и других стекол) применяют восстановители, что может не найти отражения в заданном химическом составе стекла. Необходимость введения ускорителей варки устанавливается на основе критического рассмотрения заданного состава стекла, выбранных сырьевых материалов, достигнутого удельного съема стекломассы и температурных условий варки.
Марки и сорта сырьевых материалов выбирают с учетом их оптовых цен: сырьевые материалы должны удовлетворять изложенным выше требованиям и быть по возможности дешевыми. Из тех же соображений выбирают месторождение или предприятие-изготовитель: дальность перевозки сырья должна быть минимальной. Некоторые компании-изготовители и месторождения приведены в табл. 2.1.
Работа по данному разделу заканчивается сводкой выбранных сырьевых материалов в таблице по форме, приведенной ниже (табл. 2.2).
Таблица 2.1
Месторождения и предприятия-изготовители сырьевых материалов
Компания, город |
Сырьевые материалы |
Кыштымский ГОК, г. Кыштым |
Жильный кварц |
Волга-Хим, г. Волгоград |
Двуокись церия |
Волга-Хим, г. Волгоград |
Поташ |
НеваРеактив, г. Санкт-Петербург |
Окись сурьмы |
НеваРеактив, г. Санкт-Петербург |
Глет |
ЗАО Химсервис, г. Уфа |
Борная кислота |
ЗАО Химсервис, г. Уфа |
Цинка окись |
ЗАО Химсервис, г. Уфа |
Кальций углекислый |
ЗАО Химсервис, г. Уфа |
Сода |
ООО «НФП Невский химик», г. Санкт-Петербург |
Фосфорная кислота |
ООО «ЧеляБхимСнаб», г. Челябинск |
Алюминия (III) окись (глинозем) |
ООО «Таурус Плюс», г. Санкт-Петербург |
Меди окись порошкообразная |
ООО «ПромСнабКомплект», г. Первоуральск |
Ванадия окись |
Таблица 2.2
Данный состав |
Наимено-вание сырьевого материала |
Химическая формула материала |
Массовая доля основного вещества |
Массовая доля примесей, * 10-5 |
Номер нормативного документа |
Марка материала |
|||
Fe2O3 |
MnO |
CuO |
Fe2O3 |
||||||
P2O3 |
Фосфорная кислота |
H3PO4 |
95 % |
5 |
0,5 |
0,5 |
0,5 |
ТУ 6-09-5204 |
Особо чистый 16 - 4 |
И т. д. |
Приготовление шихты выполняют на традиционном оборудовании. Трудности процесса связаны с разнообразием составов стекол, малым объемом шихты для мелких партий изделий и огромной номенклатурой используемых материалов. Как правило, каждый материал имеет несколько кондиций (марок) по качеству: технический, чистый, чистый для анализа, химически чистый, особо чистый для производства оптического стекла. Для получения оптического стекла используются кварцевые пески лучших месторождений с содержанием оксида кремния примерно 99% и оксида железа не больше 0,4%.
Выбор сырьевого материала определяется, с одной стороны, его стоимостью, с другой – требованиями к данному стеклу.
Состав, принятый для стекла каждой марки, обеспечивает получение установленных ГОСТ 3514-94 оптических констант при соблюдении некоторых средних условий производства. При любом отступлении от них оптические постоянные отклоняются от номинальных значений. Это определяет чрезвычайно жесткие требования к точности и качеству приготовления шихты.
3.1. Общие формулы для пересчета состава стекла и их примечаниеСостав стекол обычно принято выражать в массовых и молярных процентах. Выражение состава стекол в массовых процентах является наиболее распространенным и удобным для заводской практики. Содержание отдельных оксидов в стекле определяется по формуле (3.1)
,
(3.1)
где Рi – содержание i-ого оксида в стекле, масс.%;
pi – массовое содержание i-ого оксида в стекле, масс. ч.;
∑pi – суммарное массовое содержание всех оксидов в стекле, масс. ч.
Состав стекла в молярных процентах выражают, как правило, в научных исследованиях, при расчетах свойств стекла по методу Аппена. Содержание отдельных оксидов в стекле в этом случае определяют по формуле (3.2):
,
(3.2)
где Ni – содержание i-ого оксида, мол. %;
ni – число молей i-ого оксида;
∑ ni – сумма молей всех оксидов стекла.
3.1.1. Приведение химического состава к стопроцентному
Состав сырьевых материалов и стекла (химический состав) в большинстве случаев в сумме не составляет точно 100 %. Расчеты с химическим составом сырьевых материалов или стекол, не приведенных к 100 %, более затруднительны и кропотливы, чем с составом, приведенным к 100 %.
Для приведения состава к стопроцентному используется формула (3.3):
,
(3.3)
где Рi – содержание компонента (оксида) по анализу, мас. %;
∑Рi – суммарное содержание компонентов (оксидов) по анализу, масс. %.
3.1.2. Пересчет состава сырьевых материалов на безугарный
При пересчете состава сырьевых материалов на безугарный из состава исключают выгорающие во время варки стекла соединения, например, CO2, SO3, H2O и др.
Основные вещества сырьевых материалов, представляющие сложные соединения (Na2CO3, KNO3, H3BO3, Na2B4O7·10H2O, Ba(NO3)2 и др.), пересчитываются на оксиды в соответствии со стехиометрией химических реакций. Вода и газы, которые удаляются в процессе варки, не включаются в состав сырьевых материалов. Сложные оксиды (PbO2, Pb3O4), а также металлы (Al, Na, Pb) и катиона (Fe2+, Zn2+) пересчитываются на оксиды, которые образуются в стекле при варке.
Пример 1
Согласно ГОСТ 828-77 натрий азотнокислый технический (селитра натриевая) 1 сорта имеет химический состав (масс. %): NaNO3 – 99,5; NaCl – 0,5.
В процессе варки из двух молекул NaNO3 в стекле образуется одна молекула Na2O
2NaNO3 = Na2O + N2 + 2,5O2
2 · (22,99 + 14,01 + 15,999 · 3) = 166,994 мас. ч. NaNO3 дают (22,992 · 2 + 15,999) = 61,979 мас. ч. Na2O, а 99,5 мас. % NaNO3 дают Х мас. % Na2O.
Отсюда содержание Na2O в селитре натриевой равно
Х = 99,5 · (61,979 / 166,994) = 36,93 мас. %
Кроме того, в результате улетучивания и разложения NaCl парами воды при варке переходит в стекло оксид Na2O, количество которого в 10 раз меньше по массе исходного количества NaCl.
Следовательно, 0,5 мас. % NaCl дают 0,05 мас. % Na2O. Тогда суммарное содержание Na2O в составе натрия азотнокислого технического, которое переходит в состав стекла, составляет
36,93 + 0,05 = 36,98 мас. %
Следовательно, химический состав натрия азотнокислого технического, пригодный для расчета шихты, выражается в виде оксида
Na2O = 36,98 %.
Пример 2
По ГОСТ 6318-77 сульфат натрия технический имеет следующий химический состав (мас. %): Na2SO4 – 97,4; CaSO4 – 0,15; Fe3+ - 0,01; Zn2+ - 0,90.
В соответствии с химической реакцией
Na2SO4 = Na2O + SO2
+ 0,5O2
(22,99 · 2 + 32,06 + 15,999 · 4) = 142,036 мас. ч. Na2SO4 дают (22,99 · 2 + 15,999) = 61,979 мас. ч. Na2O, а 97,4 мас. % дают Х масс. % Na2O, тогда
Х = 97,4 · (61,979 / 142,036) = 42,50 мас. % Na2O
Согласно химической реакции
CaSO4
= CaO + SO2 + 0,5O2
(40,08 + 32,06 + 15,999 · 4) = 136,136 мас. ч. CaSO4 дают 40,08 + 15,999 = 56,079 мас. ч. CaO, а 0,15 мас. % CaSO4 дают Y масс. % CaO, отсюда
Y = 0,15 * (56,079 / 136,136) = 0,06 мас. % CaO
Исходя из химической реакции
2Fe3+ + 1,5O2 = Fe2O3
55,84 · 2 = 111, 68 мас. ч. Fe3+ дают (55,84 2 + 15,999 · 3) = 159,677 мас. ч. Fe2O3, а 0,01 мас. % Fe3+ дает Z масс. % Fe2O3.
Z = 0,01 (159,677 / 111,68) = 0,014 мас. % Fe2O3
По химической реакции
Zn2+ + 0,5 О2 = ZnO
65,38 мас. ч. Zn2+ дают 65, 38 + 15,999 = 81,999 мас. ч. ZnO, а 0,90 мас. % Zn2+ дают U мас. % ZnO. Следовательно,
U = 0,90 · (81,379 / 65,38) = 1,12 мас. % ZnO.
После указанных пересчетов химический состав сульфата натрия технического, подготовленный для расчета шихты, выглядит следующим образом (масс. %): Na2O – 42,59; CaO – 0,06; Fe2O3 – 0,014; ZnO – 1,12.
Сумма компонентов в химическом составе сырьевых материалов по данным нормативных документов всегда ниже 100 мас. %, т. к. не учитывает потери при прокаливании, летучие вещества и многие малые примеси. После рассмотренных выше пересчетов в большинстве случаев сумма компонентов становится еще меньше.
3.2. Расчет состава шихты по заданному составу стекла
При расчете стекольной шихты принимают, что в стекло переходят оксиды и фториды, а влага и газы улетучиваются. Расчеты шихты можно проводить на 100 массовых частей стекла или на 100 массовых частей кварцевого песка. Более распространен первый способ, т. к. он облегчает дальнейшие вычисления.
Исходными данными для расчета состава шихты служат:
1) Заданный химический состав стекла, масс. %;
2) Химические составы выбранных сырьевых материалов, мас. %;
3) Поправочные коэффициенты на улетучивание компонентов стекла при варке.
Заданный химический состав стекла должен быть приведен к 100 мас. %. В него не должны включаться компоненты, попадающие в стекло как нежелательные примеси в сырьевых материалах (Fe2O3, Al2O3 и др.), или компоненты, попадающие из атмосферы печи (SO3).
Химические составы сырьевых материалов принимаются по данным нормативных документов: ГОСТ, ОСТ или ТУ. Химический состав каждого сырьевого материала должен быть представлен в виде оксидов или фторидов, переходящих в стекло. Поэтому данные нормативных документов при необходимости должны быть предварительно обработаны. (см. п. 1.4).
3.2.1. Расчет шихты из качественных сырьевых материалов
К качественным сырьевым материалам могут быть отнесены высшие сорта кварцевого песка, доломита, известняка, а также большинство технических сырьевых материалов. За редким исключением (доломит, борат кальция) они предназначены для введения в стекло какого-либо одного заданного оксида, содержание которого в них является высоким, а остальные примесные оксиды содержатся в незначительных количествах. Доломит и борат кальция предназначены для введения в стекла соответственно оксидов магния и бора, но одновременно с ними вводятся примерно такие же по массе количества оксида кальция. Если кварцевый песок содержит существенное количество примесного оксида алюминия, то он может рассчитываться как материал, с которым вводятся два заданных оксида кремния и алюминия. Шихты из качественных сырьевых материалов применяют в производстве оптических и хрустальных стекол, сортового стекла, художественных изделий, многих технических стекол, при лабораторных исследованиях по синтезу стекол.
Некоторые компоненты стекла заметно или сильно улетучиваются в процессе варки. Для компенсации потерь на улетучивание и обеспечения получения стекла заданного состава сырьевые материалы, содержащие такие компоненты, вводят в шихту в повышенных количествах. При расчетах шихты в таких случаях используют поправочные коэффициенты на улетучивание компонентов стекла (табл. 3.1). Расчет шихты на 100 мас. ч. стекла производится по выражению (3.4):
,
(3.4)
где Мi – количество сырьевого материала в шихте, масс. ч.;
Ai – заданное содержание оксида в стекле, масс. %;
Ki – поправочный коэффициент на улетучивание оксида при варке;
Pi – содержание заданного оксида в сырьевом материале, масс. %.
Таблица 3.1
Поправочные коэффициенты на улетучивание компонентов
Компоненты стекла |
Поправочный коэффициент |
Примечание |
Na2O |
1,032 |
При введении через соду (Na2CO3) |
Na2O |
1,06 |
При введении через сульфат (Na2SO4) |
K2O |
1,12 |
- |
ZnO |
1,04 |
- |
PbO |
1,14 |
- |
P2O5 |
1,075 |
Листовое стекло |
B2O3 |
1,11 |
При содержании в стекле до 7% |
B2O3 |
1,15 |
При содержании в стекле более 7% |
Na2SiF6 |
1,30 |
- |
2NaF · AlF3 |
1,30 |
|
F |
1,30 |
С другими компонентами для обычных стекол |
F |
1,50 |
С другими компонентами для тугоплавких стекол |
Se |
1,90 |
- |
Остальные |
1,00 |
- |
При введении одного заданного оксида с двумя различными сырьевыми материалами (например, K2O вводится в свинцовый хрусталь поташом и селитрой) заранее устанавливаю, какое количество оксида вводится с каждым из двух сырьевых материалов.
Количество доломита, бората кальция и кварцевого песка определяют, исходя из заданного содержания в стекле тех оксидов, для введения которых они предназначены, т. е. MgO, B2O3, и SiO2. После этого вычисляют, сколько вводится с этими материалами соответственно оксидов CaO и Al2O3, присутствующих в указанных выше сырьевых материалах в виде примесей. По разности между заданным содержанием оксидов в стекле и вводимым с указанными сырьевыми материалами устанавливают новое заданное содержание CaO и Al2O3, по уравнению (3.5):
,
(3.5)
Исходя из нового заданного содержания Ai определяют количества сырьевых материалов (известняка, технического глинозема), необходимые для введения оставшейся части оксидов кальция или алюминия.
Дальнейшие расчеты выполняются в следующей последовательности. По рассчитанным количествам каждого сырьевого материала в шихте Mi определяют количества всех оксидов, включая примесные, переходящие в стекло с каждым сырьевым материалом. Вычисления выполняют по формуле (3.6):
,
(3.6)
где Pij – количества оксидов, переходящих в стекло из каждого сырьевого материала последовательно, масс.%;
αij – содержание оксидов последовательно в каждом сырьевом материале, масс. %;
Ki – поправочные коэффициенты на улетучивание оксидов.
Затем составляют сводную таблицу и суммируют вычисленные значения по каждому заданному и примесному оксиду. При этом получают так называемый расчетный химический состав, в котором сумма компонентов ∑Pij = ∑Aрасч. i > 100 мас. ч за счет вхождения в стекло примесных оксидов из сырьевых материалов.
Затем пересчитывают расчетный химический состав стекла на 100 мас. % и получают так называемый теоретический состав. Для пересчета используют выражение (3.7):
Aтеор. i = Aрасч. i · (100 / ∑расч.), (3.7)
где Aтеор. i – содержание заданных и примесных оксидов в теоретическом составе стекла, масс. %;
Aрасч. i – суммарное количество компонентов в расчетном составе стекла, мас. ч.;
∑расч – суммарное количество компонентов в расчетном составе стекла, масс. ч.
В теоретическом составе стекла, полученном из рассчитанной шихты, сумма всех оксидов ∑теор. = ∑Aтеор. i = 100 мас. %.
Поскольку расчет шихты проводится на 100 мас. ч. стекла, в заключение выполняют корректировку количеств сырьевых материалов в шихте по формуле (3.8):
МОi = (Мi · 100) / ∑расч., (3.8)
где МОi – откорректированные количества сырьевых материалов шихты, масс. ч. на 100 мас. ч. стекла;
Мi – ранее определенные по выражению (3.4) количества сырьевых материалов, мас. ч.
Итогом расчета шихты должно быть выражение (3.9)
Q = MO1 + MO2 + … + MOn, (3.9)
где Q – суммарное количество всех сырьевых материалов, масс. ч. на 100 мас. ч. стекла.
