Им Департамент образования и науке
Кемеровской области
Государственное профессиональное
образовательное учреждение
«Мариинский политехнический техникум»
23.02.03Техническое обслуживание и ремонт
автомобильного транспорта.
МДК.01.02 Организация технического обслуживания и
ремонта подъемно-транспортных, строительных,
дорожных машин и оборудования в различных
условиях эксплуатации.
ПРОЕКТ ЗОНЫ ТЕКУЩЕГО РЕМОНТА
В АТП г.МОСКВА
Курсовой проект
пояснительная записка
(КП.020.03.ПЗ)
Исполнитель: студент гр. ТА-17 Шевчук
Олег Константинович
Руководитель: Алябьев С А
Оценка:________
Дата
допуска к защите:________
![]() |
СОДЕРЖАНИЕ
ВВЕДЕНИЕ ……………………………………………...........3
1 ОБЩАЯ ЧАСТЬ ……………………………………………..5
1.1 Обоснование выбора основной марки, модели
автомобиля……...........................................................5
1.2 Краткая техническая характеристика
автомобиля выбранного за основную модель……..6
1.3 Краткая характеристика проектируемого
объекта….. ………………………………………………..6
2. РАСЧЕТНО-ТЕХНОЛОГИЧЕСКАЯ ЧАСТЬ…………………….....................................................7
2.1 Приведение парка к одной модели……………………7
2.2 Корректирование технологических
нормативов………… …………………………………..11
2.2 Корректирование периодичности технических
обслуживаний и капитального ремонта……………11
2.2.2 Корректирование трудоемкости технических
обслуживаний и текущего ремонта…………………14
2.2.3 Корректирование простоя автомобиля в
техническом обслуживании и ремонте…………16
2.3 Расчет производственной программы по
количеству воздействий за год……………………..18
2.3.1 Расчет коэффициента технической
готовности…….. ………….. ……………………….18
2.3.2 Расчет коэффициента использования парка….18
2.3.3 Расчет общепаркового годового пробега……...19
2.3.4 Расчет количества воздействий за год
по парку…………………………………………………19
![]() |
2.3.5 Расчет
суточной программы по количеству
воздействий………………………………………….20
2.4 Расчет годовой трудоемкости работ по
техническому обслуживанию и текущему
ремонту…………………………………………………21
2.5 Расчет годовой программы проектируемого
объекта………………………………………………….23
2.6 Расчет численности производственных
рабочих…………………………………………………..25
2.7 Расчет числа постов…………………………………27
2.8 Распределение рабочих по видам работ и
квалификации………………………………………… 29
2.9 Подбор оборудования и расчет производственной
площади………………………………………………….30
2.10 Технологические возможности проектируемого
объекта…………………………………………………..31
Технологическая карта……………………………………32
3. ОРГАНИЗАЦИОННАЯ ЧАСТЬ………………………….33
3.1 Организация технологического процесса ТО ,
ТР и диагностики в АТП…………………………….....34
3.2 Организация управленияпроизводственными
подразделениямиТО и ТР в АТП…………………...35
3.3 Режим труда и отдыха…………………………………36
ЗАКЛЮЧЕНИЕ………………………………………………..37
ЛИТЕРАТУРА ………………………………………………...31
ВВЕДЕНИЕ
НефАЗ-5299 — российский автобус большого класса производства Нефтекамского автомобильного завода. Выпускается в высокопольном (с 2000 года), частично-низкопольном (с 2004 года), полностью низкопольном (с 2011 года) вариантах городского, пригородного и междугородного автобуса с дизельным и газовым двигателями, а также в виде троллейбуса (с 2008 года) и электробуса (с 2012 года); претерпел три значительных рестайлинга дизайна (в 2005, 2013 и 2018 годах). Является одной из самых массовых моделей городского автобуса в современной России: за 15 лет производства было выпущено более 10000 экземпляро
В начале 1990-х годов Камским автомобильным заводом была выдвинута идея о производстве и продаже автобусов на шасси КамАЗ. В 1993 году в Набережных Челнах на базе автозавода КамАЗ было создано акционерное общество «КамАЗавтобуспром»[2]. Плодом работы данного предприятия стал опытный образец городского автобуса КАМАЗ-5262. Однако планы по выпуску данной модели были перечёркнуты пожаром на заводе двигателей КамАЗа, случившимся 14 апреля 1993 года. Тем не менее КамАЗ не прекращал поиски вариантов производства автобусов на собственном шасси. В мае 1997 года автозавод подписал соглашение о сотрудничестве со Словенской фирмой Avtomontaza[3]. Подписанное соглашение предусматривало создание в Набережных Челнах производственных мощностей по выпуску автобусов КамАЗ-5297. Предполагалось, что первые 100 машин на КамАЗовском шасси будут изготовлены в Словении, а в перспективе кузова собирался делать и сам КамАЗ (Automontaza должна была поставить КамАЗу необходимое оборудование, включая окрасочную линию). В это же время Татарским республиканским фондом НИОКР, администрацией Казани и Набережных Челнов совместно с Госкомимуществом Татарстана создаётся ЗАО «Челнинский Автобусный Завод» (ЧелАЗ). Новый завод разработал, запатентовал и сертифицировал городской 6-ти
дверных автобус ЧелАЗ-5281. В 1999 году Чел АЗ планировал собрать 200 автобусов. Планируемая проектная мощность завода составляла 2000 автобусов в год. На этот объём производства ЧелАЗ должен был выйти к 2000 году. Однако экономический кризис, случившийся в 1998 году, не позволил этим проектам воплотится в жизнь.
Тем не менее, спустя несколько лет, проделанная работа стала основой для реализации нового проекта — выпуск и продажа автобусов НефАЗ-5299 на дочернем предприятии КамАЗа — Нефтекамском автозаводе. Семейством автобусов большого класса инженеры расположенного в Башкортостане Нефтекамского автозавода начали заниматься в августе 2000 года, когда руководством завода была принята "Программа освоения пассажирских автобусов на шасси «КАМАЗ». Предприятие, начавшее свою работу в 1977 году с изготовления самосвалов, к тому времени уже имело опыт производства пассажирского автотранспорта: так называемые «вахтовки» — снабжённые сиденьями остеклённые кузова-фургоны, поставленные на рамы полноприводных грузовиков. А в конце 1990-х годов появился проект по сборке турецких автобусов «Мерседес» серии О325. Но уже тогда пришло понимание, что более перспективно обзавестись собственным семейством автобусов: недорогих, неприхотливых, ремонтопригодных — максимально приспособленных для эксплуатации в специфических российских условиях. В качестве базы для них было выбрано специальное автобусное шасси, разработанное в 1997 году на КамАЗе («КамАЗ-5297»)[4].
Непосредственно к изготовлению опытного образца автобуса «НефАЗ-5299» приступили 9 сентября 2000 года. Первый же автобус с заводским номером 0000001 сошёл с конвейера завода 6 декабря 2000 года и был отправлен в Набережные Челны, где проработал в предприятии «ПАК-Инвест» до 2009 года. В 2001 году было произведено 115 автобусов, которые были поставлены в Уфу, Ишимбай, Стерлитамак, Сибай, Нефтекамск, Кумертау, Белорецк и Октябрьский[6].
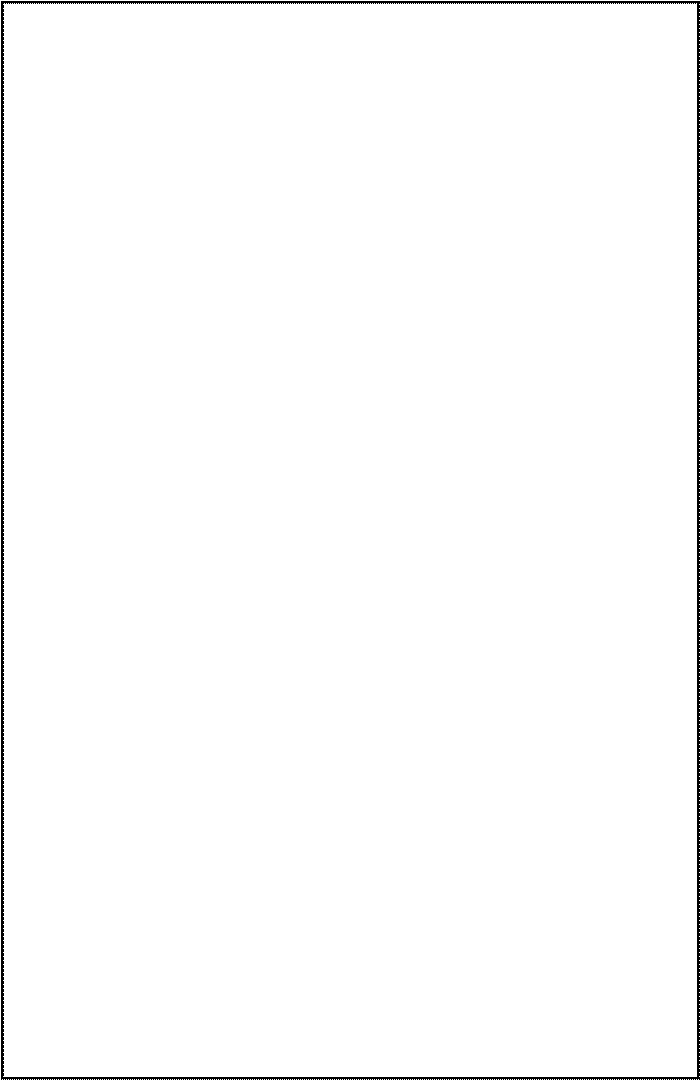
Под маркой НефАЗ-5299 представлено целое семейство автобусов большой вместимости. Существуют городские, пригородные и междугородные модификации данных автобусов, с различным устройством пассажирского салона, высотой пола, типами двигателя, КПП и прочим.
НефАЗ-5299-10 в Кемерове
Исторически первая модель завода, серийное производство которой было начато в 2000 году. Представляет собой классический заднемоторный, высокопольный городской автобус с каркасным цельнометаллическим кузовом и тремя дверьми. Конструкторы завода не пошли на поводу у доминировавшей в то время тенденции ради упрощения конструкции делать заднюю дверь зауженной, а то и вовсе одностворчатой — все дверные проемы получили одинаковую ширину 1200 мм. В моторный отсек НефАЗ-5299 был установлен КамАЗовский дизельный двигатель с КамАЗовской коробкой передач. Большая часть внешнего облика первых автобусов была аналогична автобусам МАЗ-104. С 2004 года выпускаются автобусы с обновлённым дизайном.
Базовая городская полунизкопольная модель завода, выпускающаяся с 2007 года. В автобус устанавливаются двигатели КАМАЗ или Cummins, а с 2010 года выпускаются газомоторные автобусы, работающие на метане. Устанавливаются АКПП Voith Diwa.
Автобусы оборудованы вместительным салоном с тремя двустворчатыми боковыми пассажирскими дверями. В салоне 115 мест для пассажиров, 25 из которых для сидения, возможно размещение инвалидной коляски, а средний дверной проём оборудуется пандусом. В салоне имеются три потолочных люка с электроприводом и пять форточек, оборудованы две накопительные площадки в средней и задней частях салона. Кабина водителя отделена от салона перегородкой с форточкой, по заказу в ней устанавливается дверь.
С 2010 года также выпускаются автобусы с обновлённым салоном от Набережночелнинской фирмы «КОРА», аналогичными автобусам ЛиАЗ-5292; передняя дверь полностью отводится в салон. Базовый дизайн внешнего вида был незначительно изменен в 2012 году (линия окон), а более серьёзный рестайлинг проведён в 2013 году (передняя и задняя маски, салон) и в 2018 году (полностью изменён внешний вид кузова).
Полностью низкопольный городской автобус: вход во все три двери автобуса — без ступеней. Средняя дверь сдвинутая назад по сравнению с базовой моделью. Впервые автобус был представлен на Московской Международной выставке «Комтранс-2011»[7]. Модификация рассчитана на перевозку 96 пассажиров и оборудован 24 местами для сидения. В модели предусмотрены: выдвижная рель аппав проёме средней двери, площадка для инвалидной коляски с опорной панелью и 4 мягких сиденья для инвалидов. Автобус оснащён системой ECAS (электронное управление пневмоподвеской), навигационной системой а также устройством контроля режима труда и отдыха водителя. В салоне автобуса и кабине водителя установлены кондиционеры. С 2011 года автобусы НефАЗ-52994 поставляются в Санкт-Петербург.
энергоемкостью 313,6
кВт·ч
Исторически первая модель завода, серийное производство которой было начато
в 2000
году.
Представляет собой классический заднемоторный, высокопольный городской автобус
с каркасным цельнометаллическим кузовом и тремя дверьми. Конструкторы завода не
пошли на поводу у доминировавшей в то время тенденции ради упрощения
конструкции делать заднюю дверь зауженной, а то и вовсе одностворчатой —
все дверные проемы получили одинаковую ширину 1200 мм. В моторный отсек
НефАЗ-5299 был установлен КамАЗовский дизельный двигатель с КамАЗовской коробкой передач. Большая часть внешнего облика первых автобусов была аналогична
автобусам МАЗ-104. С 2004 года выпускаются
автобусы с обновлённым дизайном.
Базовая городская полунизкопольная модель завода, выпускающаяся с 2007 года. В автобус устанавливаются двигатели КАМАЗ или Cummins, а с 2010 года выпускаются газомоторные автобусы, работающие на метане. Устанавливаются АКПП Voith Diwa.
Автобусы оборудованы вместительным салоном с тремя двустворчатыми боковыми пассажирскими дверями. В салоне 115 мест для пассажиров, 25 из которых для сидения, возможно размещение инвалидной коляски, а средний дверной проём оборудуется пандусом. В салоне имеются три потолочных люка с электроприводом и пять форточек, оборудованы две накопительные площадки в средней и задней частях салона. Кабина водителя отделена от салона перегородкой с форточкой, по заказу в ней устанавливается дверь.