Состав шихты по выражению (2.7) необходимо знать для синтеза стекол, а также для расчета производственной программы составного цеха (участка).
По результатам расчета шихты определяются важные с технологической точки зрения показатели: выход стекла при стеклообразовании и угар шихты. Выход стекла при стеклообразовании В определяется из пропорции:
Q масс. ч. шихты дают 100 мас. ч. стекла
100 мас. ч. шихты дают B мас. ч. стекла, тогда выход стекла можно вычислить по формуле (3.10):
B = (104 / Q) % (3.10)
Угар шихты У вычисляют по выражению (3.11):
У = (100 – B) % (3.11)
Пример 1. Расчет стекольной шихты
Заданный химический состав стекла, мас. %:
SiO2 – 62,0; Al2O3– 0,9; PbO – 19,5; K2O – 14,6; Na2O – 3,0. ∑Pi = 100.
8,0 мас. % K2O вводится через поташ; 6,6 мас. % K2O – через селитру.
Химический состав выбранных сырьевых материалов после необходимых предварительных пересчетов сведен в табл. 3.2.
Таблица 3.2
Химический состав сырьевых материалов, мас. %
Сырьевые материалы |
Заданные оксиды |
Примесные оксиды |
||||
SiO2 |
Al2O3 |
PbO |
K2O |
Na2O |
Fe2O3 |
|
Кварцевый песок |
98,5 |
0,6 |
- |
- |
0,3 |
0,03 |
Технический глинозем |
- |
98,9 |
- |
- |
0,4 |
0,03 |
Свинцовый сурик |
- |
- |
97,0 |
- |
- |
0,003 |
Поташ |
- |
- |
- |
66,8 |
0,3 |
0,001 |
Селитра калиевая |
- |
- |
- |
46,5 |
- |
0,005 |
Сода техническая |
- |
- |
- |
- |
57,6 |
0,005 |
Поправочные коэффициенты на улетучивание оксидов:
SiO2 |
Al2O3 |
PbO |
K2O |
Na2O |
Fe2O3 |
1,00 |
1,00 |
1,14 |
1,12 |
1,032 |
1,00 |
Вначале последовательно определяем количества каждого сырьевого материала в шихте по выражению (3.4).
Количество кварцевого песка в шихте
M1 = (62,0 · 1,0 · 100) / 98,5 = 62,94 мас. ч
С вычисленным количеством кварцевого песка в стекло вводится
Аввед = 62,94 · (0,6 / 100) = 0,38 мас. % Al2O3
Следовательно, с помощью технического глинозема в стекло надо ввести Al2O3
А’ = 0,90 – 0,38 = 0,52 мас. % Al2O3
Тогда количество технического глинозема в шихте
M2 = (0,52 · 1,0 · 100) / 98,9 = 0,53 мас. ч
Количество свинцового сурика в шихте
M3 = (19,5 · 1,14 · 100) / 97,0 = 22,92 мас. ч
Количество поташа в шихте
M4 = (8,0 · 1,12 · 100) / 66,8 = 13,41 мас. ч
Количество селитры калиевой в шихте
M5 = (6,6 · 1,12 · 100) / 46,5 = 15,90 мас. ч
С вычисленным количеством кварцевого песка в стекло вводится
Аввед = 62,94 · (0,3 / 100) = 0,19 мас. % Na2O
Следовательно, с помощью соды технической в стекло надо ввести
А’ = 3,0 – 0,19 = 2,81 мас. % Na2O
Количество соды технической в шихте
M6 = (2,81 · 1,032 · 100) / 57,6 = 5,03 мас. ч
Далее определяем количество оксидов, переходящих в стекло с каждым сырьевым материалом.
С кварцевым песком в стекло переходит:
Р SiO2 = (62,94 · 98,5) / (1,0 · 100) = 62,00 мас. %
Р Al2O3 = (62,94 · 0,6) / (1,0 · 100) = 0,38 мас. %
Р Na2O = (62,94 · 0,3) / (1,032 · 100) = 0,19 мас. %
Р Fe2O3 = (62,94 · 0,03) / (1,0 · 100) = 0,019 мас. %
С техническим глиноземом в стекло переходит:
Р Al2O3 = (0,53 · 98,9) / (1,0 · 100) = 0,52 мас. %
Р Na2O = (0,53 · 0,4) / (1,032 · 100) = 0,002 мас. %
Р Fe2O3 = (0,53 · 0,003) / (1,0 · 100) = 0,0002 мас. %
Со свинцовым суриком в стекло переходит:
Р PbO = (22,92 · 97,0) / (1,14 · 100) = 19,50 мас. %
Р Fe2O3 = (22,92 · 0,003) / (1,0 · 100) = 0,0007 мас. %
С поташом в стекло переходит:
Р K2O = (15,90 · 46,5) / (1,12 · 100) = 6,60 мас. %
Р Fe2O3 = (15,90 · 0,005) / (1,0 · 100) = 0,0008 мас. %
С содой технической в стекло переходят:
Р Na2O = (5,03 · 57,6) / (1,032 · 100) = 2,81 мас. %
Р Fe2O3 = (5,03 · 0,005) / (1,0 · 100) = 0,0002 мас. %
Далее составляем сводную таблицу и определяем расчетный состав стекла (табл.3.3).
Таблица 3.3
Расчетный состав стекла
№ п/п |
Сырьевые материалы |
Переходят в стекло, мас. % |
|||||
SiO2 |
Al2O3 |
PbO |
K2O |
Na2O |
Fe2O3 |
||
1 |
Кварцевый песок |
62,0 |
0,38 |
- |
- |
0,19 |
0,19 |
2 |
Технический глинозем |
- |
0,52 |
- |
- |
0,002 |
0,0002 |
3 |
Свинцовый сурик |
- |
- |
19,50 |
- |
- |
0,0007 |
4 |
Поташ |
- |
- |
- |
8,0 |
0,04 |
0,001 |
5 |
Селитра калиевая |
- |
- |
- |
6,6 |
- |
0,008 |
6 |
Сода техническая |
- |
- |
- |
- |
2,81 |
0,0003 |
Расчетный состав |
62,0 |
0,90 |
19,50 |
14,6 |
3,042 |
0,029 |
|
∑расч = 100,063 |
Сумма компонентов в расчетном химическом составе стекле оказалась выше 100 за счет вхождения в стекло оксида натрия из технического глинозема и поташа и примесей оксида железа из всех сырьевых материалов. Теоретический состав стекла получаем путем пересчета расчетного состава по выражению (2.5) и сравниваем между собой заданный, расчетный и теоретические составы.
Заданный |
Расчетный |
Теоретический |
|
SiO2 |
62,0 |
62,0 |
61,95 |
Al2O3 |
0,9 |
0,9 |
0,9 |
PbO |
19,5 |
19,5 |
19,45 |
K2O |
14,6 |
14,6 |
14,57 |
Na2O |
3,0 |
3,042 |
3,21 |
Fe2O3 |
- |
0,029 |
0,2 |
∑ |
100,0 |
100,063 |
100,0 |
Анализ химических составов стекол, их сравнение и оценка правильности выбранных сырьевых материалов рассматриваются в разделе 2.4.
Считая теоретический состав стекла, получаемого из выбранных сырьевых материалов, приемлемым, проводим корректировку состава шихты по выражению (2.6):
МО1 = (62,94 · 100) / 100,063 = 62,90 мас. ч.
МО2 = (0,53 · 100) / 100,063 = 0,53 мас. ч.
МО3 = (22,92 · 100) / 100,063 = 22,90 мас. ч.
МО4 = (13,41 · 100) / 100,063 = 13,40 мас. ч.
МО5 = (15,90 · 100) / 100,063 = 15,89 мас. ч.
МО6 = (5,37 · 100) / 100,063 = 5,36 мас. ч.
Q = ∑ МОi = 120,98 мас. ч. на 100 мас. ч. стекла.
Таким образом, состав шихты, мас. ч. на 100 мас. ч. стекла, будет следующим:
Кварцевый песок 62,90
Технический глинозем 0,53
Свинцовый сурик 22,90
Поташ 13,40
Селитра калиевая 15,89
Сода техническая 5,36
Итого: 120,98
По выражению (2.8) определяем выход стекла при стеклообразовании
В = (104) / 120,98 = 82,6 %
Угар шихты по формуле (2.9) составляет:
У = 100 – 82,6 = 17,4 %
3.2.2. Пример 2. Расчет стекольной шихты
Заданный химический состав стекла, мас. %: P2O5 – 61,86; Al2O3 – 6,54; K2O – 9,91; ZnO – 20,82; CuO – 0,50; V2O5 – 0,37.∑Pi = 100.
Химический состав выбранных сырьевых материалов после необходимых предварительных пересчетов сведен в табл. 2.
Таблица 2
Химический состав сырьевых материалов, мас. %
Сырьевые материалы |
Заданные оксиды |
Примесные оксиды |
|||||||||
P2O5 |
Al2O3 |
ZnO |
K2O |
CuO |
V2O5 |
Fe2O3 |
MnO |
Cr2O3 |
NiO |
CoO |
|
H3PO4 |
68,8 |
0,000005 |
0,00005 |
0,000005 |
0,000005 |
0,000005 |
0,000003 |
||||
Al2O3 |
98 |
0,03 |
|||||||||
ZnO |
99,7 |
||||||||||
K2CO3 |
67,48 |
0,00005 |
0,0003 |
0,0001 |
0,00005 |
0,00005 |
0,000005 |
||||
CuO |
99,9 |
0,02 |
|||||||||
V2O5 |
97 |
Поправочные коэффициенты на улетучивание оксидов:
P2O5 |
Al2O3 |
ZnO |
K2O |
CuO |
V2O5 |
Fe2O3 |
MnO |
Cr2O3 |
NiO |
CoO |
1,075 |
1,00 |
1,04 |
1,12 |
1,00 |
1,00 |
1,00 |
1,00 |
1,00 |
1,00 |
1,00 |
Последовательно определяем количества каждого сырьевого материала в шихте по выражению (1).
Количество цинковой окиси ZnO в шихте:
MZnO = 20,82 · 1,04 · 100 / 99,7 = 21,72 мас. ч.
Количество окиси ванадия V2O5 в шихте:
МV2O5 = 0,37 · 1 · 100 / 97 = 0,38 мас. ч.
Количество фосфорной кислоты H3PO4 в шихте:
МH3PO4 = 61,86 · 1,075 · 100 / 68,8 = 96,66 мас. ч.
С вычисленным количеством фосфорной кислоты в стекло вводится:
Аввед = 122,44 · 0,000005 / 100 = 0,000006 мас. % CuO
Количество глинозема Al2O3 в шихте:
МAl2O3 = 6,54 · 1 · 100 / 98 = 6,68 мас. ч.
Количество поташа K2CO3 в шихте:
МK2CO3 = 9,91 · 1,12 · 100 / 67,48 = 16,45 мас. ч.
С вычисленным количеством поташа в стекло вводится:
Аввед = 16,43 · 0,00005 / 16,43 = 0,00005 мас. % CuO
Следовательно, с помощью окиси меди в стекло надо ввести CuO
А’введ = 0,5 – Аввед = 0,5 – 0,00005 - 0,000006 = 0,499944 мас. % CuO
Тогда количество окиси меди CuO в шихте:
МCuO = А’введ · 1 · 100 / 99,9 = 0,499944 · 1 · 100 / 99,9 = 0,5 мас. ч.
Определяем количество оксидов, переходящих в стекло с каждым сырьевым материалом.
С фосфорной кислотой в стекло переходит:
РP2O5 = (96,66 · 68,8) / (1,075 · 100) = 61,86 мас. %
Р Fe2O3 = (96,66 · 0,00005) / (1 · 100) = 0,00005 мас. %
РMnO = (96,66 · 0,000005) / (1 · 100) = 0,000005 мас. %
РCuO = (96,66 · 0,000005) / (1 · 100) = 0,000005 мас. %
РCr2O3 = (96,66 · 0,000005) / (1 · 100) = 0,000005 мас. %
РNiO = (96,66· 0,000005) / (1 · 100) = 0,000005 мас. %
РCoO = (96,66 · 0,000003) / (1 · 100) = 0,000003 мас. %
С глиноземом в стекло переходит:
РAl2O3 = (6,68 · 98) / (1 · 100) = 6,55 мас. %
РFe2O3 = (6,68 · 0,03) / (1 · 100) = 0,002 мас. %
С окисью цинка в стекло переходит:
РZnO = (21,72 · 99,7) / (1,04 · 100) = 20,82 мас. %
С поташом в стекло переходит:
РK2O = (16,45 · 67,48) / (1,12 · 100) = 9,91 мас. %
РFe2O3 = (16,45 · 0,0003) / (1 · 100) = 0,000049 мас. %
РMnO = (16,45 · 0,0001) / (1 · 100) = 0,000016 мас. %
РCuO = (16,45 · 0,00005) / (1 · 100) = 0,0000082 мас. %
РCr2O3 = (16,45 · 0,00005) / (1 · 100) = 0,0000082 мас. %
РNiO = (16,45 · 0,00005) / (1 · 100) = 0,0000082 мас. %
РCoO = (16,45 · 0,000005) / (1 · 100) = 0,00000082 мас. %
С окисью меди в стекло переходит:
РCuO = (0,5 · 99,9) / (1 · 100) = 0,5 мас. %
РFe2O3 = (0,5 · 0,02) / (1 · 100) = 0,0001 мас. %
С окисью ванадия в стекло переходит:
РV2O5 = (0,38 · 97) / (1 · 100) = 0,37 мас. %
Далее составляем сводную таблицу и определяем расчетный состав стекла.
Таблица Расчетный состав стекла |
CoO |
0,000003 |
0,00000082 |
0,00000382 |
∑ = 100,0122644 |
||||
NiO |
0,000005 |
0,0000082 |
0,0000132 |
||||||
Cr2O3 |
0,000005 |
0,0000082 |
0,0000132 |
||||||
MnO |
0,000005 |
0,000016 |
0,000021 |
||||||
Fe2O3 |
0,00005 |
0,002 |
0,000049 |
0,0001 |
0,0022 |
||||
V2O5 |
0,37 |
0,37 |
|||||||
CuO |
0,000005 |
0,0000082 |
0,5 |
0,5000132 |
|||||
K2O |
9,91 |
9,91 |
|||||||
ZnO |
20,82 |
20,82 |
|||||||
Al2O3 |
6,55 |
6,55 |
|||||||
P2O5 |
61,86 |
61,86 |
|||||||
Сырьевые материалы |
Фосфорная кислота |
Глинозем |
Цинковые белила |
Поташ |
Меди окись |
Ванадия окись |
Расчетный состав |
Сумма компонентов в расчетном химическом составе стекле оказалась выше 100 за счет вхождения в стекло оксида натрия из технического глинозема и поташа и примесей оксида железа из всех сырьевых материалов. Теоретический состав стекла получаем путем пересчета расчетного состава по выражению (2.5) и сравниваем между собой заданный, расчетный и теоретические составы.
Таблица 14
Заданный |
Расчетный |
Теоретический |
|
P2O5 |
61,86 |
61,86 |
61,8524 |
Al2O3 |
6,54 |
6,55 |
6,5492 |
ZnO |
20,82 |
20,82 |
20,8174 |
K2O |
9,91 |
9,91 |
9,9088 |
CuO |
0,5 |
0,5000132 |
0,5 |
V2O5 |
0,37 |
0,37 |
0,37 |
Fe2O3 |
0,0022 |
0,0022 |
|
MnO |
0,000021 |
0,000021 |
|
Cr2O3 |
0,0000132 |
0,0000132 |
|
NiO |
0,0000132 |
0,0000132 |
|
CoO |
0,00000382 |
0,00000382 |
|
∑ |
100,0 |
100,0122644 |
100,0 |
Анализ химических составов стекол, их сравнение и оценка правильности выбранных сырьевых материалов рассматриваются в разделе 2.4.
Считая теоретический состав стекла, получаемого из выбранных сырьевых материалов, приемлемым, проводим корректировку состава шихты по выражению (2.6):
МОH3PO4= 96,66 · 100 / 100,012 = 96,65 мас. ч.
МОAl2O3 = 6,67 · 100 / 100,012 = 6,68 мас. ч.
MОZnO = 21,72 · 100 / 100,012 = 21,72 мас. ч.
МОK2CO3 = 16,45 · 100 / 100,012 = 16,45 мас. ч.
МОCuO = 0,5 · 100 / 100,012 = 0,5 мас. ч.
МОV2O5 = 0,38 · 100 / 100,012 = 0,38 мас. ч.
Q = 96,66 + 6,68 + 21,72 + 16,45 + 0,5 + 0,38 = 142,38 мас. ч. стекла
Таким образом, состав шихты, мас. ч. на 100 мас. ч. стекла будет слудеющим:
Фосфорная кислота |
96,65 |
Глинозем |
6,68 |
Цинковые белила |
21,72 |
Поташ |
16,45 |
Окись меди |
0,5 |
Окись ванадия |
0,38 |
∑ |
142,38 |
Определяем выход стекла при стеклообразовании
В = (104 / 142,38) = 70,23 %
Угар шихты считаем по формуле (2.9) составляет:
У = 100 – 70,23 = 29,77 %
4. Расчет производственной программыРасчет производной программы включает:
- вычисление фактического количества стеклянных изделий, заготовок, полуфабрикатов с учетом отходов, боя и брака, находящихся на каждой стадии технологического процесса;
- вычисление потребного количества стекломассы, шихты и сырьевых материалов;
- вычисление объемов переработки, транспортирования и хранения сырьевых материалов согласно технологической схеме составного цеха;
Стекловаренные сосуды выбираются с учетом особенности варки конкретной марки стекла.
Исходные данные для расчета производственной программы составного цеха:
1) Плотность оптического стекла данной марки, ρ, г/см3;
2) Тип горшков и объём, V, л;
3) Общее количество горшков, n, шт.;
4) Коэффициент заполняемости горшка, К;
5) Количество возвратного стеклобоя, δ, %.
Расчёт номинального годового фонда рабочего времени ТН:
Количество рабочих дней (суток) в году или номинальный фонд рабочего времени Тн зависит от принятого режима работы цеха. При работе по режиму непрерывной рабочей недели без остановок в праздничные дни номинальный фонд Тн совпадает с календарным фондом Ткал: Тн = Ткал = 365 дней. В случае остановок в праздничные дни Тн = 357 дней. При работе в 1 смену при пятидневной рабочей недели (продолжительность смены 8 ч 12 мин) Тн = 254 дням. При работе в 2 или 3 смены Тн = 261 дню. На стекольных заводах склады и отделения обработки работают в 1 или 2 смены, а дозировочно-смесительные отделения в 2 или 3 смены.
ТН = ТК – ТВЫХ – ТПРАЗД
Расчёт выпуска стекла в сутки:
М = К · V · p, т / сут
Суточное и годовое потребное количество стекломассы с учётом отходов на хальмовку:
, т/сутки;
, т/год
Зная годовое количество возвратного стеклобоя δ или его отношение ко всей навариваемой стекломассе ρ (принимается от 20 до 40%), определяют годовое количество стекломассы, навариваемой только из шихты S.
Возвратный стеклобой:
, т/год
Годовое количество стекломассы, навариваемое только из шихты:
, т/год
Отсюда вычисляется производственная мощность составного цеха – Ш или годовое количество шихты, необходимой для получения стекломассы.
, т/год
где Q - количество шихты, мас. частей на 100 мас. частей стекломассы, получаемое при расчете шихты.
Производительность составного цеха в сутки вычисляется по формуле:
, т/сутки.
Пример
Плотность оптического стекла марки БФ101: ρ = 2,66 г/см3;
Керамические горшки, объёмом V = 700 л;
Общее количество горшков n = 40 шт.;
Коэффициент заполняемости горшка К = 0,9;
Возвратный стеклобой δ = 25%.
Выбираем периодическое производство, пятидневную рабочую неделю, 24-часовой день (переменно поточное производство). Нерабочие дни – праздники, суббота и воскресение.
ТН = ТК – ТВЫХ – ТПРАЗД = 365 – 96 – 8 = 261 дней.
Расчёт выпуска стекла в сутки:
т/сутки.
Суточное и годовое потребное количество стекломассы с учётом отходов на хальмовку:
т/сутки,
т/год
Возвратный стеклобой:
т/год.
Годовое количество стекломассы, навариваемое только из шихты:
13121,25 т/год
Производственная мощность составного цеха или годовое количество шихты, необходимой для получения стекломассы:
т/год
Производительность составного цеха в сутки:
т/сутки.
Исходными данными для расчета производственной программы составного цеха или дозировочно-смесительного отделения являются мощность цеха – Ш, а также состав и количество шихты на 100 мас. частей стекла Q. Статьи производственной программы рассчитываются тем же табличным методом при движении слева направо (табл.7.3) Вначале определяют годовую потребность в обработанных (кондиционных) сырьевых материалах из выражений вида:
;
;
;
где П, Г, И, - количества песка, глинозема, известняка в шихте, масс. частей на 100 мас. частей стекла.
Затем вычисляется годовая потребность в сырьевых материалах, которые поступают на хранение и обработку в сухом виде:
;
;
;
где φП, φГ, φИ - отходы сырьевых материалов при хранении и обработке, %
Они берутся по нормам технологического проектирования (табл. 7.4)
Таблица 7.3.
Производственная программа составного цеха
Наименование сырьевых материала |
Состав шихты масс.ч на 100 м.ч. стекла |
Требуется для производст ва шихты в т/год |
Отходы при хранении и обработк, % |
Поступает на хранение и обработку в сухом виде, т/год |
Влажность сырьевых материалов, % |
Расходы влажных материалов со склада |
||
т/год |
т/сут |
т/ч |
||||||
Песок |
П |
П1 |
φп |
П2 |
ωп |
П3 |
П4 |
П5 |
Глинозем |
Г |
Г1 |
φг |
Г2 |
ωг |
Г3 |
Г4 |
Г5 |
Известняк |
И |
И1 |
φи |
И2 |
ωи |
И3 |
И4 |
И5 |
Доломит |
Д |
Д1 |
φд |
Д2 |
ωд |
Д3 |
Д4 |
Д5 |
Сода |
С |
С1 |
φс |
С2 |
ωс |
С3 |
С4 |
С5 |
ИТОГО: |
Q |
Ш |
- |
∑ |
- |
∑ |
∑ |
∑ |
Или по данным производственной практики Годовой расход сырьевых материалов с учетом складской влажности определяют по формулам вида:
;
;
;
где ωп, ωг, ωи – складская влажность сырьевых материалов (табл.7.4).
Таблица 7. 4
Производственные потери сырьевых материалов при хранении и обработке
Наименование материала |
Поступление сырья в обработанном виде |
Поступление сырья в необработанном виде |
||
Складская влажность, % |
Потери сырья при хранении и обработке, % |
Складская влажность, % |
Потери сырья при хранении и обработке, % |
|
Песок |
1,0 |
0,5 |
5,0 |
7,0 |
Доломит |
1,0 |
1,0 |
6,0 |
6,0 |
Сода |
1,5 |
2,0 |
- |
- |
Сода гранулированная |
3,0 |
2,0 |
- |
- |
Сульфат технический |
2,0 |
2,0 |
- |
- |
Сульфат гранулированный |
1,0 |
2,0 |
- |
- |
Натриевая селитра |
5,0 |
3,0 |
- |
- |
Калиевая селитра |
2,0 |
3,0 |
- |
- |
Поташ |
8,0 |
2,0 |
- |
- |
Содопоташная смесь |
1,1 |
1,0 |
- |
- |
Известняк |
1,0 |
1,0 |
6,0 |
6,0 |
Мел кусковой |
- |
- |
12,0 |
6,0 |
Мел молотый |
3,0 |
1,0 |
- |
- |
Селитра кальциевая |
До 15,0 |
5,0 |
- |
- |
Глинозем |
1,0 |
1,0 |
- |
- |
Полевошпатовый концентрат |
1,0 |
1,0 |
- |
- |
Полевой шпат |
1,0 |
1,0 |
6,0 |
4,0 |
Нефелиновый концентрат |
1,0 |
3,0 |
- |
- |
Бура техническая |
- |
1,0 |
- |
- |
Борная кислота |
1,0 |
1,0 |
- |
- |
Сурик свинцовый |
0,3 |
0,5 |
- |
- |
Барий углекислый |
1,0 |
1,0 |
- |
- |
Барий азотнокислый |
0,5 |
1,0 |
- |
- |
Цинковые белила |
0,1 |
2,0 |
- |
- |
Сода из нефелинового сырья |
1,0 |
1,0 |
- |
- |
Кремнефтористый натрий |
1,0 |
2,0 |
- |
- |
Криолит |
1,0 |
1,0 |
- |
- |
Уголь |
- |
- |
10,0 |
5,0 |
Для последующего расчета ПП и подбора технологического оборудования составного цеха представляется важным определение суточного и часового расхода сырьевых материалов со склада. Суточный расход сырьевых материалов со склада определяется по выражениям типа:
;
;
;
При определении часового расхода сырьевых материалов принимают
количество рабочих часов в сутки τн в зависимости от числа рабочих смен (8,
16 или 24):
;
;
;
По данным производственной программы составного цеха рассчитывается удельный расход сырьевых материалов на 1 тонну стекломассы, навариваемой из шихты, по формулам:
;
;
;
Удельный расход шихты на 1 тонну стекломассы, равной сумме удельных расходов компонентов, вычисляют по выражению:
По расчетам производственной программы составляется заявка на транспорт.
Таблица 7.5
Заявка на транспорт
Наименование сырьевого материала |
Вид транспорта |
Расход материала со склада |
Кол-во транспорта, вместимость |
Частота привоза |
||
т/год |
т/квартал |
т/мес |
||||
Фосфорная кислота |
цистерна |
14951,79 |
1243,09 |
3729,27 |
20 шт по 60 т |
1 раз в месяц |
Окись сурьмы |
машина |
26,78 |
6,70 |
2,23 |
16 шт по 10 т |
1 раз в месяц |
И т. д. |
При разработке технологической схемы составного цеха обосновываются основные требования к качеству стекольных шихт. С одной стороны, эти требования рассматриваются в тесной связи с процессами стекловарения, производительностью стекловаренных печей и качеством стекломассы. С другой стороны, качество стекольных шихт является следствием тех требований, которые предъявляются к способам хранения и обработке сырьевых материалов и их смешиванию.
Технологические схемы составного цеха разрабатываются для каждого сырьевого материала применительно к его исходному виду, твердости, влажности и другим свойствам. Традиционные технологические схемы обработки некондиционных сырьевых материалов включают значительное количество операций (рис.5.1).
Таблица 5.1
Технологические схемы обработки сырьевых материалов и подготовки шихты в составном цехе
Кварцевый песок |
Доломит, известняк |
Сода, поташ |
Сульфат натрия |
Каменный уголь |
Стеклобой |
||||||
Приемный бункер |
Приемный бункер |
Приемный бункер |
Приемный бункер |
Приемный бункер |
Приемный бункер |
||||||
Питание |
Питание |
Просеивание |
Питание |
Питание |
Питание |
||||||
Сушка |
Дробление |
Расходный бункер |
Дробление |
Помол |
Дробление |
||||||
Просеивание |
Сушка |
Взвешивание |
Сушка |
Просеивание |
Магнитная сепарация |
||||||
Расходный бункер |
Помол |
Помол |
Взвешивание |
Промывка |
|||||||
Взвешивание |
Просеивание |
Просеивание |
Смешивание |
Инспекция |
|||||||
Расходный бункер |
Усреднение |
Расходный бункер |
Расходный бункер |
||||||||
Взвешивание |
Взвешивание |
Взвешивание |
Взвешивание |
||||||||
Смешивание |
|||||||||||
Расходный бункер |
|||||||||||
Взвешивание |
|||||||||||
Увлажнение и смешивание компонентов шихты |
|||||||||||
Хранение шихты |
|||||||||||
Транспортировка к стекловаренной печи |
|||||||||||
Использование кондиционных материалов, предварительно обработанных на централизованных сырьевых базах, позволяет значительно упростить технологические схемы (табл.5.2) и превратить составные цеха в дозировочно-смесительные отделения.
Таблица 5.2
Технологические схемы дозировочно-смесительного отделения
Кварцевый песок, сода |
Доломит, известняк |
Полевошпатный концентрат, глинозем |
||||
Хранение в силосе |
Хранение в силосе |
Приемный бункер |
||||
Питание |
Питание |
Питание |
||||
Просеивание |
Просеивание |
Просеивание |
||||
Расходный бункер |
Расходный бункер |
Расходный бункер |
||||
Взвешивание |
Взвешивание |
Взвешивание |
||||
Увлажнение и смешивание |
||||||
Хранение шихты |
||||||
Транспортировка к печи |
||||||
При рассмотрении технологической схемы обосновывается необходимость проведения технологических операций дробления, сушки, помола, просеивания, дозировки, смешивания, увлажнения. Обсуждаются условия хранения необработанных и обработанных сырьевых материалов и готовой шихты. Принимаются технологические параметры обработки сырьевых материалов и подготовки шихты: степень дробления и величина частиц получаемого щебня, температуры сушки, размеры ячеек, сит или зерен сырьевых материалов, влажность и однородность шихты.
Подчеркиваются реализованные в проекте научно-технические достижения. Принятие таких технологических решений как использование силосов – промежуточных емкостей и силосов – расходных бункеров, применение пневмо- и вакуум-транспорта, организация новых способов подготовки шихт-грануляции, брикетирования, бункеров – дозаторов для малого количества шихты, тензо – метрические тележки (проверить) и других обосновывается с учетом влияния этих решений на производительность стекловаренного цеха и качества стекломассы.
Все стадии технологического процесса подробно рассматриваются и обосновываются. Способ загрузки шихты, совместное или раздельное введение шихты и боя, возможность компактирования шихты перед загрузкой рассматриваются и принимаются с учетом их воздействия на процессы стекловарения.
6. Выбор способов хранения сырья, расчет площади склада и емкости силосов и расходных бункеров6.1. Расчет площадей крытых механизированных складов
При проектировании составных участков целесообразно использовать типовые проекты крытых механизированных складов в соответствии с нормами запаса сырьевых материалов каждого типа [13].
Площади отсеков (Si, м2) для материалов, поступающих на предприятие «навалом», рассчитывается по формуле:
,
Где - суточный расход
материала со склада, т/сут;
- норма запаса
сырьевого материала, сут;
- насыпная масса
материала, т/м3;
h – нормативная высота насыпки материала в отсеке, оборудованном мостовым краном, м;
К – коэффициент, учитывающий полноту заполнения отсека (0,7 – для крупнокусковых, 0,8 – для мелкокусковых материалов).
В складах, оборудованных грейферным краном, высота насыпки песка – 8 м, звестняка, доломита – 5-6 м, угля – 5 м. Для малооборудованных складов высота насыпки сырьевых материалов не более 2-3 м.
В настоящее время в кондиционном виде (в таре) на стекольные заводы поступают пегматит, глинозем, нефелиновый и полевошпатовый концентраты, сода, сульфат и другие материалы.
Сырьевые материалы, поступающие затаренными в мешки, на складе укладываем штабелями. В этом случаи площадь складов (отсеков) увеличивают на 30% под проходы между штабелями.
Расчет площади складов для хранения затаренных материалов определяют по формуле:
,
где – суточный расход
материала со склада, т/сут;
– норма запаса
сырьевого материала, сут;
– насыпная масса
материала, т/м3;
- нормативная
высота насыпки материала в отсеке, оборудованном мостовым краном (принимается 4
м);
– коэффициент,
учитывающий плотность укладки мешков (принимается равным 0,8);
– коэффициент,
учитывающий площадь проходов между штабелями (принимается равным 0,7).