С 2010 года также выпускаются автобусы с обновлённым салоном от Набережночелнинской фирмы «КОРА», аналогичными автобусам ЛиАЗ-5292; передняя дверь полностью отводится в салон. Базовый дизайн внешнего вида был незначительно изменен в 2012 году (линия окон), а более серьёзный рестайлинг проведён в 2013 году (передняя и задняя маски, салон) и в 2018 году (полностью изменён внешний вид кузова).
Полностью низкопольный городской автобус: вход во все три двери автобуса — без ступеней. Средняя дверь сдвинутая назад по сравнению с базовой моделью. Впервые автобус был представлен на Московской Международной выставке «Комтранс-2011»[7]. Модификация рассчитана на перевозку 96 пассажиров и оборудован 24 местами для сидения. В модели предусмотрены: выдвижная рель аппав проёме средней двери, площадка для инвалидной коляски с опорной панелью и 4 мягких сиденья для инвалидов. Автобус оснащён системой ECAS (электронное управление пневмоподвеской), навигационной системой а также устройством контроля режима труда и отдыха водителя. В салоне автобуса и кабине водителя установлены кондиционеры. С 2011года автобусы НефАЗ-52994 поставляются в Санкт-Петербург.
1 ОБЩАЯ ЧАСТЬ
1.1 Обоснование выбора основной
марки, модели автомобиля
За основную марку выбирется автомобиль Нефаз-5299 на основании следующего:
- автобус Нефаз-5299 является более современной моделью по сравнению с остальными марками;
- автобусы марк ЛИАЗ 429260, указанные в задании, находятся в одной технологически совместимой группе с автомобилем ГАЗ-3307, что позволяет использование одних и тех же постов и оборудование для технического обслуживания и текущего ремонта;
- автобус НЕФАЗ5299 является базовым автобусом.
1.2 Краткая техническая
характеристика автомобиля
Грузоподъемность, кг. …………………………………………………………..4000
Полная масса,кг…………………………………………………………………..7400
Габариты, мм. ……………………………………………………6395*2380*2220
Радиус поворота, мм.
по оси внешнего переднего колеса ……………………………………………8
наружн. габаритный…………………………………………………………..9
Максимальная скорость, км/ч ……………………………………………………70
База,мм …………………………………………………………………………..3700
Колея передних колес, мм……………………………………………………….1630
Колея задних колес, мм………………………………………………………….1690
Дорожный просвет, мм. ………………………………………….. ……...347/265
Двигатель (марка, вид применяемого топлива,
расположение
цилиндров, число цилиндров, расположение клапанов)……………ЗМЗ-53,карб.,
4-такт., 8-цил., V- образн., верхнеклап.
Марка топлива……………………………………………………………………….А-80
Контрольный расход топлива, л/100 км. …………………………… …………..24
Колесная формула ……………………………………………………………….4 * 2.
1.3Краткая характеристика
проектируемого объекта
Электротехнический цех предназначен для проверки и ремонта приборов электрооборудования подвижного состава. Помимо приборов и стендов, в цехе устанавливают прибор для проверки обмоток генераторов и стартеров, станок для обточки и фрезерования коллекторов якоркй, выпрямитель и др.
Электротехнический, аккумуляторный, карбюраторный цехи (а также цех топливной аппаратуры в парках с дизельными автомобилями) специфичны тем, что обслуживают как зонуТР, так и зоны ТО-2 и ТО-1, в связи с чем и располагаться в здании они могут в самых различных местах. Но здесь все же можно указать на два основных варианта их расположения. По первому из них все эти цехи располагаются в смежных с зоной ТО-1 помещениях или в отдельном здании поточного профилактория при павильонной застройке. По второму варианту указанные цехи располагаются вблизи от постов зоны ТР, специализирующихся на ремонте двигателей, или входят в состав специализированной зоны ТО-2 и ТР двигателей. В последнем случае в зоне ТО-1 размещаются только шкафы и верстаки с необходимыми приспособлениями, инструментом, узлами и деталями для электриков и карбюраторщиков. Для аккумуляторных работ, кроме необходимых инструментов и приспособлений, предусматриваются запас дистиллированной воды, обменный фонд аккумуляторных батарей для быстрой замены их на автомобиле при необходимости и тележка для транспортировки аккумуляторов. Все это позволяет ослабить технологическое тяготение зоны ТО-1 к описываемым цехам.
2
РАСЧЕТНО-ТЕХНОЛОГИЧЕСКАЯ
ЧАСТЬ
2.1 Приведение паркак одной модели.
Приведение парка к одной модели производим по удельной трудоемкости текущего ремонта, через коэффициент приведения:
Кп = tптр / tотр; (1)
где tптр -расчетная удельная трудоемкость текущего ремонта
приводимой модели, чел- час;
tотр - расчетная удельная трудоемкость текущего ремонта
основной модели, чел.-час;
Расчетная удельная трудоемкость текущего ремота определяется по формуле:
tтр = tнтр*К1*К2*К3*К4* К5,чел.-час;(2)
где tнтр – нормативная удельная трудоемкость текущего ремонта,
чел.-час/1000км, (см.табл. 1.2,[2]);
К1 - коэффициент корректирования нормативов в зависимости от
условий эксплуатации,(см.табл. 1.3,[2]);
К2 - коэффициент корректирования нормативов в зависимости от
модификации подвижного состава и организации его работы,
(см.табл. 1.4,[2]);
К3 – коэффициент корректирования нормативов в зависимости от
природно-климатических условий,(см.табл. 1.9 и табл.1.5,[2]);
К4 – расчетный коэффициент корректирования нормативов удельной
трудоемкости текущего ремонта в зависимости от пробега
с началаэксплуатации.
К5 – коэффициент корректирования нормативовтрудоемкости
технического обслуживания и текущего ремонта в зависимости от
количества обслуживаемых и ремонтируемых автомобилей
на атотранспортном предприятии и количества технологически
совместимых групп подвижного состава,(принимается по табл.
1.8 и табл. 1.7,[2]).
Расчетный коэффициент корректирования нормативов удельной трудоемкости текущего ремонта в зависимости от пробега с начала
эксплуатацииопределяется по формуле:
К4 = А1 * К14 + А2 * К24 + ..... + Аn * Кn4 / Аи,(3)
где А1, А2, Аn – число автомобилей разной возрастной категории,
принимается из задания;
К14, К24, Кn4 - коэффициент корректирования нормативов удельной
трудоемкости текущего ремонта в зависимости от
пробега с начала эксплуатации, соответствующий
своей возрастной категории,(принимается по табл.
1.6[2]).
Аи - инвентаризационное (списочное) число автомобилей определенной
марки, модели, принимается из задания.
Расчет производится в таблице 1.