Расчет площади складов для хранения затаренных материалов, поступающих в биг-бегах:
Sбиг-бега = 1 · 1 = 1 м2
Vбиг-бега = 1 т
Расчет площади склада затаренных материалов, которые поступают в цистерне:
Vбочки = Sосн · h,
где h – высота бочки,
Sосн – площадь основания бочки,
Vбочки – объем одной бочки.
,
где R – радиус основания бочки.
m = V
· ρ,
где m – масса сырьевого материала, которая входит в одну бочку,
ρ – плотность сырьевого материала.
М = Mi · Ni, т / мес
n = M / m,
где n – количество бочек.
S = n · Sосн
Общая площадь склада:
,
где l – коэффициент учета проходов для погрузчика.
общая площадь склада (написать)
Начертить схему склада.
После завершения технологических расчетов разрабатываются варианты компоновки оборудования составного участка. Оптимальный вариант выбирается по критерию минимума приведенных затрат.
Проекты составных участков следует разрабатывать таким образом, чтобы в перспективе они могли работать как дозировочно-смесительные участки без какой-либо серьезной реконструкции. Это означает, что за основу следует принимать типовые проекты дозировочно-смесительных участков, применительно к которым разрабатываются участки по приемке, хранению, обработке сырья и транспортно-технологические связи.
Составные участки целесообразно проектировать в одном блоке со складами сырья. Склады сыпучего сырья (или сырья, поступающего навалом) проектируются пролетом 12, 18 и 24 м длиной, кратной 6 м и площадью отсеков под отдельные виды сырьевых материалов, обеспечивающих требуемые нормы запасов сырья. Склады, если это рационально, оборудуются грейферными мостовыми кранами грузоподъемностью до 5 т. в склады большей емкости вводится железнодорожный путь широкой колеи вдоль складских отсеков. Возможен и другой вариант, когда склад сырья располагается на основной железной магистрали, выполняя роль промежуточного склада. На заводской склад сырьевые материалы могут доставляться с промежуточного склада автомобильным транспортом.
Полы склада сыпучих материалов заглубляются на отметку -2.00, а полы склада затаренных материалов проектируются на отметке 0.00.
Склады затаренного сырья могут примыкать к торцу склада сыпучих материалов.
Железнодорожный путь в складе сыпучих материалов проходит по эстакаде при отметке головки рельса 0.00.
Соответственно различным видам сырьевых материалов склады разделены подпорными стенками на отсеки. Стенки отсека выводятся до отметки +2.00, выше этой отметки штабели хранимых материалов выводятся по углу естественного откоса.
При доставке на склад сырья автотранспортом в наружной стенке строго напротив отсека проектируются ворота. Составной участок имеет постоянную этажность, равную единице, но возможна и переменная этаность от одного до четырех. Высота этажей принята кратной модулю 0.9 м.
При компоновке оборудования составного участка следует руководствоваться следующими основными положениями.
1) Склады сырьевых материалов необходимо располагать в непосредственной близости к дозировочно-смесительному отделению (участку), в одном здании.
2) Для каждого сырьевого материала на складе выделяются отсеки надлежащей площади, из которых материалы подаются в соответствующие агрегаты для обработки.
3) Агрегаты для обработки сырьевых материалов располагаются по принципу поточности, один за другим, с механизированной подачей материалов, образуя непрерывную технологическую ветвь (линию).
4) Грейферные краны выполняют функцию подачи материалов со склада на соответствующие линии их обработки. Обработанные материалы подаются в дозировочно-смесительное отделение (участок) механическими транспортными средствами (ленточными транспортерами, элеваторами, пневмотранспортом).
5) Складские отсеки для хранения затаренных материалов оборудуются растаривателями. В качестве транспортирующих средств здесь часто используется электропогрузчики.
6) Дозировочно-смесительные отделения (участки) включают систему расходных бункеров, оборудования контрольного просева, автоматических весов, располагающихся над ленточным конвейером сборки компонентов шихты и подачи их в смеситель.
7) Следует отдавать
предпочтение компактированной шихте нежели сыпучей. Для этого на составном
участке предусматривается отделение компактирования.
Таблица 5 |
Нормы запасов сырья и обработанных материалов |
При работе на обогащенном сырье в дозировочно-смесительных отделениях |
Насыпная масса, т/м3 |
11 |
1,5 |
1,2 – 1,3 |
1,5 |
0,6 – 0,7 |
1,1 – 1,3 |
1,0 |
Запас в расходных бункерах, сутки |
10 |
2 |
2 |
2 |
1 |
1 |
1 |
|||
Запас в силосных банках, сутки |
9 |
15 |
15 |
15 |
15 |
15 |
15 |
|||
Способ хранения |
8 |
Насыпью в силосной банке |
-“- |
-“- |
Насыпью в силосной банке или таре |
-“- |
Насыпью в силосной банке или в расходных бункерах |
|||
При работе на необогащенном сырье в составных цехах |
После обработки |
Насыпная масса, т/м3 |
7 |
1,5 |
1,2 – 1,3 |
1,4 – 1,5 |
0,6 – 0,7 |
1,1 – 1,3 |
1,0 |
|
Запас, сутки |
6 |
2 |
2 |
2 |
1/2 |
2 |
2 |
|||
Способ хранения |
5 |
В бункере |
-“- |
-“- |
-“- |
-“- |
-“- |
|||
До обработки |
Насыпная масса, т/м3 |
4 |
1,6 – 1,7 |
1,6 – 1,9 |
1,7 – 2,0 |
0,6 – 0,7 |
1,1 – 1,3 |
1,2 |
||
Запас на складе, сутки |
3 |
30 |
30 |
30 |
30 15 |
30 |
30 |
|||
Способ хранения |
2 |
Насыпью в крытом складе |
-“- |
-“- |
В таре в крытом складе или силосной банке |
-“- |
В таре в крытом складе |
|||
Наименование материалов |
1 |
Песок |
Известняк |
Доломит |
Сода |
Сода гранулированная |
Сульфат карабугазский |
11 |
1,3 – 1,5 |
1,7 |
1,7 |
1,7 – 1,8 |
1,1 |
1,1 |
0,8 |
10 |
1 |
2 |
2 |
2 |
2 |
1 |
1 |
9 |
15 |
15 |
15 |
15 |
15/30 |
30 |
30 |
8 |
-“- |
Насыпью в силосной банке |
-“- |
Насыпью в силосной банке или расходных бункерах |
Насыпью в силосной банке, в расходных бункерах или в таре в крытом складе |
В таре в крытом складе |
-“- |
7 |
1,3 – 1,5 |
1,7 |
1,7 |
1,7 – 1,8 |
1,1 |
1,1 |
1,1 |
6 |
½ |
2 |
2 |
2 |
2 |
1 |
1 |
5 |
В бункере |
-“- |
-“- |
-“- |
-“- |
-“- |
-“- |
4 |
1,3 – 1,5 |
2,0 |
1,7 |
1,7 – 1,8 |
1,1 – 1,4 |
1,1 |
0,8 |
3 |
30 |
30 |
30 |
30 |
30 |
30 |
30 |
2 |
Насыпью или в таре в крытом складе |
-“- |
-“- |
Насыпью 30 в крытом складе |
Насыпью в таре или крытом складе |
В таре в крытом складе |
-“- |
1 |
Сульфат технический |
Полевой шпат |
Полевошпатовый концентрат |
Пегматит |
Мел |
Селитра |
Поташ |
11 |
0,8 |
0,96 – 1,22 |
1,0 – 1,2 |
1,31 – 1,63 |
1,5 – 1,72 |
0,8 – 1,1 |
0,78 |
3,05 |
10 |
1 |
1 |
1 |
В таре |
В таре |
В таре |
1 |
1 |
9 |
15 |
30 |
15 |
15 |
30 |
30 |
30 |
30 |
8 |
Насыпью в силосных банках, в расходных бункерах, в таре в крытом складе |
Насыпью или в силосной банке |
Насыпью в силосной банке или расходных бункерах |
Насыпью или в таре в крытом складе |
В таре в крытом складе |
-“- |
-“- |
-“- |
7 |
0,8 |
0,96 – 1,22 |
1.0 – 1,2 |
1,31 – 1,63 |
1,5 – 1,72 |
0,8 – 1,1 |
0,78 |
3,05 |
6 |
2 |
2 |
2 |
2 |
2 |
1 |
1 |
1 |
5 |
-“- |
В бункере |
-“- |
В таре |
-“- |
В бункере |
-“- |
-“- |
4 |
0,8 |
0,96 – 1,22 |
1,0 – 1,2 |
1,31 – 1,63 |
1,5 – 1,72 |
0,8 – 1,1 |
0,78 |
3,05 |
3 |
30 |
30 |
30 |
30 |
30 |
30 |
30 |
30 |
2 |
Насыпью или в таре в крытом складе |
Насыпью или в таре |
Насыпью в крытом складе |
Насыпью или в крытом складе |
В таре в крытом складе |
-“- |
-“- |
-“- |
1 |
Содопоташная смесь |
Глинозем |
Гидроокись Al |
Нефелиновый концентрат |
Датолитовый концентрат |
Бура техническая |
Борная кислота |
Глет |
11 |
3,05 |
1,6 |
0,8 – 0,9 |
0,51 – 0,92 |
0,7 |
|
10 |
1 |
В таре |
1 |
В таре |
1 |
1 |
9 |
30 |
30 |
15 |
30 |
30 |
30 |
8 |
-“- |
В таре в крытом складе |
Насыпью в крытом складе |
В таре в крытом складе |
В таре в крытом складе |
Насыпью в крытом складе |
7 |
3,05 |
1,6 |
0.8 – 0,9 |
0,51 – 0,92 |
0,7 |
|
6 |
1 |
1 |
1 |
2 |
||
5 |
-“- |
В таре |
В бункере |
В таре |
В бункере |
-“- |
4 |
3,05 |
1,8 |
0,84 |
0,51 – 0,92 |
0,8 |
|
3 |
30 |
30 |
30 |
30 |
30 |
30 |
2 |
-“- |
В таре в крытом складе |
Насыпью в крытом складе |
В таре в крытом складе |
-“- |
Насыпью в крытом складе |
1 |
Сурик свинцовый |
Барий углекислый |
Плавиковый шпат |
Криолит технический |
Оксид цинка |
Уголь |
6.2. Расчет емкости и размер силосных складов
Типовые проекты дозировочно-смесительных отделений предусматривают
хранение материалов в силосных банках. Хорошо зарекомендовали себя силосы,
корпус которых имеет формы призмы и цилиндра, а дно – форму усеченного конуса
или усеченной пирамиды. Для сырьевых материалов, используемых в стеклоделии,
угол наклона стенок пирамидальной части приминается равным 55.
Исходные данные для расчета силосов:
1) Суточная потребность в каком-либо сырьевом материале, Мсi, т/сут;
2) Норма запаса, Ni, сут.
Общий объем силоса (Voб) определяется по формуле:
,
где – насыпной вес
сырьевого материала, т / м3,
0,8 –
коэффициент, учитывающий полноту заполнения силоса,
H
h
d
k D
Рисунок 3 – Форма и характеристические размеры силосов
Из технических соображений d принимаем равным 1м, H = 2D. Объем усеченного конуса Vук = 1/6 * Vобщ, тогда объем цилиндрической части силоса будет равен:
Vцч = Vобщ
- Vук.
Полагая, что H = 4R,
из выражения Vцч = D2H = 4
R3 можно определить радиус силоса (R, м)
R = .
Определив R, находим высоту призматической части силоса (H, м)
H = .
Высота конусной части силоса h определяется
из условия h / k = tg 55,
где k = (D – d) / 2.
Общая высота силоса равняется Hобщ = H + h.
По такой схеме рассчитываются объем и размеры силосов для песка, соды, доломита, глинозема и др. материалов.
Сырьевые материалы |
Высота силоса, м |
Кол-во силосов, шт |
Исходные данные для расчета расходных бункеров рекомендуется свести в таблицу по указанной ниже форме.
Наименование сырьевых материалов |
Насыпная масса, т/м3 |
Ежесуточная потреб-ность |
Запасы норма-тивные |
Принимаемая к установке емкость, м3 |
Кол-во бункеров, шт. |
||
т |
м3 |
т |
м3 |
||||
По конструктивным соображениям (рисунок 13) принимаем а = 1,5 м;
размер выпускного отверстия b принимается по таблице
2.1; угол наклона пирамидальной части бункера 55.
![]() |
|||
![]() |
|||
Рис. 13. Форма и характеристические размеры бункеров
Таблица
Минимальные размеры выпускных отверстий бункеров
Материал |
Размер выпускных отверстий, мм |
Гравий среднего размера |
300 |
Сухой песок |
150 |
Сырой песок |
450 |
Цемент |
250 |
Порода и руда с размерами кусков: До 60 мм До 100 мм До 160 мм |
300 450 500 |
Размеры выпускных отверстий даны для бункеров, не оборудованных вибраторами или другими средствами опорожнения.
Поскольку h / k
= tg 55, k = (a – b) / 2, то
.
Объем пирамидальной части бункера VП определяется по формуле:
м3,
(19)
Общий объем бункера находим по формуле:
м3,
(17)
где Мi – суточная потребность в каком-либо сырьевом материале, т / сут;
Ni – норма запаса сырьевого материала после обработки, сут;
γi – насыпной вес сырьевого материала, т / м3;
0,8 – коэффициент, учитывающий полноту заполнения силоса (можно 0,9).
Учитывая принимаемую к установке емкость бункера и коэффициент заполнения бункера, равный 0,9, по уравнению (33) определяем высоту призматической части (H)
м,
(20)
Тогда лющая высота бункера
Hобщ = H + h.
7. Подбор и расчет основного оборудования составного участка 7.1. Расчет практической производительности оборудования и коэффициента его производительностиВыбор оборудования осуществляется на основании принятых практических схем и установленного режима работы составного участка. По режиму работы определяется коэффициент использования оборудования по времени (φ), практическая производительность машин (установок), на основании которой и рекомендуется к использованию конкретный тип и марка машин.
Расчет практической производительности ведущего оборудования (Ппр) производится по формуле:
,
где Пп – технически обоснованная часовая производительность машины;
- коэффициент,
учитывающий потери материала (табл. 1).
Коэффициент использования оборудования во времени находится из соотношения
,
где Tэф – эффективный фонд работы оборудования;
Ткал – календарный фонд времени в году (365 дней).
Эффективный фонд работы оборудования равен
Тэф = Тн – Трем – То,
где Тн – номинальный фонд времени, который равен числу дней работы оборудования в зависимости от установленного режима работы производства без учета простоев оборудования из-за ремонта и технологически неизбежных остановок;
Трем – нормативное время простоя оборудования при ремонтах;
То – время технологически неизбежных остановок.
Трем и То устанавливается принятой системой ППР по ведущему технологическому оборудованию.
При работе по режиму непрерывной недели без остановок производства в праздничные дни Тн является максимальным и совпадает с Ткал, равным 365 дней. В случае остановок в праздничные дни
Тн = 365 – 8 = 357 дней.
При работе в одну смену по пятидневной рабочей недели продолжительность смены устанавливается 8 ч 12 мин, в этом случае
Тн = 365 – 103 выходных – 11 праздничных = 251 дня
При работе цеха в 2 или 3 смены их продолжительность устанавливается равной 8 ч. Чтобы обеспечить тредуемую продолжительность недели в 41 ч, каждую 8 субботу делают рабочим днем. Тогда
Тн = 365 – 96 выходных – 11 праздников = 258 дней
Могут быть и другие варианты режима работы участка.
На стекольных заводах механизированные склады сырья и отделения обогащения работают в одну или две смены, а дозировочно-смесительные отделения (ДСО) – в две или три смены.
Расчеты показывают, что коэффициент использования оборудования (φ) для составного цеха при работе в две смены по пятидневной рабочей недели изменяются за счет То и Трем в незначительном интервале значений 0,46 – 0,53.
7.2. Расчет оборудования механизированного склада сырьяДля подачи сыпучих материалов используются мостовые краны (краны-балки), оснащенные грейферами.
Исходными данными для расчета производительности грейферного крана являются:
- технологическая схема отделений хранения и обработки сырья;
- влажность сырья, ω,%;
- суточный расход сырьевого материала со склада, Мс, т/сут;
- общий суточный расход сырьевых материалов со склада, Q, т/сут.
Определяется масса материала, забираемого грейфером за 1 цикл, q, т:
,
где V – емкость грейфера, м3;
γ – насыпная масса материала, т/м3;
– коэффициент
заполнения грейфера (для мелких материалов – 0,8; для кусковых – 0,5).
С учетом показателей мощности проектируемого участка емкость грейфера (V принимается равной 1 или 1,5 м3). В силу того, что грейферный кран обслуживает все складские отсеки хранения сырья, показатель q следует рассчитывать для каждого вида материала, а затем усреднить полученные числовые значения qi по формуле
,
где n – количество сырьевых материалов.
Суточное число циклов работы грейферного крана будет равно
()
На складе в сутки поступает Мс материалов и столько же подается в расходные бункера, поэтому в расчете N принимается 2Мс.
Максимальная продолжительность одного цикла (τ, с) рассчитывается по максимальным расстояниям передвижения крана и подъема груза и составляет:
,
где – максимальное
расстояние передвижения соответственно крана, тележки и груза, м;
– скорость
передвижения соответственно крана, тележки и груза, м/с;
30 – время взятия и высыпания материала из грейфера, с.
Протяженность грузопотоков сырьевых материалов принимается согласно
выбранным технологическим схемам и рассчитанным ранее размерам складов
(например
Согласно паспортным данным грейферных кранов принимаются скорости Vк = 2 м/с, Vт = 0,67 м/с, Vг = 0,2 м/с.
Таблица 2
Скорости мостовых и подвесных кранов и талей
Тип крана |
Скорость, м/мин |
||
крана |
каретки |
грейфера |
|
Мостовой |
80 |
40 |
8 |
Подвесная кран-балка |
20-30 |
20 |
8 |
Электроталь |
- |
20 |
8 |
Общая суточная продолжительность работы крана (Т, ч) составляет:
,
где N – суточное число циклов работы грейферного крана;
t – максимальная продолжительность одного цикла, с.
Как правило, на складе к установке принимается 1 грейферный кран с технической характеристикой:
1) Грузоподъемность |
5 т |
2) Высота подъема |
16 м |
3) Пролет |
17 м |
4) Мощность электродвигателя |
58 кВт |
Обычно используют грейферы ПР 7-3.2 и ПР 7-5.0, параметры которых приведены в табл. 3.
Таблица 3
Техническая характеристика грейферов
Марка грейфера |
Грузоподъемность, т |
Объем, м3 |
Габаритные размеры в раскрытом виде, м |
ПР 7-3.2 |
3 |
0,8 |
1,2х1,8х1,7 |
ПР 7-5.0 |
2 |
1,5 |
1,5х1,97х1,91 |
При проектировании складов необходимо предусматривать механизированную разгрузку вагонов. Для этой цели могут быть использованы элеваторно-ковшовые разгрузчики (С-492, ПЭ-240), виброразгрузчики (С-656), разгрузчики железнодорожных платформ (Т-182А), вагоноопрокидыватели. Для транспортирования и штабелирования материалов в мешках, уложенных на поддоны, могут быть использованы автомобильные или аккумуляторные погрузчики, имеющие высоту подъема до 4,5 м.
Механизированный склад приемки и хранения сырьевых материалов может работать в одну смену с коэффициентом использования оборудования во времени – 0,3. При проектировании более мощных составных участков эффективность принятых решений заметно увеличивается за счет повышения коэффициента загрузки оборудования. Ниже приводятся справочные данные для расчета и подбора оборудования составных участков малых стекольных предприятий.
Пример
Рисунок - кран мостовой грейферный г/п 5 т.
Таблица
Базовые значения
Высота подъема, м |
Скорость, м/с |
||
подъема |
передвижения тележки |
передвижения крана |
|
24 |
0,8 |
0,8 |
1,6 |
Таблица
Кран мостовой грейферный г/п 5 т, режим работы А8. Технические характеристики
Пролет Lk, м |
h1, мм |
h2, мм |
L1, мм |
L2, мм |
A, мм |
B, мм |
C1, мм |
C2, мм |
F, мм |
Масса крана (c грейфером), т |
Суммарная мощность электродвигателей механизмов, кВт |
|
16,5 |
2800 |
3400 |
1500 |
1500 |
4500 |
5500 |
2100 |
800 |
100 |
21,9 |
78 |
|
22,5 |
1500 |
1500 |
4500 |
5500 |
2100 |
800 |
200 |
26,8 |
81,4 |
|||
28,5 |
1500 |
1500 |
4800 |
6200 |
2200 |
800 |
400 |
33,9 |
85 |
|||
32 |
1500 |
1500 |
5400 |
6800 |
2400 |
800 |
400 |
38,2 |
93 |
|||
42 |
1500 |
1500 |
7000 |
8600 |
2650 |
1100 |
500 |
52,6 |
100 |
Таблица
Кран мостовой грейферный г/п 10 т, режим работы А8. Технические характеристики
Пролет Lk, м |
h1, мм |
h2, мм |
L1, мм |
L2, мм |
A, мм |
B, мм |
C1, мм |
C2, мм |
F, мм |
Масса крана (c грейфером), т |
Суммарная мощность электродвигателей механизмов, кВт |
|
16,5 |
3900 |
4600 |
1500 |
1900 |
4500 |
5500 |
2200 |
800 |
200 |
31,9 |
140 |
|
22,5 |
1500 |
1900 |
4500 |
5500 |
2200 |
800 |
200 |
39,1 |
148 |
|||
28,5 |
1500 |
1900 |
4800 |
6200 |
2500 |
800 |
300 |
48,4 |
148 |
|||
32 |
1500 |
1900 |
5400 |
6800 |
2500 |
800 |
400 |
53,6 |
148 |
|||
42 |
1500 |
1900 |
7000 |
8600 |
2800 |
1100 |
500 |
74,3 |
162 |
Выбор ленточного транспортера, как и другого оборудования составного участка, производится по часовому расходу материала, М, т/ч:
,
()
где Мс – суточный расход материала, т/сут;
n – число смен в сутки;
t – продолжительность рабочей смены, ч;
ψ – коэффициент использования оборудования (при двухсменной и односменной работе обычно не учитывается).
В стекольной промышленности для подачи сырьевых материалов, а в некоторых случаях и шихты, широко применяются горизонтальные и наклонные транспортеры, плоские и желобчатые.
Исходные данные для расчета:
1) производительность, требуемая по какому-либо сырьевому материалу, М, т/ч;
2) длина наклонного участка транспортера, L1, м;
3) длина горизонтального участка транспортера, L2, м;
4) высота подъема груза, h, м;
5) скорость движения ленты, V, м/с;
6) насыпная масса сырьевого материала, γ, кг/м3.
Их производительность зависит от ширины ленты и скорости движения. При ширине ленты В груз на ней располагается слоем b, равным 0,9 · B – 0,05.
В
b
![]() |
Рисунок 15. Расположение груза на ленте транспортера
Производительность (П, т/ч) рассчитывается по формуле:
,
()
где с – коэффициент пропорциональности, зависящий от типа
транспортера и угла (для плоской ленты
=
15
с = 240, при
=
20
с = 325, для
желобчатой ленты при
= 30
с
= 265, при
= 45
с
= 320);
γ – насыпная масса, т/м3;
V – скорость ленты транспортера.
Расчет сводится к определению минимальной ширины транспортера, обеспечивающей требуемую производительность. Ширину ленты (В, м) находим по формуле:
м,
(21)
где К – коэффициент, учитывающий режим работы транспортера, равный 1 при трехсменной работе; 2 – при двухсменной работе; 3 – при работе в одну смену;
ψ – коэффициент, зависящий от угла наклона ленты транспортера к горизонту (табл.4).
Таблица 4
Наибольший угол наклона ленточных транспортеров с гладкой прорезиненной лентой
Наименование материала |
Допустимый угол наклона транспортера к горизонту, град |
Угол естественного откоса материалов, град |
Коэффициент, учитывающий
степень уменьшения производительности, |
Известь порошкообразная |
23 |
30 – 40 |
0,85 |
Камень сортированный |
18 |
30 – 40 |
0,90 |
Камень несортированный |
20 |
30 – 45 |
0,85 |
Песок сухой, чистый |
15 |
30 – 45 |
0,95 |
Песок рядовой из карьера |
20 |
35 – 50 |
0,95 |
Песок влажный |
20 |
35 – 50 |
0,85 |
Уголь каменный рядовой |
18 |
30 – 45 |
0,90 |
Цемент |
20 |
30 – 45 |
0,85 |
Шлак каменноугольный |
22 |
35 – 50 |
0,85 |
Щебень |
18 |
30 – 45 |
0,90 |
Стекольный бой недробленый |
12 |
- |
0,95 |
Стекольный бой дробленный |
15 |
- |
0,9 |
Таблица 5
Рекомендуемые скорости движения конвейерной ленты
Материал |
Скорость ленты, м/c, при ширине ленты, мм |
|||
400 |
500 – 650 |
800 – 1000 |
1200 – 1400 |
|
Песок, пегматит, доломит, известняк (дробленые) |
1,0 – 1,6 1,0 – 1,25 |
1,25 – 2,0 1,5 |
1,6 – 3,0 1,6 – 2,0 |
2,0 – 4,0 2,0 – 3,0 |
Доломит, известняк (кусковые) |
- |
1,0 – 1,6 |
1,6 |
1,6 – 2,0 |
Сода, поташ |
- |
0,6 – 0,9 |
1,0 – 1,25 |
- |
Угол подъема наклонного участка определяется из соотношения
.
Если допустимый угол наклона транспортера к горизонту (табл. 4) для данного сырьевого материала больше
рассчитанного по формуле (13) угла ,
то транспортируемый материал хорошо удерживается на ленте транспортера.
Принимается к установке ближайшая по стандарту ширина ленты (табл. 5).
Элеваторы в стекольной промышленности служат для транспортирования сыпучих материалов в вертикальном направлении.
Исходные данные для расчета:
1) часовая потребность в сухом материале, М, т/ч;
2) насыпная масса
сырьевого материала, , т/м3;
3) коэффициент
использования элеватора во времени, = 0,52.
Выбор типа элеватора осуществляется по величине погонной мощности
ковшей элеватора . Требуемую погонную
мощность элеватора можно определить из выражения:
,
где V – скорость движения ленты элеватора (или скорость тягового органа), м/с;
io – объем ковша, м3;
d – расстояние между осями ковшей, м;
φ – коэффициент заполнения ковшей, равный 0,6 – 0,8.
С учетом характеристики транспортируемого материала по табл. 6 выбирается скорость тягового органа и коэффициент заполнения ковшей.
Таблица 6
Рекомендации по выбору ковшей элеватора
Наименование материала |
Скорость тягового органа, м/с |
Тип ковша |
Коэффи-циент заполнения ковша |
Способ |
|
загрузки |
разгрузки |
||||
Пылевидный сухой цемент, сырьевая мука, зола ТЭЦ |
0,6 – 0,8 |
Г |
0,85 |
Зачерпыванием |
Свободный самотечный |
Зернистый и мелкокусковой: известняк, шлаки |
0,4 – 0,65 |
О, С |
0,80 |
Зачерпыванием |
Самотечный направленный |
предварительно измельченные |
0,8 – 1,0 |
Г |
0,80 |
Зачерпыванием |
Свободный самотечный |
Средне- и крупнокусковые сырьевые материалы |
0,4 – 0,6 |
О, С |
0,6 – 0,8 |
Зачерпыванием |
Самотечный направленный |
Г – глубокий ковш, О – остроугольный ковш с бортовыми направляющими, С – ковш со скругленными дном и бортовыми направляющими.
По уравнению (14) определяется погонная мощность элеватора, а по табл. 7 – размер ковшей.
Таблица 7
Основные размеры ковшей элеватора
Ширина ковша, мм |
Ширина ленты, мм |
Шаг ковшей, мм |
Объем ковшей, 10-3 м3 |
||||
расставленных |
сомкнутых |
глубоких |
мелких |
С бортовыми направляющими |
|||
С остроуго-льным днищем |
Со скругле-нным днищем |
||||||
100 |
125 |
200 |
- |
0,2 |
0,10 |
- |
- |
125 |
150 |
320 |
- |
0,4 |
0,20 |
- |
- |
160 |
200 |
320 |
160 |
0,6 |
0,35 |
0,65 |
- |
200 |
250 |
400 |
200 |
1,3 |
0,75 |
1,30 |
- |
250 |
300 |
400 |
200 |
2,0 |
1,40 |
2,00 |
- |
320 |
400 |
500 |
250 |
4,0 |
3,70 |
4,00 |
6,4 |
400 |
500 |
500 |
320 |
6,3 |
4,20 |
8,00 |
14,0 |
500 |
- |
630 |
400 |
12,0 |
- |
7,80 |
28,0 |
650 |
- |
630 |
500 |
18,0 |
- |
- |
60,0 |
800 |
- |
800 |
630 |
32,0 |
- |
- |
118,0 |
1000 |
- |
900 |
630 |
45,0 |
- |
- |
148,0 |
Наиболее распространенным типом вертикальных ковшовых элеваторов, используемых в стекольной промышленности, являются тип ЭЛ. Они предназначены для транспортирования сыпучих порошкообразных и мелкокусковых материалов. Выпускаются двух исполнений: ЭЛГ – с глубоким скругленным ковшом для сухих, хорошо высыпающихся материалов; ЭЛМ – с мелким скругленным ковшом, склонных к некоторому слеживанию.
Мощность по приводному валу (N0, кВт), потребляемая для работы элеватора, рассчитывается по формуле:
,
()
где П – часовая производительность элеватора (принимается равной M), т/ч;
h – высота элеватора (принимается согласно графической части проекта), м;
Кэ – коэффициент, зависящий от типа элеватора и его производительности (для ленточных при производительности до 20 м3/ч Кэ = 1,5);
Мощность двигателя для привода конвейера (N, кВт):
()
где - КПД механизма
привода (0,85).