Таблица 1 Расчет коэффициента К4
Марка, модель |
Списочное количество |
Пробег с начала эксплуатации в долях от нормативного пробега до капитального ремонта (Lкр) |
Результирующий |
||||||||
до 0,5 |
К14 |
0,5-0,75 |
К24 |
0,75-1 |
К34 |
Свыше 1 |
К44 |
К4 |
|||
ЛИАЗ 429260 |
7 |
5 |
0,8 |
0 |
1,0 |
1 |
1,3 |
1 |
0,4 |
0,9 |
|
ГОЛАЗ 52911 |
31 |
13 |
0,8 |
11 |
1,0 |
5 |
1,3 |
7 |
1,2 |
||
НЕФАЗ 35299 |
15 |
0 |
0,8 |
1 |
1,0 |
7 |
1,3 |
7 |
1,4 |
1,3 |
|
Итого |
53 |
18 |
12 |
13 |
10 |
3,4 |
|||||
Число приведенных автомобилей (Апр) определяется по формуле:
Апр = Аи * Кп,шт.(4)
где Аи– инвентаризационное (списочное) количество приводимых
автомобилей определенной марки, модели, принимается из
задания;
Кп - коэффициент приведения, формула 1,ПЗ.
Расчеты по приведению парка к одной модели производятся в таблице 2.
Таблица 2Приведение парка к одной модели
Марка, модель |
tнтр |
Коэффициенты корректирования |
Количество |
|||||||
К1 |
К2 |
К3 |
К4 |
К5 |
tтр |
Кп |
Списоч-е |
Привед-е |
||
ЛИАЗ 429260 |
6,9 |
1,1 |
1,0 |
1,0 |
0,9 |
1,15 |
7,8 |
0,63 |
7 |
4 |
ГОЛАЗ 352911 |
7,5 |
1,1 |
1,0 |
1,0 |
1,2 |
1,15 |
11,3 |
0,92 |
31 |
28 |
НЕФАЗ 5299 |
7,5 |
1,1 |
1,0 |
1,0 |
1,3 |
1,15 |
12,3 |
1 |
15 |
15 |
Итого |
47 |
Принимается к расчету 47 автобусов ЛИАЗ 429260
2
РАСЧЕТНО-ТЕХНОЛОГИЧЕСКАЯ
ЧАСТЬ
2.1 Приведение парка к одной модели.
При выполнении расчетов по ТО и диагностике автомобилей коэффициент приведения (Кпр) определяется для соответствующего вида ТО и диагностики из выражения:
Кп = t2п * L2о/ t2о * L2 ,п(1)
гдеt2п–расчетная трудоемкость приводимой модели, чел.-час,
t2о – расчетная трудоемкость основной модели, чел.-час,
L2о – расчетная периодичность ТО-2 основной модели, км,
L2пр – расчетная периодичность ТО-2 приводимой модели,км.
Расчет трудоемкости ТО-2
t2= tн2 * К2 * К5, чел-час,(2)
где tн2– нормативная трудоемкость ежедневного обслуживания,
чел-час (см.табл. 1.3,[2]);
К2 - коэффициент корректирования нормативов в зависимости
от модификации ПС и организации его работы (см.табл. 1.4,[2]);
К5 – коэффициент корректирования нормативов в зависимости от
количества обслуживаемых и ремонтируемых автомобилей на
АТП и количества технологически совместимых групп подвижного
состава (принимается по табл. 1.8 и табл. 1.7,[2]).
![]() |
Расчет периодичности ТО-2
L2= Lн1 * К1 * К3, км,(3)
гдеLн2- нормативная периодичность ТО-2, км. (см. табл. 1.1 ,[2]);
К1– коэффициент корректирования нормативов в зависимости от
условий эксплуатации (см.табл. 1.3,[2]);
К3 – коэффициент корректирования нормативов в зависимости от
природно-климатических условий,(см.табл. 1.9 и табл.1.5,[2]);
Число приведенных автомобилей (Апр) определяется по формуле:
Апр = Аи * Кп, шт,(4)
где Аи– инвентаризационное (списочное) количество приводимых
автомобилей определенной марки, модели (принимается из
задания);
Кп - коэффициент приведения (см. формула ,1 ПЗ).
Расчеты по приведению парка к одной модели производятся в таблице 1.
Таблица 1Приведение парка к одной модели
Марка, Модель |
tн2
|
Коэффициенты корректирования |
t2 |
Lн2 |
Коэффициенты корректирования |
L2 |
Кп |
Количество |
|||
К2 |
К5 |
K1 |
К3 |
Аи |
Апр |
||||||
3,76 |
1,0 |
1,15 |
43,24 |
1400 |
0,9 |
1,0 |
12600 |
1,0 |
7 |
7 |
|
7,8 |
1,0 |
1,15 |
43,24 |
14000 |
0,9 |
1,0 |
12600 |
1 |
31 |
31 |
|
25,8 |
1,0 |
1,15 |
296 |
14000 |
0,9 |
1,0 |
12600 |
1,4 |
15 |
21 |
|
Итого |
53 |
59 |
Принимается к расчету 2 1АВТОБУСОВ ЛИАЗ 429260
2.2 Корректирование
технологических нормативов
2.2.1 Корректирование периодичности ТО и пробега до капитального ремонта.
Периодичность ТО-1.
L1= Lн1 * К1 * К3, км,(5)
гдеLн1- нормативная периодичность ТО-1, км. (см. табл. 1.1,[2]);
К1– коэффициент корректирования нормативов в зависимости от
условий эксплуатации (см.табл. 1.3,[2]);
К3 – коэффициент корректирования нормативов в зависимости от
природно-климатических условий (см.табл. 1.9 и табл.1.5,[2]);
L1=3000*0,9*0,9=2430 км.
Периодичность ТО-2.
L2= Lн2 * К1 * К3, км,(6)
гдеLн2- нормативная периодичность ТО-2, км. (см. табл. 1.1 [2]);
L2=14000 *1,1 *1,0.=15400
Пробег до капитального ремонта.
Lкр = Lнкр * К1 * К2 * К3 * К4, км,(7)
где Lнкр – нормативный пробег до капитального ремонта, км;
(см. табл. 1.2 [2]);
К1 - коэффициент
корректирования нормативов в зависимости от
условий эксплуатации (см.табл. 1.3 [2]);
К2 - коэффициент корректирования нормативов в зависимости
модификации ПС и организации его работы (см. табл. 1.4[2]);
К3 – коэффициент
корректирования нормативов в зависимости от
природно-климатических условий (см.табл. 1.9 и табл.1.5[2]);
К4 – расчетный коэффициент корректирования нормативов удельной
трудоемкости текущего ремонта в зависимости от пробега с
начала эксплуатации.
Расчетный коэффициент корректирования нормативов удельной трудоемкости текущего ремонта в зависимости от пробега с начала
эксплуатации определяется по формуле:
К4 = (Ан * Кн4 + Аст * Кст4 ) / Аи,(8)
где Ан – число «новых» автомобилей от списочного количества (новыми
считаютя автомобили не прошедшие капитальный ремонт, т.е до 1
Lкр- принимается из задания);
Аст – число «старых» автомобилей от списочного количества
(старымисчитаютя автомобили прошедшие капитальный ремонт,
т.е свыше 1Lкр -принимается из задания);
Кн4- коэффициент корректирования нормативов в зависимости от
пробега с начала эксплуатации, соответствующий «новым»
автомобилям (принимается – 1,0 [2]);
Кст4- коэффициент корректирования нормативов в зависимости
от пробега с начала эксплуатации, соответствующий «старым»
автомобилям ( принимается – 0,8[2]);
Аи - инвентаризационное (списочное) число автомобилей
парка (принимается из задания);
К4 =43*1+10*0,8=0,96
тогда Lкр=250000*0,9*1,00*0,98*0,8=176400 км.