Таблица
Техническая характеристика ленточных элеваторов типа ЛГ с глубокими расставленными ковшами
Наименование параметра |
Типоразмер элеватора |
||||
ЛГ-120 |
ЛГ-160 |
ЛГ-200 |
ЛГ-250 |
||
Производительность, м³/ч |
5,0 |
13,0 |
18,0 |
28,0 |
|
Ковши |
тип ковша |
глубокий |
глубокий |
глубокий |
глубокий |
ширина, мм |
120 |
160 |
200 |
250 |
|
ёмкость, л |
0,2 |
0,9 |
1,3 |
2,8 |
|
шаг, мм |
200 |
320 |
400 |
400 |
|
Скорость движения ковша, м/с |
2,2 |
2,2 |
2,2 |
2,2 |
|
Высота транспортирования, мм |
от 5830 до 55630 |
||||
Диаметры барабана, мм |
приводного |
250 |
400 |
400 |
500 |
натяжного |
220 |
320 |
320 |
400 |
|
Мощность привода, кВт |
от 1,5 до 45 |
||||
Тяговый орган |
лента резинотканевая по ГОСТ 20-85 |
Таблица
Техническая характеристика ленточных элеваторов типа ЛМ с мелкими расставленными ковшами
Наименование параметра |
Типоразмер элеватора |
||||
ЛМ-160 |
ЛМ-200 |
ЛМ-250 |
ЛМ-320 |
||
Производительность, м³/ч |
5,6 |
10,0 |
21,8 |
32,0 |
|
Ковши |
тип ковша |
мелкий |
мелкий |
мелкий |
мелкий |
ширина, мм |
160 |
200 |
250 |
320 |
|
ёмкость, л |
0,5 |
0,75 |
1,9 |
3,8 |
|
шаг, мм |
320 |
400 |
400 |
500 |
|
Скорость движения ковша, м/с |
1,5 |
1,5-2,0 |
1,85 |
1,85 |
|
Высота транспортирования, мм |
от 5830 до 55630 |
||||
Диаметры барабана, мм |
приводного |
400 |
400 |
500 |
500 |
натяжного |
320 |
320 |
400 |
400 |
|
Мощность привода, кВт |
от 1,5 до 45 |
||||
Тяговый орган |
лента резинотканевая по ГОСТ 20-85 |
Таблица
Техническая характеристика ленточных элеваторов типа ЛО с остроугольными сомкнутыми ковшами
Наименование параметра |
Типоразмер элеватора |
||||
ЛО-160 |
ЛО -200 |
ЛО-250 |
ЛО-320 |
||
Производительность, м³/ч |
6,3 |
12,5 |
19,0 |
30,0 |
|
Ковши |
тип ковша |
остроугольный сомкнутый |
остроугольный сомкнутый |
остроугольный сомкнутый |
остроугольный сомкнутый |
ширина, мм |
160 |
200 |
250 |
320 |
|
ёмкость, л |
0,65 |
1,3 |
2,0 |
4,0 |
|
шаг, мм |
160 |
200 |
200 |
320 |
|
Скорость движения ковша, м/с |
0,40-0,63 |
0,40-0,63 |
0,40-0,63 |
0,40-0,63 |
|
Высота транспортирования, мм |
от 5830 до 55630 |
||||
Диаметры барабана, мм |
приводного |
400 |
400 |
500 |
500 |
натяжного |
320 |
320 |
400 |
400 |
|
Мощность привода, кВт |
от 1,5 до 45 |
||||
Тяговый орган |
лента резинотканевая по ГОСТ 20-85 |
Рисунок 12 – Элеватор ЛГ-120
Работа элеватора происходит следующим образом (рис.13):
Насыпной груз поступает в нижнюю часть элеватора через загрузочную воронку, засыпается в ковши, поднимается вверх и выдается за счёт центробежной силы через разгрузочный патрубок, расположенный в верхней части. При подаче материала в загрузочный носок нижней секции необходимо обеспечить равномерность подачи материала. Перегрузка элеватора транспортируемым материалом не допускается. Производительность агрегата подающего в элеватор материал не должна превышать максимальной производительности элеватора в соответствии с данным руководством по эксплуатации. Неравномерная, превышающая производительность элеватора подача материала может привести к заклиниванию натяжного барабана и останову элеватора.
Рисунок 13 – Вертикальный ленточный ковшовый элеватор
Элеватор ленточный состоит из следующих основных составных частей: 1 — тяговый орган; 2 — ковш; 3 — приводной барабан; 4 — останов; 5 — привод; 6 — разгрузочный патрубок; 7 — шпиндель натяжного устройства ленты; 8 — загрузочный патрубок, ак – шаг ковшей, Вк – ширина ковша, А – длина ковша, h – высота ковша.
7.3.3.Пневмотранспорт сырьевых материалов и шихтыИспользование механического транспорта способствует загрязнению сырьевых материалов и их потере. С целью устранения указанных недостатков в настоящее время для транспортирования сырьевых материалов и стекольной шихты широкое применение получил пневмотранспорт.
Основными преимуществами пневмотранспорта являются:
1) высокая производительность за счет полной механизации процессов захвата материала при загрузке и разгрузке транспортной линии;
2) герметичность трассы перемещения и полная изоляция транспортируемого материала от внешней среды;
3) повышение безопасности труда вследствие отсутствия движущихся частей и механических приводов;
4)
сокращение обслуживающего
персонала ввиду простоты обслуживания
установок пневмотранспорта;
5) исключение потерь материала от распыления;
6) простота установки и управления ею, легкость монтажа и замены частей;
7)
возможность
осуществления полной автоматизации всего
технологического процесса;
8)
большая гибкость направлений трассы, что позволяет осуществлять
транспортирование в весьма
стесненных по габаритам и
неблагоприятных для механического транспорта условиях;
9)
низкие капитальные затраты,
стоимость оборудования и эксплуатации
пневмотранспортных установок.
Однако пневматический транспорт имеет и недостатки:
1) ограничен
круг материалов, которые могут транспортироваться
установками пневмотранспорта;
2) сравнительно
высок удельный расход электроэнергии на тонну
перемещаемого материала;
3) высок износ стенок трубопровода, особенно в местах поворота.
4) Разгрузке с помощью пневмотранспорта подлежат сырьевые материалы, прибывающие в крытых загонах навалом, в цистернах (типа содовозов), в цистернах типа автоцементовозов (автосодовозов), в крытых вагонах в таре.
Пневмотранспорт может осуществляться следующими системами: вакуумной, напорной (высоко- и низконапорной), комбинированной.
Вакуумная система: применяется для транспортирования различных сыпучих материалов на расстояние до 150 м.
Высоконапорная система: используется для транспортирования пылевидных и мелкозернистых материалов с размером кусков 5-6 мм на расстояние до 1200 мм, а при использовании промежуточных станций - до нескольких километров.
Низконапорная система: применяется для транспортирования пылевидных и мелкокусковых материалов на расстояние до 100 м.
Комбинированная система: применяется для транспортирования материалов из нескольких точек на расстояние свыше 200 м. Сбор материала в один бункер осуществляется вакуумной и низконапорной системой, а дальнейшее транспортирование на большое расстояние – высоконапорной системой.
Транспортирование сырьевых материалов осуществляется вакуумной системой. Шихта транспортируется как напорной системой, так и вакуумной.
Пневмотранспорт сыпучих материалов в плотном слое имеет ряд преимуществ:
1) уменьшение удельного расхода воздуха на транспортирование в 15-20 раз;
2) сокращение удельного расхода энергии на сжатие воздуха в 10 раз и более;
3) уменьшение линейной скорости аэросмеси в 4-5 раз, в результате чего практически устраняется износ трубопровода;
4) повышение удельной производительности трубопроводов в 4-5 раз;
5) улучшение условий фильтрации и обеспыливания отработанного воздуха;
6) упрощение конструкции основного аппарата камерного насоса.
Технические характеристики пневмотранспортной установки в плотном слое:
Производительность |
15 т/ч |
Длинна трассы |
80 м |
Диаметр трубопровода |
60 мм |
Давление |
2,8 – 3,5 атм |
Техническая характеристика пневмотранспортных установок – в табл. 8.
Таблица 8
Техническая характеристика пневмотранспортных установок
№ установки |
Производительность, т/ч |
Объемный расход газа, м3/с |
Средняя скорость газа, м/с |
Массовая концентр. аэросмеси, кг/кг |
Суммарные потери давления, МПа |
Потребная мощность, кВт |
Удельная энергоемкость, кВт ч/т |
1 |
4,5 |
0,025 |
36,0 |
41,7 |
0,053 |
10 |
0,278 |
2.1 |
3,0 |
0,025 |
27,6 |
27,8 |
0,033 |
10 |
0,333 |
2.2 |
1,5 |
0 |
27,0 |
1,2 |
- |
- |
- |
2.3 а |
15 |
0,830 |
64,7 |
4,2 |
- |
100 |
0,330 |
2.3 б |
10 |
0,830 |
64,7 |
2,8 |
- |
100 |
0,500 |
3 |
1,0 |
0,029 |
27,4 |
8,0 |
0,020 |
10 |
0,333 |
4 |
3,0 |
0,830 |
64,7 |
0,83 |
- |
100 |
0,320 |
5 |
30,0 |
1,263 |
66,0 |
16,5 |
0,004 |
156 |
0,023 |
6 |
5,0 |
0,050 |
77,0 |
23,1 |
0,055 |
20 |
0,062 |
7 |
1,75 |
0,070 |
89,0 |
5,8 |
0,063 |
20 |
0,078 |
8.1 |
2,5 |
0,080 |
85,0 |
7,2 |
0,060 |
20 |
0,064 |
8.2 |
3,5 |
0,097 |
60,0 |
8,3 |
0,050 |
20 |
0,046 |
8.3 |
6,5 |
0,117 |
100,0 |
12,86 |
0,075 |
70 |
0,086 |
9 |
6,0 |
0,170 |
- |
8,2 |
0,060 |
70 |
0,137 |
10 |
3,5 |
0,267 |
- |
3,0 |
0,040 |
70 |
0,267 |
11 |
2,8 |
0,267 |
- |
2,4 |
0,040 |
70 |
0,446 |
Рисунок 14 – Принцип работы пневмотранспорта
Рисунок 15 – Пневмотранспортная установка
7.3.4. Подбор и расчет сушильного оборудованияИсходные данные:
1) суточный расход сырьевого материала со склада, Мс, т/сут;
2) начальная влажность материала, bн, %;
3) конечная влажность материала, bк, %;
4) напряженность сушки сырьевого материала, А, кг/м3 ч.
Напряженность сушильного барабана по количеству испаряемой влаги (за час с 1 м3) является основным показателем работы сушильного барабана. При сушке песка А = 60 – 100, известняка – 35 – 65, глины – 40-60 кг/м3 ч.
Рассчитываем количество испаряемой влаги из высушиваемого сырьевого материала влаги (W, кг/ч):
,
где Т – число часов работы барабана, ч (например, при 2-сменной работе сушильного отделения Т = 16 ч).
Объем сушильного барабана (Vб, м3) находится из соотношения:
.
По техническим данным (табл. 9) выбирается сушильный барабан с объектом, рассчитанным по соотношению (15).
Таблица 9
Техническая характеристика сушильных барабанов
Показатели |
Типоразмер |
|||
1600х11000 |
1600х8000 |
1200х6000 |
1000х5000 |
|
Объем сушильного пространства, м3 |
22,2 |
16,1 |
6,8 |
3,9 |
Наклон, |
5-3 |
5-3 |
5-3 |
4 -1 |
Угловая скорость барабана, об/мин |
2,59; 1,9 |
3,4; 4,6; 5,7 |
5 |
5 |
Мощность электродвигателя, кВт |
10 |
7 |
3,8 |
3,5 |
Габаритные размеры установки (без пылеотделяющих устройств), м3: длина ширина высота |
16 3,5 3,5 |
11,8 3,7 4,1 |
7,2 2,1 2,2 |
5,23 2,27 2,04 |
Масса металлоконструкций, т |
20 |
17,8 |
10 |
5,7 |
Выбранный размер сушильного барабана проверяется по влагоиспарительной способности (U, кг/ч), которая рассчитывается, исходя из типоразмера барабана, по уравнению:
.
Если U ≥ W, то выбор типоразмера сушильного барабана сделан правильно, в противном случае выбирается другой типоразмер.
Если после проведенного расчета, выбор сушильного барабана оказывается не целесообразным из-за малой заполняемости барабана, можно подобрать сушильные шкафы исходя из производительности.
Для примера приводятся характеристикики сушильных шкафов марки ED 720 Binder и SNOL 970/350.
Рисунок 18 – Сушильный шкаф ED 720 Binder
Таблица 14
Технические характеристики сушильного шкафа ED 720 Binder
Внешние размеры: ширина, мм |
1234 |
высота, мм |
1530 |
глубина, мм |
950 |
Внутренние размеры: ширина, мм |
1000 |
высота, мм |
1200 |
глубина, мм |
600 |
Внутренний объем, л |
720 |
Полки хромирован. (станд./макс.) |
2/16 |
Макс. нагрузка на полку, кг |
45 |
Макс. загрузка, кг |
120 |
Темп. диапазон, от 5 °C выше комнатной температуры до °C |
300 |
Темп. погрешность: при 70 °C (±°C) |
1.5 |
при 150 °C (±°C) |
2.8 |
при 300 °C (±°C) |
5.0 |
Напряжение (± 10%) 50/60 Гц (В) |
400 3/N |
Мощность, Вт |
5000 |
Рисунок – Шкаф сушильный SNOL 970/350
Таблица
Технические характеристики Шкаф сушильный SNOL 970/350
Внешние размеры: ширина, мм |
1300 |
высота, мм |
1600 |
глубина, мм |
1630 |
Внутренние размеры: ширина, мм |
900 |
высота, мм |
900 |
глубина, мм |
1200 |
Диапазон автоматического регулирования температуры, °С |
40:200 |
Время разогрева электрошкафа до номинальной температуры, без садки, мин., не более |
30 |
Стабильность температуры в установившемся тепловом режиме, без садки, °С, не хуже |
±1 |
Напряжение, В |
400 |
Хорошо зарекомендовали себя для сушки кварцевого песка сушилки «взвешенного слоя», используемые на Новосельском и Раменском ГОКах, а так же Константиновском заводе бутылочного стекла и др.
Техническая характеристика установки «взвешенного слоя»:
Сечение рабочей камеры 3,0 х 1,2 м
Высота кипящего слоя 0,3 м
Площадь пода «кипящего слоя» 3,4 м2
Производительность сушилки при начальной
влажности 6,5 % и конечной 0,1 % 5,0 т/ч
Потребное количество газов 3,1 м3/с
Пылеунос 3-4 %
Температура газов в «кипящем слое» 100-125
Габаритные размеры 3,9х2,2х4,5 м
Вес металлоконструкций 3,0 т
7.3.6. Подбор оборудования для контрольного просеваНа отечественных заводах наиболее часто используются сита-бураты. Для просева стекольного песка, соды, сульфата, мела, доломита, глинозема, полевого шпата используются сита № 1,4 – 0,7.
Выбор типа сита-бурат производится по показателю производительности, которая зависит от размера барабана сита. Для составных цехов большой производительности возможно использование инерционных грохотов.
Техническая характеристика сит-буратов и инерционных грохотов приведена в табл. 10 и 11.
Таблица 10
Техническая характеристика сит-буратов
Показатели характеристики |
Типы сит-буратов |
||||
СМ-237 |
СМ-236 |
650х1500 |
1300х2500 |
800х1250 |
|
Размер барабана, мм: диаметр большего основания диаметр меньшего основания длина |
1100 780 3500 |
1100 780 2500 |
650 550 1500 |
1300 1000 2500 |
800 600 1250 |
Число оборотов в 1 мин |
25 |
25 |
30 |
30 |
30 |
Размеры фракций, мм |
0-1; 1-3; 3-5 |
0-1 |
0-1 |
0-1 |
0-1 |
Средняя производительность, т/ч (при ситах № 1,4 – 0,7) |
3,0 |
2,0 |
1,5 |
4,5 |
1,5 |
Мощность электродвигателя, кВт |
1,7 |
1,7 |
1,0 |
1,0 |
1,0 |
Число оборотов двигателя, мин |
930 |
930 |
- |
930 |
930 |
Габаритные размеры, мм: длина ширина высота |
4813 1376 1545 |
3915 1366 1520 |
2715 1180 1005 |
3850 1600 2020 |
2500 1000 1300 |
Таблица 11
Техническая характеристика инерционных грохотов
Показатели характеристики |
М-472 |
СМ-388 |
СМ-861 |
Размеры просеивающих поверхностей, м: ширина длина |
1,2 1,82 |
1,2 1,84 |
1 1,5 |
Число ярусов сит |
3 |
2 |
2 |
Частота вращения вала вибратора, об/с |
12,3 |
12 |
12,5 |
Производительность, м3/ч |
50 |
20-30 |
4 |
Мощность электродвигателя, кВт |
4,5 |
4,5 |
4,5 |
Габаритные размеры, м: длина ширина высота |
3,97 1,55 1,35 |
2,485 1,632 1,075 |
2,85 2,05 1,22 |
Вибросита являются высокопроизводительными, эффективными и надежными аппаратами для рассева порошкообразных, зернистых и кусковых материалов и могут быть использованы для обезвоживания материалов.