Корректирование периодичности по среднесуточному
пробегу.
Для корректирования нормативов периодичности ТО и пробега до капитального ремонта по среднесуточному пробегу, должна бытьсохранена кратность расчетных величин периодичности ТО-1, ТО-2 и Lкр, которая определяется по формулам:
КратностьL1: n1 = L1 / lcc ,(9)
где L1 – периодичность ТО-1 ( см. формула 5, ПЗ);
lcc– среднесуточный пробег ( принимается из задания).
n1 =3500172=20
КратностьL2:n2 = L2 / L1, (10)
где L2 – периодичность ТО-2 ( см. формула 6, ПЗ);
L1 – периодичность ТО-1 (см. формула 5, ПЗ);
n2 = 154003465=4
КратностьLкр:nкр = Lкр / L2, (11)
где Lкр – пробег до КР (см. формула 7, ПЗ);
L2 – периодичность ТО-2 (см. формула 6, ПЗ).
nкр =32832015400=21
Полученное значение кратности округляется до целого числа. Отклонение при округлениях не должно превышать ± 10%.
Корректирование периодичности по среднесуточному пробегу производится в таблице 2.
Таблица 2 Корректирование периодичности
по среднесуточному пробегу
Вид пробега |
Обозначение |
Нормативное значение |
Откорр-е значение |
Пробег до предшетсву- ющего вида воздействия умножить на кратность |
Принято к расчету |
Среднесут. пробег, км |
lсс |
172 |
|||
До ТО-1, км |
L1 |
3500 |
3465 |
172*20 |
3440 |
До ТО-2, км |
L2 |
14000 |
15400 |
3440*4 |
13760 |
До капитального ремонта, км. |
Lкр |
38000 |
328320 |
13760*21 |
288960 |
![]() |
2.2.2 Корректирование трудоемкости технических воздействий.
Трудоемкость ежедневного обслуживания:
tео = tнео * К2 * К5, чел-час, (12)
где tнео– нормативная трудоемкость ежедневного обслуживания,
чел-час (см. табл. 1.2 [2]);
К2 - коэффициент корректирования нормативов в зависимости
от модификации ПС и организации его работы (см.табл. 1.4[2]);
К5 – коэффициент корректирования нормативов в зависимости от
количества обслуживаемых и ремонтируемых автомобилей на
АТП и количества технологически совместимых групп подвижного
состава (принимается по табл. 1.8 и табл. 1.7[2]).
tео =0,95*1,00*1,15=1,1, чел-час,
Трудоемкость ТО- 1:
t1 = tн1 * К2
* К5, чел-час, (13)
где tн1 – нормативная трудоемкость ТО-1, чел-час (см. табл. 1.2 [2]);
t1= 6,6*1,00*1,15=77,6чел-час.
Трудоемкость ТО- 2 :
t2 = tн2 * К2 * К5, чел-час, (14)
где tн2 – нормативная трудоемкость ТО-2, чел-час (см. табл. 1.2 [2]);
t2 = 25,8*1,00*1,15=29,6-час.
Трудоемкость сезонного обслуживания :
tсо = Кзоны * t2, (15)
где Кзоны – коэффициент климатической зоны (см. п.2.11.2. [1]);
t2 – расчетная трудоемкость ТО-2 (см. формула 14, ПЗ).
tсо = 29/100 * 29,6=6чел-час.
Трудоемкость текущего ремонта (ТР) :
tтр=tнтр*К1*К2*К3*К4*К5,чел.-час, (16)
где tнтр – нормативная трудоемкость текущего ремонта,
чел.-час/1000км, (см. табл. 1.2,[2]);
К1 - коэффициент корректирования нормативов в зависимости от
условий эксплуатации (см.табл. 1.3,[2]);
К2 - коэффициент корректирования нормативов в зависимости от
модификации ПС и организации его работы (см. табл. 1.4,[2]);
К3 – коэффициент корректирования нормативов в зависимости от
природно-климатических условий (см.табл. 1.9 и табл. 1.5,[2]);
К4 – расчетный коэффициент корректирования нормативов удельной
трудоемкости в зависимости от пробега с начала эксплуатации.
К5 – коэффициент корректирования нормативов в зависимости от
количества обслуживаемых и ремонтируемых автомобилей на
АТП и количества технологически совместимых групп
подвижного состава (принимается по табл. 1.8 и табл. 1.7[2]).
![]() |
Расчетный коэффициент корректирования нормативов в зависимости
от пробега с начала эксплуатации определяется по формуле:
К4 = А1 * К14 + А24 * К34 + ... + Аn * Кn4 / Аи,(17)
где А1, А2, Аn – число автомобилей от списочного количества разной
возрастной категории (принимается из задания);
К14, К24, Кn4- коэффициент корректирования нормативов
удельной трудоемкости в зависимости от пробега с начала
эксплуатации,соответствующий своей возрастной категории (см.
табл. 1.6[2]);
Аи - инвентаризационное (списочное) количество автомобилей
(принимается из задания);
К4=18*0,8117*1,0+13*1,3+10*14153=1,0
тогда tтр = 3,7*1,1*1,00*1,2*0,99=4,6чел.-час.
2.2.3 Корректирование простоя автомобиля в ТО, ТР и капитальном
ремонте.
Простой автомобиля в ТО и ТР.
d = dн * КI4 ,дней/1000 км, (18)
где dн – нормативный простой в ТО и ремонте (см.табл. 1.10[2]);
КI4 – коэффициент корректирования нормативов удельной
трудоемкостипродолжительности простоя в ТО и ремонте в
зависимости от пробега с начала эксплуатации (см. табл. 1.6. [2]).
К/4=(А1*К/14+А2*К/24+..+Аn*К/n4)/Аи, (19)
где А1, А2, Аn – число автомобилей разной возрастной категории
(принимается из задания);
![]() |
К /14, К/24, К/n4 - коэффициент корректирования нормативов
удельной трудоемкости текущего ремонта в зависимости от пробега с
началаэксплуатации, соответствующий своей возрастной категории
(см.табл. 1.6[2]);
Аи - инвентаризационное (списочное) число автомобилей определенной
марки, модели (принимается из задания);
К/4=18*0,7+12*0,7+13*1,0+10*1,353=0,88
тогда d =0,50дней1000 0,50*0,88=0,44 км.
Простойавтомобиля в капитальном ремонте.
Дкр = Днкр + Ддост, дней,(20)
где Днкр – нормативный простой в капитальном ремонте
(см.табл. 1.10[2]);
Ддост – число дней транспортирови автомобилей на АРЗ и
обратно ( принимается из задания).
Дкр =20+6=26дней
Корректирование технологических нормативов сводится в таблицу 3.
Таблица 3 Корректирование технологических
нормативов
Обозначения |
L1 |
L2 |
Lкр |
tео |
t1 |
t2 |
tсо |
tтр |
d |
Дкр |
Норматив- ноезначение |
3500 |
1400 |
380000 |
0,95 |
6,6 |
25,8 |
20% |
6,9 |
0,50 |
20 |
Откоррек- тированное значение |
3440 |
13760 |
288960 |
1,0 |
7,6 |
29,6 |
6,0 |
12,8 |
0,44 |
26 |
2.3 Расчет производственной
программы по количеству
воздействий за год.
2.3.1 Расчет коэффициента технической готовности.
Коэффициент технической готовности показывает, какая часть автомобилей находится в технически исправном состоянии.
Коэффициент технической готовности (aТ) расчитывается по формуле:
aТ = 1 / (1 + Lcc ( d / 1000 + Дкр / Lкр)), (21)
где Lcc– среднесуточный пробег автомобиля ( принимается из задания);
d – простой автомобиля в ТО и ТР (см. табл. 4, ПЗ );
Дкр - простой автомобиля в капитальном ремонте (см. табл. 3, ПЗ);
Lкр - пробег автомобиля до капитального ремонта, км. (см. табл. 3, ПЗ).
aТ= 1/ 1+ 172(0,441000+26288960) = 0,93
![]() |
2.3.2 Расчет коэффициента использования парка.
Коэффициент использования парка показывает какая часть технически исправных автомобилей находится на линии.
Коэффициент использования парка расчитывается по формуле:
aи = Др.г / Ди * aТ * Ки, (22)
где Др.г - число дней эксплуатации автомобилей в году
(принимается из задания);
Ди – число календарных дней в году;
aТ - коэффициент технической готовности (см. формула 21, ПЗ);
Ки – коэффициент, учитывающий снижение использования
технически исправных автомобилей в рабочие для АТП дни по
эксплуатационным причинам, т. е. нет работы (при отсутстви
данных по конкретному парку Ки можно принять в пределах
0,93 – 0,97).
aи = (365366)*0,93*0,94=0,87
2.3.3 Расчет общепаркового годового пробега.
Годовой пробег автомобилей (L), км. определяется по формуле:
L = Ди * Апр * Lсс * aи, км, (23)
где Ди – число календарных дней в году;
Апр– приведенное количество автомобилей (см. табл. 1, ПЗ);
Lcc– среднесуточный пробег автомобиля ( принимается из задания);
aи - коэффициент использования парка ( см. формула 22).
L =
366*47*172*0,87=2574107км.
2.3.4 Расчет количества воздействий за год по парку.
Расчет числа капитальных ремонов производится по формуле:
Nкр = L / Lкр,(24)
где L– общепарковый годовой пробег, км (см. формула 23,ПЗ);
Lкр - пробег автомобиля до капитального ремонта, км(см. табл.3, ПЗ).
Nкр =2574107288960=9
Расчет числа ТО-2 производится по формуле:
N2 = L / L2 – Nкр, (25)
где L2 – периодичность ТО-2, км (см. табл. 3, ПЗ),
Nкр – число капитальных ремонтов (см. формула 24, ПЗ).
N2 =25741071376013760-11=176
Расчет числа ТО-1 производится по формуле:
N1 = L / L1 – N2 - Nкр, (26)
где L1 – периодичность ТО-1, км (см. табл. 3, ПЗ).
N2 – количество ТО-2 (см. формула 25, ПЗ);
N1 =25741073440-22411=513
Расчет числа ЕО производится по формуле:
Nео = L / Lсс ,(27)
где L– общепарковый годовой пробег, км ( см. формула 23, ПЗ);
Lcc– среднесуточный пробег автомобиля ( принимается из задания).
Nео =2574107172=14965
Расчет числа моек производится по формуле:
Nм = L / (Lсс * n), (28)
где Lcc– среднесуточный пробег автомобиля ( принимается из задания);
n– периодичность мойки в днях ( принимается 3 – 4 - 5).
Nм =2574107/(172*4)=3741
2.3.5 Расчет суточной программы по количеству воздействий.
Расчет суточного числа ТО-1 производится по формуле:
N1с = N1 / Дргз, (29)
где N1 – количество ТО-1 (см. формула 26, ПЗ);
Дргз – число дней работы зоны ТО-1 в году (см. табл. 1.11[2]).
N1с =704305=2
Расчет суточного числа ТО-2 производится по формуле:
N2с = N2 / Дргз, (30)
где N2 – количество ТО-2 (см.
формула 25, ПЗ);
Дргз – число дней работы зоны ТО-2 в году (см. табл. 1.11 [2]).
N2с =224305=1
Расчет суточного числа ЕО производится по формуле:
Nео.с = Nео / Дргз, (31)
где Nео – количество ЕО (см. формула 27, ПЗ);
Дргз – число дней работы зоны ЕО в году (см. табл. 1.11 [2]).
Nео.с =8787305=29
2.4. Расчет годовой трудоемкости
работ по ТО и ТР.
Расчет годовой трудоемкости ЕО производится по формуле:
Тео = Nео * tео, чел-час, (32)
где Nео -количество ЕО (см. формула 27);
tео – удельная трудоемкость ежедневного ослуживания (см. табл. 3, ПЗ).
Тео =8787*1,09=9577,83чел-час.
Расчет годовой трудоемкости ТО-1 производится по формуле:
Т1 = N1 * t1, чел-час, (33)
где N1-количество ТО-1 (см. формула 26);
t1 – удельная трудоемкость ТО-1 (см. табл. 3, ПЗ).
Т1 =704*7,6=5350,4чел-час.
При расчете годовой трудоемкости ТО-1 и ТО-2, необходимо
учитывать дополнительную трудоемкость сопутствующего ремонта (СР), объем которого не должен превышать 20% трудоемкости
соответствующего вида ТО (подраздел 2.33 {1}), поэтому с учетом сопутствующего ремонта трудоемкость ТО-1 будет составлять:
Т1(ср) = Т1* 1,20, чел-час, (34)
тогдаТ1(ср) =5350,4*1,20=6,420,4чел-час.
Расчет годовой трудоемкости ТО-2 производится по формуле:
Т2 = N2 * t2, чел-час, (35)
где N2 -количество ТО-2 (см. формула 25, ПЗ);
t2 – трудоемкость ТО-2 (см. табл. 3, ПЗ).
Т2 =224*29,6=6630,4чел-час.
С учетом сопутствующего ремонта:
Т2(ср) = Т2 * 1,20, чел-час, (36)
Т2(ср) =6630,4*1,20=7956,48чел-час
Расчет годовой трудоемкости сезонного ослуживания производится по формуле:
Тсо = tсо * 2 * Апр, чел-час, (37)
где tсо – трудоемкость сезонного обслуживания (см. табл. 3, ПЗ);
Апр– приведенное количество автомобилей, (см табл 2, ПЗ).
Тсо =6,0*59=354чел-час.
Расчет годовой трудоемкости ТР производится по формуле:
Ттр = L * tтр /1000, чел-час, (38)
где L– общепарковый годовой пробег, км (см. формула 23, ПЗ);
tтр – трудоемкость ТР (см. табл.3, ПЗ).
Ттр =2574107*12*81000=32948,5чел-час.