Сита (рис. 19), как правило, поставляются в двухдечном варианте (рассев материалов на 3 фракции). По требованию Заказчиков на сите может быть установлен один дополнительный каркас (рассев материала на 4 фракции) или оставлен только один каркас (рассев материала на две фракции) и установлены сетки с необходимыми Заказчику размерами ячеек.
Сита выпускаются в нержавеющем исполнении или из углеродистой стали.
Достоинствами вибрационных сит типа СВ являются:
- высокая эффективность рассева;
- возможность подбора оптимальных режимов для различных материалов;
- высокая степень ремонтопригодности (замена каркаса с сеткой, в случае необходимости, осуществляется за 10…15 мин.);
- надежность аппаратов;
- пылеплотность;
- малый расход электроэнергии;
- низкие динамические нагрузки на основание.
Рисунок 19 – Сито вибрационные типа СВ2 (круглого сечения)
Особенностью работы вибрационных сит типа СВ является характер колебаний просеивающих поверхностей. В отличие от других конструкций вибрационных сит в ситах типа СВ применяется пространственная (трехкомпонентная) вибрация просеивающих поверхностей.
Подобный характер колебаний обеспечивает непрерывное изменение по величине и направлению инерционных нагрузок, что позволяет получить оптимальные условия рассева, особенно, для материалов с размерами частиц близкими к размерам ячейки сетки. Трехмерное движение просеивающей поверхности объединяет в себе движение плоскорешетного классификатора и грохота.
Рисунок 20 – Вибросито СВ2-0,4
Таблица 16
Технические характеристики вибросит
Наименование |
СВ2-0,4 |
СВ2-0,6 |
СВ2-0,9 |
СВ2-1,2 |
|
Производительность, м3/ч** |
до 0,1* |
до 0,3* |
до 0,7* |
до 1,5* |
|
Диаметр корпуса, мм |
0,4 |
600 |
900 |
1200 |
|
Ситовая поверхность, м2 |
0,11 |
0,26 |
0,6 |
1,0 |
|
Количество фракций |
1-0,4 |
2-4 |
2-4 |
2-4 |
|
Амплитуда колебаний на наружном диаметре (мм) |
веpтикальная |
1...3 |
1...2,5 |
1...2,5 |
1...2,5 |
гоpизонтальная |
1...2 |
1...2 |
1...2 |
||
Частота колебаний, Гц (кол/мин) |
24 (1440) |
22,8 (1370) |
22,8 (1370) |
22,8 (1370) |
|
Мощность привода, кВт |
0,25 |
0,37 |
0,75 |
1,1 |
|
Габаритные размеры, мм |
Длина |
590 |
1000 |
1250 |
1250 |
Ширина |
565 |
1000 |
1250 |
1250 |
|
Высота |
740 |
1237 |
1330 |
1330 |
|
Масса, кг |
51 |
143 |
240 |
444 |
* Зависит от размера ячейки сетки и характеристики просеиваемого материала.
** Принимается с учетом насыпной плотности материала
На малых предприятиях для протирки поташа, селитры, мела и сурика используются мелотерки.
Характеристика мелотерок:
Производительность 0,5 т/ч
Частота вращения ротора 29,52 об/мин
Сетка для протирки поташа, селитры и сурика № 1,6 – 0,5
Габариты: длина 1650
ширина 626
высота 1000
Мощность электродвигателя 0,7 кВт
7.3.7. Подбор сепаратораК числу вредных примесей, снижающих светопрозрачность стекла относится железо. Магнитный сепаратор серии ЛМО предназначен для удаления железного натира и других содержащих железо примесей из кварцевого песка, с том числе слабомагнитных. Сепаратор предназначен для стабилизации содержания железа в кварцевом песке, магнитная система выполнена на постоянных магнитах.
Магнитный сепаратор серии ЛМО для сухого магнитного обогащения кварцевого песка барабанного типа с высокоинтенсивной магнитной системой, что позволяет удалять слабомагнитные примеси.
Имеет следующие достоинства:
- обеспечивает наилучшее качество магнитного обогащения кварцевого песка;
- имеет водоохлаждаемую магнитную систему. Магнитный сепаратор ЛМО предназначен для обогащения горячего кварцевого песка непосредственно после сушки;
- установлен на многих стеклозаводах и ГОКах;
- имеет модификации.
Технические характеристики модификаций представлены в таблице (табл. 19).
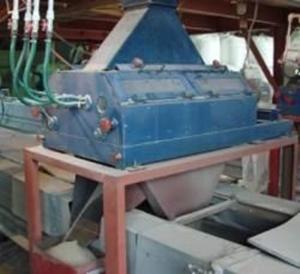
Рисунок 23 – Магнитный сепаратор ЛМО-5000-2
Таблица 19 – Основные характеристики модификаций магнитного сепаратора ЛМО.
№ |
Наименование |
Модификация |
Технические характеристики |
Назначение |
|||
Габаритные размеры, мм |
Вес, кг |
Произво-дительность, т/ч |
Напряженность (Н) и индукция (В) магнитного поля на поверхности барабана. |
||||
1 |
ЛМО-5000 |
1 |
1500х890х 400 |
600 |
5-10 |
Н 480 кА/м В более 0,6 Тл |
Удаление сильно-магнитных примесей |
2 |
ЛМО-5000-2 |
2 |
1700х890х740 |
700 |
5 |
Н 580 кА/м В более 0,75Тл |
Высоко-качественное магнитное обогащение |
3 |
ЛМО-7500-2 |
2 |
2050х890х740 |
800 |
7.5 |
Н 580 кА/м В более 0,75Тл |
Высоко-качественное магнитное обогащение |
4 |
ЛМО-5000-3 |
3 |
2050х890х740 |
800 |
5 |
Н 800 кА/м В 1,0 Тл |
Высоко-качественное магнитное обогащение |
Питатели служат для непрерывной и равномерной подачи материала в дробильно-помольные, сушильные или формующие устройства. Наибольшее распространение в стекольной промышленности получили лотковые питатели, техническая характеристика которых представлена в табл. 12.
Таблица 12
Техническая характеристика лотковых питателей
Показатели характеристики |
Лотковые питатели |
||
Л-3 |
Л-4 |
Конструкции ПКБ ГИС |
|
Размеры лотка, мм: длина ширина |
1500 460 |
1460 700 |
1500 500 |
Число ходов лотка, мин |
23 |
38 |
23 |
Производительность, т/ч |
5-12 |
20-50 |
2-20 |
Мощность электродвигателя, кВт |
1,7 |
2,8 |
4,5 |
Габаритные размеры, мм: длина ширина высота |
2690 690 485 |
2750 940 760 |
3050 950 780 |
Движение материала по наклонному лотку обеспечивается за счет создания колебаний, направленных под некоторым углом к лотку. В качестве приводов лотковых питателей используются механизмы, обеспечивающие возвратно-поступательное движение. Особое место занимают лотковые питатели с электромагнитным и пневматическим шариковым виброприводом.
Рисунок 24 – Лотковый питатель
1 - бункер, 2 - заслонка, 3 - лоток, 4 - привод.
Тарельчатые (дисковые) питатели изготовляют в зависимости от условий применения в подвесном или опорном исполнении с подвижной обоймой (рис. 25,a) либо с поворотным скребком (рис. 25,б).
Рисунок 25 – тарельчатый питатель с регулированием подачи материала путем подъема или опускания обоймы (а) либо поворотом скребка (а).
1 – тарелка, 2, 3 – обойма и механизм ее перемещения, 4 – скребок.
Рисунок 26 – Тарельчатый питатель.
Тарельчатые питатели (рис. 26) предназначены для выдачи из бункеров преимущественно мелкозернистых и мелкокусковых материалов при повышенных температурах. Такой питатель представляет собой круглую плоскую тарель, устанавливаемую под бункером и вращаемую приводом. Между бункером и тарелью устанавливаются неподвижная и подвижная манжеты и нож. По периметру тарели устраиваются направляющие борта с проемом в месте установки ножа, исключающие неорганизованное осыпание материала.
Регулирование производительности тарельчатых питателей может осуществляться за счет изменения скорости вращения тарели или сечения потока выдаваемого материала. Для автоматического регулировани0я в настоящее время используется преимущественно изменение сечения потока.
Таблица
Технические параметры тарельчатых питателей
Тип |
Модель |
Диаметр диска (мм) |
Скорость вращения диска (об/мин) |
Максимальная крупность загружаемого материала (мм) |
Производительность (т/ч) |
Мощность электродвигателя (кВт) |
Вес (кг) |
Закрытый подвесной тип |
YG300 |
300 |
10,0 |
20 |
0-1,8 |
0,55 |
115 |
YG400 |
400 |
10,7 |
20 |
0-2,6 |
1,1 |
120 |
|
YG500 |
500 |
10,7 |
20 |
0-3,3 |
1,1 |
124 |
|
YG600 |
600 |
10,0 |
20 |
0-5,0 |
1,1 |
130 |
|
YG800 |
800 |
9,0 |
30 |
0-8,0 |
1,1 |
195 |
|
YG1000 |
1000 |
9,0 |
30 |
0-12,0 |
1,5 |
263 |
|
YG1500 |
1500 |
7,0 |
40 |
0-22,0 |
5,5 |
755 |
|
Открытый подвесной тип |
DK600 |
600 |
7,53 |
25 |
1,8-3,9 |
1,1 |
410 |
DK800 |
800 |
7,53 |
30 |
3,5-7,6 |
1,1 |
600 |
|
DK1000 |
1000 |
7,5 |
40 |
1,8-16,7 |
1,5 |
800 |
|
DK1300 |
1300 |
6,5 |
50 |
4,3-27,9 |
3 |
1110 |
|
DK1600 |
1600 |
6,0 |
60 |
7,03-48,6 |
4 |
1980 |
|
DK1800 |
1800 |
5,0 |
70 |
9,26-60 |
5,5 |
3070 |
|
DK2000 |
2000 |
5,0 |
80 |
13,6-88,4 |
5,5 |
3260 |
Для дробления кусковых материалов, имеющих влажность не выше 15%, используют щековые дробилки. Для измельчения сырьевых материалов, прошедших сушку, а также стекольного боя наиболее часто используются молотковые дробилки, шаровые мельницы.
Исходные данные для подбора щековой дробилки:
1) часовой расход материала со склада, М, т/ч;
2) максимальный размер куска, d, мм;
3) насыпная масса материала, γ, т/м3;
4) коэффициент использования дробилки во времени, φ = 0,52.
Подбор дробилок осуществляется по часовой паспортной производительности (ПП, т/ч). Расчет суточной практической производительности (ППР, т/ч) выбранной дробилки производится с учетом коэффициента использования ее по времени
ППР = 24 · ПП · φ
По значению ППР при работе отделения в двухсменном режиме делается заключение об обеспечении для выбранной дробилки требуемого объема переработки материала.
Таблица 13
Технические характеристики щековых дробилок
Типоразмеры (размер загрузочного отверстия) |
Средняя производительность, т/ч |
Частота вращения проводного вала, мин-1 |
Мощность двигателя, кВт |
Габаритные размеры, мм |
Расход электроэнергии на 1 т материала, кВт |
|||||||||||
длина |
ширина |
высота |
||||||||||||||
С простым качанием щеки |
||||||||||||||||
Щ7 (330х600) |
20-30 |
220-275 |
18 |
3050 |
1790 |
1680 |
0,7 |
|||||||||
СМ 211 (500х800) |
30-90 |
225 |
40 |
2420 |
2330 |
2150 |
0,6 |
|||||||||
СМ 204 (600х900) |
70-180 |
275 |
75 |
3570 |
2400 |
3000 |
0,6 |
|||||||||
ЩК Д8 (1200х1500) |
400-600 |
100 |
280 |
7750 |
5810 |
4500 |
0,55 |
|||||||||
Со сложным качанием щеки |
||||||||||||||||
ЩДС (250х400) |
3,2-9,6 |
375 |
14 |
1470 |
1450 |
1475 |
2,2 |
|||||||||
СМ 166 (250х900) |
6,0-30 |
275 |
28 |
1352 |
2045 |
1230 |
1,5 |
|||||||||
СМ 16 (600х900) |
35-120 |
250 |
75 |
2980 |
2590 |
2430 |
1,0 |
|||||||||
ЩС (1300х2000) |
600 |
250 |
250 |
5100 |
4900 |
5300 |
0,3 |
|||||||||
80х130 |
0,05-0,2 |
300 |
1,5 |
845 |
550 |
525 |
16,5 |
|||||||||
Подбор молотковых дробилок и шаровых мельниц производится по схеме, аналогичной вышеописанной для щековой дробилки.
Молотковые дробилки промышленного класса МД 5х2 и МД 5х5 предназначены для дробления материалов средней твердости (рис.).
Дробилка молотковая может применяться при переработке отходов строительных материалов, глины, соли, кирпичной крошки, минералов, стекла, огнеупоров, шлаков и многих других материалов. Получение необходимого гранулометрического состава происходит за счет подбора разгрузочной решётки, количества молотков и их формы, а также изменения частоты вращения ротора.
Принцип действия:
Дробилка МД является изделием непрерывного действия, т.е. ее производительность определяется количеством материала, выходящего через разгрузочную решетку за единицу времени. Двигатель дробилки вращает через ременную передачу ротор. При вращении возникает центробежная сила, под воздействием которой молотки располагаются радиально относительно оси ротора.
Дробимый материал через загрузочный бункер непрерывно подается в камеру дробления, где разрушается под действием ударов молотков, ударов и трения о внутренние поверхности камеры дробления, а также самоизмельчается. Измельченный материал проходит через отверстия разгрузочной решетки, размер которых определяет крупность продукта.
При работе с блоком пылеулавливания пылевидная фракция дробленого материала захватывается воздушным потоком, создаваемым вентилятором БПУ, проходит через воздуховод и осаждается в циклоне и рукавном фильтре.
Рисунок 27 – Дробилка молотковая МД 5x2.
Таблица 14
Техническая характеристика молотковых дробилок
Типоразмер |
Диаметр ротора и длина, мм |
Частота вращения ротора, мин-1 |
Максим. размер кусков материала, мм |
Производительность, т/ч |
Мощность двигателя, кВт |
Габаритные размеры |
||
длина |
ширина |
высота |
||||||
СМ-218 |
600/450 |
1250 |
100 |
18 |
14 |
1050 |
1029 |
1122 |
«П»-образными молотками |
450/300 |
1250 |
75 |
3 |
- |
1120 |
1170 |
1250 |
ДМ-2 |
800/400 |
1300 |
100 |
16 |
35 |
|||
СМ-431 |
800/600 |
1000 |
100 |
40 |
55 |
1500 |
1255 |
1230 |
ДМ-3 |
800/800 |
1300 |
100 |
65 |
75 |
|||
СМ-19А |
1000/800 |
1000 |
300 |
85 |
115 |
2230 |
1740 |
1515 |
ДМ-5 |
1000/1200 |
950 |
200 |
125 |
150 |
|||
СМ-170Б |
1300/1600 |
1220 |
400 |
200 |
200 |
2600 |
2750 |
1900 |
МД 2х2 |
250х150 |
1500 |
20 |
0,1 |
2,2 |
830 |
550 |
1430 |
МД 5х2 |
500х200 |
1500 |
50 |
0,7 |
15 |
1600 |
560 |
1200 |
МД 5х5 |
500х500 |
1500 |
50 |
1,5 |
25 |
1750 |
840 |
1200 |
Таблица 15
Техническая характеристика шаровых мельниц с загрузкой через полую цапфу
Показатели |
ШР-4 |
ШР-5 |
ШР-6 |
ШР-8 |
Диаметр барабана, мм |
2100 |
2100 |
2700 |
3200 |
Рабочая длина барабана, мм |
1500 |
2200 |
2100 |
3100 |
Частота вращения барабана, об/с |
0,4 |
0,4 |
0,35 |
0,33 |
Производительность, т/ч |
6-16 |
7-20 |
12-35 |
35-80 |
Мощность двигателя, кВт |
125 |
160 |
300 |
600 |
Габаритные размеры, м: длина ширина высота |
6,595 4,457 3,720 |
8,07 4,79 3,79 |
8,17 4,79 3,79 |
9,63 6,385 5,12 |
Аэробильные мельницы выгодно отличаются от дробилок и шаровых мельниц тем, что в них совмещаются помол, сушка и транспортировка материала.