Расчет производственной программы по количеству воздействий за год сводится в таблицу 4.
Таблица 5. Расчет годовой производственной
программы
aТ |
aи |
L |
Тео |
Т1(ср) |
Т2(ср) |
Тсо |
Ттр |
0,93 |
0,87 |
3231326 |
9577,83 |
6420,48 |
7956,48 |
354 |
32948,5 |
2.5 Расчет годовой прораммы
проектируемого объекта.
Расчет годовой трудоемкости работ для зоны ТР, ремонтным цехам, участкам и отделениям производится по формуле:
Тц = Ттр* Стр / 100, чел-час, (39)
где Ттр – годовая трудоемкость работ ТР (см.табл 5, ПЗ),
Стр – доля постовых или цеховых работ в % от общего объема
работ по ТР (см. табл. 1.13[1]).
Тц = 32948,5*30100=9884,5 чел-час.
2.6 Расчет числа рабочих мест
и распределение трудоемкости
по видам работ
Технологически необходимое число рабочих определяется
по формуле:
Рт = Тц / Фрм,чел, (40)
где Тц- годовая программа проектируемого объекта (см. формула 38, ПЗ);
Фрм – годовой производственный фонд времени рабочего места
при односменной работе,ч.
Годовой производственный фонд времени рабочего места Фрм, определяется с учетом календаря на данный год, при учете режима работы пректируемого объекта:
Фрм = Тсм* (Ди – Дв – Дп), ч., (41)
где Тсм– продолжительность рабочей смены, ч. ( 8 ч. при 5 –
дневной
рабочей неделе, 7 ч. при 6 – дневной);
Ди– число календарных дней в году;
Дв- число выходных дней в году;
Дп - число праздничных дней в году;
Фрм=8*(366-104-14)= 1984ч;
тогда:Рт =9884,5/1984 =74,9чел.
2.7. Расчет числа постов
Птр =Ттр* Ки /( Дргз * С * Тсм* Рср * hп), (42)
где Ттр- годовой объем работ вида воздействия (см. табл. 5, ПЗ);
Ки – коэффициент неравномерности загрузки постов
(см. птабл.1.14{1});
Дргз – число дней работы зоны в году (принимается из задания);
С – число смен работы в сутки (см. табл. 1.11{1});
Тсм – продолжительность смены (см. табл. 1.11{1});
Рср – среднее число рабочих на одном посту (см. табл. 1.15{1});
hп – коэффициент использования рабочего времени поста
(см. табл. 1.16{1});
При расчете числа постов следует учитывать следующее – расчитанное число постов должно быть целым числом, а число рабочих постов зоны ТР приведет не только к увеличению производственных площадей, но и к увеличению количества одноименного оборудования , оснастки и т. д.
Поэтому оперируя числом смен (С), продолжительностью смены (Тсм) и средним числом исполнителей на одном посту (Рср), можно принять оптимальное число постов для соответствующей зоны ТР.
Птр =9884,51,15/(305*1*8*1,5*0,92)=1,7
Принимается три поста.
Распределение рабочих по видам работ производится в таблице 6.
Таблица 6.
Распределение рабочих по видам
работ и квалификации
Виды работ |
Марка, модель |
Твида |
Фрм |
Рт расч. |
Рт принят. |
Разряд |
Нефаз 5299 |
||||||
Работы, выполняемые на постах зоны текущего ремонта |
||||||
Диагностические |
2,0 |
658,98 |
1984 |
0,33 |
||
Регулировочные |
2,0 |
658,98 |
1984 |
0,33 |
||
Разборочно-сборочные |
26,0 |
85661 |
1984 |
1320,25 |
||
Сварочно-жестяницкие |
6,0 |
197691 |
1984 |
99,64 |
||
Малярные |
8,0 |
263584 |
1984 |
132,8 |
||
Итого |
44,0 |
1449 |
1984 |
0,73 |
||
Всего |
||||||
Работы выполняемые в цехах (и частично на постох) |
||||||
Ремонт агрегатов и узлов в том числе: |
20,0 |
7186,8 |
1992 |
3,6 |
4 |
|
по ремонту двигателя |
7,0 |
2515,4 |
1992 |
1,3 |
2 |
|
по ремонту сцепления, карданной передачи, стояночной тормозной системы, редуктора, подъемного механизма |
7,0 |
2515,4 |
1992 |
1,3 |
2 |
|
по ремонту рулевого управления, переднего и заднего мостов, тормозной системы |
6,0 |
2156,0 |
1992 |
1,0 |
||
Слесарно-механические |
11,3 |
1992 |
||||
Электротехнические |
5,0 |
1992 |
||||
Аккумуляторные |
1,3 |
1992 |
||||
По системе питания |
3,5 |
1992 |
||||
Шиномонтажные |
0,5 |
1992 |
||||
Вулканизационные |
1,5 |
1992 |
||||
Кузнечно-рессорные |
2,2 |
1992 |
||||
Медницкие |
2,3 |
1992 |
||||
Сварочные |
1,0 |
1992 |
||||
Жестяницкие |
1,0 |
1992 |
||||
Арматурные |
1,2 |
1992 |
||||
Деревообрабатывающие |
2,7 |
1992 |
||||
Обойные |
1,5 |
1992 |
||||
Итого |
55,0 |
1992 |
||||
Всего: |
100 |
35934,0 |
1992 |
Согласнотарифно-квалификационного справочника (см. приложение 9, табл. 4 {1}),принимется два рабочих 4 разряда, с совмещением работ по ремонту системы питания.
2.7 Подбор
оборудования ирасчет
производственной площади
Подбор технологического оборудования и организационной оснастки производится в таблице 7.
Таблица 7.Технологическоеоборудование и
№ № |
Наименование оборудования |
Тип, модель |
Число единиц |
Размеры оборудования, м. |
Площадь, м2 |
Стоимость, руб |
||
Единицы |
Общая |
Единицы |
Общая |
|||||
Итого |
организационная оснастка
Подбор технологической оснастки производим в таблице 8.
Таблица 8. Технологическая оснастка
№ |
Наименование оборудования |
Тип, модель |
Число единиц |
Стоимость, руб |
|
Единицы |
Общая |
||||
Итого |
Производственная площадь определяется по формуле:
Fзоны =Коб (Fавт.*n+Σ Fоб,), м2 (43)
где Коб– коэффициент плотности расстановки оборудования
(принимается из табл. 1.17[2]);
n – расчетное число постов в зоне ТО (см. формулу 42, ПЗ).
Fоб - площадь горизонтальной проекции оборудования
(принимается из табл. 7, КП, «Площадь, м2, общая» ).
Fавт.- площадь горизонтальной проекции автоммобиля (см. п.1.2, ПЗ)
Руководствуясь (СНИП II-Д-9-6) принимается площадь участка
( ) м2, длина – ( )м, ширина – ( ) м.
2.8. Выбор метода организации
производственного процесса на
проектируемом объекте
ТР автомобилей на АТП производится по потребности на специально выделенных, соответственно оснащенных технологическим оборудованием постах в зоне ремонта и производственных цехах (участках).