Аэробильные мельницы применяются для измельчения мягких и средних по твердости материалов – глины, угля, известняка и комовой извести, гипсового камня, трепела и др. Этот тип мельниц применим для работы по замкнутому циклу под вакуумом и для помола с одновременной подсушкой измельчаемых материалов горячими газами (рис.16). Основная область применения данной мельницы – сырьевой компонент шихты для получения стекла.
В аэробильную мельницу материал подается с помощью тарельчатого питателя.
Мельница требует подачи холодной воды t=10-15оС, с рабочим давлением водопровода (max 3 атм.) в рубашку охлаждения корпуса подшипников.
Рисунок 16 – Принцип работы аэробильной мельницы
Технические характеристики приведены в таблице (табл. 13), схема мельницы (рис. 17).
Для примера приводятся характеристикики аэробильной мельницы марки МПА.
Таблица 13
Технические характеристики аэробильной мельницы МПА 850*200
производительность |
до 2 т/час |
размер исходного материала |
0-70 мм |
размер измельченного продукта до 95% |
0-700 мкм |
влажность исходного продукта |
< 12% |
влажность конечного продукта |
< 0,25 % |
Температура сушки |
до 450 |
Давление,атм. |
4-5 |
Расход воды max, м3/час |
7 |
Количество электродвигателей, шт |
1 |
Число оборотов в минуту |
1500 |
Мощность электродвигателя,кВт |
55,0 |
Габариты |
1936*2627*4410 |
Масса, кг |
4745 |
Рисунок 17 – Схема мельницы.
Для более крупных производст исп аэроб мельницы большей производительности (таб)
Таблица 16
Техническая характеристика аэробильных мельниц завода «КОМЕГА»
Показатели характеристики |
Тип |
||
А |
Б |
||
Производительность, т/ч |
2,5 |
5 |
|
Расход воздуха, м3/ч |
6000 |
8000 |
|
Диаметр ротора по билам, м |
0,855 |
1,045 |
|
Допустимый подогрев воздуха, |
400 |
400 |
|
Мощность электродвигателя, кВт |
50 |
90 |
|
Число оборотов электродвигателя, об/с |
24,2 |
24,2 |
|
Габаритные размеры, м: |
длина |
2,044 |
2,324 |
ширина |
2,145 |
2,440 |
|
высота с сепаратором |
4,059 |
6,900 |
Исходные данные для расчета весов марки ДВСТ:
1) общий суточный расход сырьевого материала со склада с учетом потерь при транспортировании и обработке, М, т/сут;
2) общая продолжительность цикла, τ, ~ 7 мин;
3) насыпная масса материала, γ, т/м3;
4) коэффициент использования ДВСТ по времени – φ.
При работе ДСО в 2 смены в режиме прерывистой рабочей недели коэффициент использования ДВСТ во времени вычисляеся по формуле ():
,
(39)
где Тэф – эффективный фонд рабочего времени, сут;
К – коэффициент, учитывающий режим сменности работы линии (равен 0,33 – при односменной работе; 0,67 – при двусменной; 1 – при трехсменной);
Ткал – календарный фонд времени в году (365 дней).
Эффективный фонд работы оборудования равен:
Тэф = 365 – Твп – Тр
– Тно,
где Твп – число выходных и праздничных дней в году соответственно 104 и 11 дней;
Тр – общее годовое время ремонта (по данным ППР – 10 дней);
Тно – время неизбежных технологических остановок (1-1,5 дней).
Тэф = 365 – 104 – 11 – 10 – 1 = 239 дней
Определяется полезная емкость ковша ДВСТ (V, м3):
,
()
где
Подбор ДВСТ производится по полезной емкости ковша по табл.17. рекомендуется установка на весовой линии одного типоразмера ДВСТ. Целесообразно для каждого расходного бункера весовой линии установить свой ДВСТ.
Таблица 17
Техническая характеристика автоматических дозировочных весов ДВСТ
Показатели характеристики |
ДВСТ-5 |
ДВСТ-10 |
ДВСТ-40 |
ДВСТ-70 |
ДВСТ-150 |
ДВСТ-300П |
Пределы взвешивания, кг |
2-5 |
4 – 10 |
15 – 40 |
35 – 70 |
50 – 150 |
120-300 |
Полезный объем ковша, м3 |
0,028 |
0,02 |
0,07 |
0,16 |
0,27 |
0,27 |
Цикл взвешивания, с |
45 |
45 |
90 |
180 |
180 |
180 |
Потребляемая мощность, кВт |
- |
0,8 |
1,8 |
1,8 |
1,8 |
1,8 |
Габаритные размеры, мм: |
||||||
длина |
870 |
1630 |
2100 |
2100 |
2100 |
|
ширина |
1100 |
1295 |
1860 |
1860 |
1860 |
|
высота |
840 |
2545 |
3000 |
3000 |
3000 |
Рисунок 28 – Дозировочные весы ДВСТ-150.
Рисунок 29 – Дозировочные весы ДВСТ-10.
7.4.2. Подбор и расчет смесителей шихтыИсходные данные:
1) суточная потребность цеха в стекольной шихте, Мш, т/сут;
2) общая длительность цикла смешивания в тарельчатых смесителях – 5 мин;
3) насыпная масса шихты, γш = 1,5 т/м3;
4) коэффициент использования смесителя во времени, φ = 0,48.
Выбор смесителя производится по требуемой величине его рабочего объема (V, л):
,
()
Таблица 18
Техническая характеристика тарельчатых и планетарных смесителей
Показатели характеристики |
Смесители |
|||
тарельчатые |
планетарный |
|||
СТ-700 |
СТ-335 |
СТ-250 |
||
Вместимость чаши, л |
700 |
500 |
250 |
1000 |
Производительность, т / ч |
10-12 |
7 – 8 |
3-4 |
24-30 |
Мощность электродвигателя, кВт |
20 |
10 |
4,5 |
11,13 |
Габаритные размеры, м: длина ширина высота |
3,40 3,14 2,24 |
3,35 2,62 1,54 |
2,30 1,27 1,90 |
3,22 3,18 2,60 |
На малых стекольных предприятиях часто используются смесители, в которых взвешивание материала и смешивание их производится в кюбеле. Такие смесители обладают небольшой производительностью, просты и удобны в эксплуатации. Примером является смеситель СШ-5, техническая характеристика которого следующая:
Объем кюбеля 230 л
Коэффициент использования 0,67
Частота вращения 12,5 об/мин
Время смешивания 15-20 мин
Мощность электродвигателя 3 кВт
Габариты: длина 1850 мм
ширина 1010 мм
высота 1230 мм
Кольцевые лотковые смесители THZ компании ТЕКА для стекольной шихты, работающие в периодическом режиме, имеют емкость от 250 до 6000 литров (табл)
Рисунок 30 – Лотковый смеситель THZ для стекольной шихты.
Дно и стенки смесительного лотка защищены от износа сменной футеровкой. В зависимости от варианта применения футеровка изготовлена из проверенных на практике материалов, например, специального стального листа, специальной хромоникелевой или нержавеющей стали, износостойкого антикоррозионного материала Hardox 500, керамики с окисью алюминия.
Месильные стержни регулируются по высоте и упруго смонтированы в корпусе ротора, по желанию заказчика они могут монтироваться в сменных втулках (THZ 250 - THZ 1125). начиная с типоразмера THZ 1500 этот вид монтажа применяется в серийном исполнении. В качестве специального исполнения смесители могут поставляться с централизованной смазкой.
Месильные стержни, сменные манжеты для защиты месильных стержней от износа и скребки (рис. 31) могут изготавливаться из различных материалов на выбор заказчика: отбеленного чугуна W4, с покрытием из твердых сплавов, полиуретановых эластомеров, отбеленного чугуна (SPIKE) со штифтами из твердого сплава, специальная безникелевая сталь.
Кольцевой лотковый смеситель THZ 250 оборудован не требующим обслуживания фланцевым редукторным двигателем в качестве привода и для опорожнения.
Рисунок 31 – Месильные стержни и скребки.
Кольцевые лотковые смесители типоразмеров с THZ 375 по THZ 1125 имеют расположенный по центру планетарный редуктор с фланцевым двигателем.
Кольцевые лотковые смесители типоразмеров с THZ 1500 по THZ 6000 также приводятся в действие расположенным по центру планетарным редактором с карданным валом и двигателем на лапах. По желанию для мягкого пуска с полной нагрузкой может быть установлена промежуточная турбомуфта.
Прифланцованный к редуктору масляный насос обеспечивает циркуляцию масла и служит для опорожнения смесителя. Общая система маслоснабжения облегчает технический уход за редуктором и системой опорожнения комплексного узла.
Ротационный цилиндр приводит в действие сегментные разгрузочные заслонки с электрическим управлением, которые могут устанавливаться в любое положение с помощью не подверженных износу концевых выключателей.
Благодаря смещённому во внутрь центру вращения создается большое разгрузочное отверстие, что позволяет быстро выгрузить продукт. В качестве опции разгрузочное устройство может приводиться в действие независимо от привода смесителя через отдельный гидравлический агрегат.
В типоразмерах с THZ 375 до THZ 1125 могут монтироваться до 4, а начиная с типоразмера THZ 1500 до THZ 6000 – до 3 разгрузочных устройств. Возможна также установка устройства для выгрузки продукта с целью пробоотбора. Рабочее пространство смесителя защищено пыленепроницаемым защитным кожухом.
Максимально большие заслонки имеют разное расположение и могут приводиться в действие ручными или электрическими лебёдками. Благодаря отсутствию ограничивающих пространство надстроек возможно размещение загрузочных отверстий, патрубков, вентиляционных отверстий, заслонок для чистки, смотровых отверстий по индивидуальным проектам.
Рисунок 33 – Размеры лотковых смесителей.
Все размеры (рис. 33) указаны в мм (табл. 24). При проектировании монтажа запрашивайте монтажные чертежи. Все данные соответствуют современному уровню техники. Возможно внесение изменений, связанных с техническими усовершенствованиями
Таблица 23
Технические характеристики лоткового кольцевого смесителя THZ.
THZ |
250 |
375 |
500 |
750 |
1125 |
1500 |
1875 |
2250 |
3000 |
3750 |
4500 |
5250 |
6000 |
|
Емкость смесителя |
л. |
250 |
375 |
500 |
750 |
1125 |
1500 |
1875 |
2250 |
3000 |
3750 |
4500 |
5250 |
6000 |
Емкость (при плотности загрузки 1,2 кг/дм.куб) |
кг. |
300 |
450 |
600 |
900 |
1350 |
1800 |
2250 |
2700 |
3600 |
4500 |
5400 |
6300 |
7200 |
Число циклов |
в час |
15 - 20 |
||||||||||||
Мощность привода смесителя |
кВт |
7,5 |
11 |
15 |
22 |
30 |
37 |
45 |
55 |
75 |
90 |
110 |
132 |
160 |
Частота вращения ротора |
об/м |
35 |
37 |
30,5 |
29 |
29 |
20 |
20 |
18,5 |
18,5 |
18,5 |
18,5 |
18,5 |
18 |
Напорное давление воды |
бар |
4 - 6 |
||||||||||||
Вес нетто стандартного смесителя |
кг. |
900 |
1500 |
1900 |
2500 |
3500 |
4200 |
4600 |
6500 |
8600 |
9500 |
10300 |
11600 |
15000 |
Таблица 24
Размеры лотковых смесителей.
THZ |
A |
B |
C |
D |
E |
F |
G |
K |
N |
R |
Y |
250 |
350 |
500 |
300 |
1354 |
- |
780 |
600 |
- |
- |
400 |
500 |
375 |
450 |
485 |
370 |
1700 |
215 |
765 |
700 |
170 |
- |
400 |
550 |
500 |
550 |
485 |
410 |
1900 |
215 |
860 |
860 |
170 |
- |
400 |
650 |
750 |
650 |
500 |
473 |
2210 |
235 |
1000 |
1000 |
207 |
- |
450 |
750 |
1125 |
475 |
500 |
430 |
2520 |
265 |
1175 |
1100 |
207 |
- |
525 |
900 |
1500 |
550 |
550 |
430 |
2520 |
265 |
1175 |
1100 |
207 |
1427 |
525 |
1050 |
1875 |
550 |
600 |
380 |
2872 |
320 |
1350 |
1300 |
215 |
1423 |
600 |
1150 |
2250 |
650 |
650 |
330 |
2992 |
320 |
1410 |
1300 |
215 |
1678 |
600 |
1150 |
3000 |
650 |
650 |
440 |
3370 |
321 |
1575 |
1500 |
230 |
1862 |
700 |
1350 |
3750 |
800 |
800 |
310 |
3840 |
321 |
1800 |
1600 |
230 |
2317 |
700 |
1350 |
4500 |
800 |
800 |
310 |
3840 |
321 |
1800 |
1600 |
230 |
2456 |
700 |
1350 |
5250 |
800 |
800 |
320 |
4350 |
321 |
2060 |
1800 |
230 |
2400 |
700 |
1350 |
6000 |
800 |
800 |
500 |
4660 |
321 |
2000 |
2000 |
230 |
2450 |
700 |
1650 |
Суточная практическая производительность выбранного смесителя Ппр
оценивается с учетом коэффициента использования его по времени ,
часовой паспортной производительности Пп из выражения:
Ппр = 24 · Пп · .
По рассчитанной величине Ппр (т/сут) делается заключение о том, обеспечивает ли выбранный смеситель выполнение производственной программы линии. В противном случае подбирается другой смеситель.
В пояснительной записке в качестве примера приводится полная смеха расчета и подбора оборудования только для одного вида сырьевых материалов. Результаты расчетов оборудования по другим видам сырья обобщаются в сводную таблицу по форме, приведенной ниже.
Потребное количество оборудования кажого типа рассчитываентся по валовой производительности линии П и требуемого производственной программой объема переработки Мi из выражения ():
()
После расчета и подбора оборудов свести в таблицу 19
Таблица 19
Состав и характеристика основного оборудования технологических линий составного цеха
Наименование технологической линии и состав оборудования |
Назначение оборудования |
Суточный объем переработки, т/сут |
Коэффициент использования во времени |
Количество единиц оборудования, шт. |
Габаритные размеры оборудования, м |
Поточная технологическая линия транспортировки и обработки кварцевого песка |
|||||
Грейферный мостовой кран грузоподъемностью 5 т |
Размещение песка по складскому отсеку и подача на линию обработки |
80 |
0,3 |
1 |
Пролет крана 18 м |
И т. д. |
Вставить конец
Порядок таблиц и рисунков пересмотреть (если что, то исправить в тексте)
Библиограф список1. ОСТ 3-4931-81 Стекло оптическое серии 100. Синтетический состав. М.: Издательство стандартов, 1981. 16 с.
2. ОСТ 3-4375-79 Стекло оптическое цветное. Синтетический состав. М.: Издательство стандартов, 1980. 32 с.
3. Стекло оптическое бесцветное. Физико-химические характеристики ГОСТ 3514-94 М.: Издательство стандартов, 1994. 22 с.
4. Справочник технолога-оптика / М. А. Окатов, Э. А. Антонов и др.; под ред. М. А. Окатова. 2-е изд. СПб: Политехника, 2004. 679 с.
5. Халилев В. Д. Основы технологии оптического стекла: учебное пособие. Л.: ЛТИ, 1989. 100 с.
6. Физико-химические основы производства оптического стекла / Под ред. Л. И. Демкиной. Л.: ЛТИ, 1976. 456 с.