В связи с тем, что некоторые операции ТР технологически связаны с операциями, выполняемыми на постах ТО-1 и ТО-2, считается целесообразным ряд работ ТР, при малой трудоемкости (до 15—20% от трудоемкости ТО), выполнять совместно с работами ТО-1 или ТО-2. В принципе выполнение работ по ТР, влекущих сверхнормативный простой автомобиля на посту ТО, нарушающих режим работы линии обслуживания или универсальных постов, недопустимо.
Рекомендуется операции ТР выполнять совместно с процессом обслуживания ТО-2 при малой частоте повторяемости данной операции (коэффициент повторяемости 0,15) и в случае, если операции ТР имеют малую трудоемкость.
Указанный объем работ выполняется за счет так называемого «скользящего» рабочего (бригадира), т. е. такого рабочего, который включается в работу любого поста, где возникает потребность в дополнительной рабочей силе для выдерживания установленного такта поста линии.
Ремонт автомобилей производится одним из двух известных методов: агрегатным или индивидуальным.
При индивидуальном методе ремонта
агрегаты, снятые с автомобиля, не обезличиваются, их ремонтируют, а затем
устанавливают на тот же автомобиль. Этот метод характерен длительностью
простоя автомобиля в ремонте.
Более прогрессивным является агрегатный метод ремонта автомобилей, при котором неисправные агрегаты заменяют исправными (ранее отремонтированными или новыми) из оборотного фонда, имеющегося в автохозяйстве. Неисправный агрегат после ремонта поступает в оборотный фонд.
Агрегатный метод ремонтапозволяет сократить время простоя автомобилей в ремонте, поскольку замена неисправных агрегатов и узлов на исправные, как правило, требует меньше времени, чем ремонтные работы, производимые без обезличивания агрегатов и узлов.
В зоне текущего ремонта работы проводятся на универсальных или специальных тупиковых постах, которые оснащаются осмотровыми
канавами, подъемно-транспортными устройствами, приспособлениями и инструментом.
Для обеспечения выполнения ремонтно-восстановительных работ в АТП, создаются следующие производственные цехи (отделения): агрегатный, слесарно-механический, кузнечно-рессорный, сварочный, медницкий, электротехнический, аккумуляторный, топливной аппаратуры, шиномонтажный, кузовной, малярный и т.д.
При агрегатном методе ремонта применяется агрегатно-участковый метод организации производства, который заключается в том, что все работы по ТО и ремонту подвижного состава АТП распределяются между производственными участками, полностью ответственными за качество и результаты своей работы.
Эти участки являются основными звеньями
производства. Каждый из основных производственных участков выполняет все работы
по ТО и ТР одного или нескольких агрегатов (узлов, систем, механизмов,
приборов) по всем автомобилям АТП. Работы распределяются между
производственными участками с учетом величины
производственной программы, зависящей от количества подвижного состава на АТП
и интенсивности его работы.
На крупных и средних АТП с интенсивным использованием подвижного состава число участков, между которыми распределяются работы ТО и ТР, принимается от четырех до восьми.
В связи с этим в проекте предлагается агрегатный метод ремонта на универсальных постах, при агрегатно-участковом методе организации производства. Расстановка оборудования на проектируемом объекте предполагается в соответствии со схемой технологического процесса в зоне ТР.
Технологические возможности при выбранном методе ремонта заключаются в производстве работ по снятию и установке основных агрегатов автомобиля (двигатель, коробка передач, раздаточная коробка, мосты и т.д.), а также замена механизмов, узлов и деталей на одном универсальном посту.
3
ОРГАНИЗАЦИОННАЯ ЧАСТЬ
3.1 Организациятехнологического
процесса ТО и ТР в АТП
Схема технологического процесса
![]() |
|
|
Зона ожидания
|
|
|
ТО-1 Др |
ТР
|
ТО-2
|
Зона хранения автомобиля |
____________ основной маршрут ------------- возможный маршрут
![]() |
Ремонтно-обслуживающее производство (РОП) в АТП является вспомогательным. Готовым его продуктом может быть единица ЕО,ТО-1, ТО-2, один отремонтированный двигатель и т. п. Процесс РОП в АТП представляет собой комплекс различных трудовых процессов, каждый из которых в свою очередь является лишь частью (стадией) в изготовлении готового продукта. Технологический процесс ТО и ТР автомобилей — часть производственного процесса, представляющий сумму действий по изменению размера, формы, состояния (внутренних свойств) и взаимного расположения предметов труда (например, процесс выполнения ТО-1, процесс выполнения ТР двигателя и т. п.).
Общий технологический процесс АТП следует рассматривать согласно схеме 3.1. Прибывающие автомобили в первую очередь проходят контрольно-пропускной пункт (КПП) и осматриваются дежурным механиком. В процессе осмотра проверяется комплектность и внешний вид автомобиля, определяется его техническое состояние и прежде всего механизмов, обеспечивающих безопасность движения. После осмотра исправные автомобили направляются в зону ЕО, а затем на хранение. При необходимости некоторые автомобили после ЕО поступают в соответствующие производственные зоны ТО и ТР, а затем на хранение.
Взависимости от плана-графика профилактических работ автомобили поступают на посты общей или поэлементнной диагностики (Д-1 или Д-2) через зону ожидания ТО и ТР или в зону хранения автомобилей.
После Д-1 автомобиль поступает в зону ТО-1, а затем в зону хранения. Туда же направляются автомобили после Д-2. Если при Д-1 не удается обнаружить неисправность, то автомобиль направляется на Д-2 через зону ожидания. После устранения обнаруженной неисправности автомобиль поступает в зону ТО-1, а оттуда в зону хранения.
Автомобили, прошедшие предварительно за 1-2 дня диагностирование Д-2, направляются в зону ТО-2 для планового обслуживания и устранения неисправностей, указанных в диагностической карте, и оттуда в зону хранения.
После оформления заявки на ТР автомобиль подвергается ЕО и направляется на диагностирование Д-2 для уточнения объема предстоящего ТР, после чего направляется в зону ТР и затем в зону хранения. Углубленному диагностированию подвергаются также все автомобили для выявления потребности в капитальном ремонте (КР).
Обнаружив в процессе приемки подвижного состава повреждения аварийного характера, составляют специальный акт, который представляется главному инженеру и является основанием для предъявления материального иска виновному. В случае преждевременного возврата подвижного состава с линии по техническим причинам дежурный механик делает отметку в соответствующей графе путевого листа и направляет автомобиль в ремонт, стараясь обеспечить возвращение его на линию.
![]() |
Обнаружив на линии неисправность, водитель вызывает автомобиль технической помощи, дежурный механик выписывает листок учета на ремонт автомобиля на линии, который передает механику технической помощи. После устранения неисправности заполненный механиком автомобиля технической помощи листок учета передается дежурному механику КПП.
Перед выездом на линию водителю в диспетчерской выдают путевой лист, который он предъявляет механику КПП и получает разрешение на выезд. Во многих АТП дежурный механик, с целью сокращения времени выезда автомобилей, оформляет разрешение на выезд в путевых листах заранее, до начала выпуска подвижного состава.
3.2
Организация управления
производственными подразделениями
ТО и ТР в АТП
|
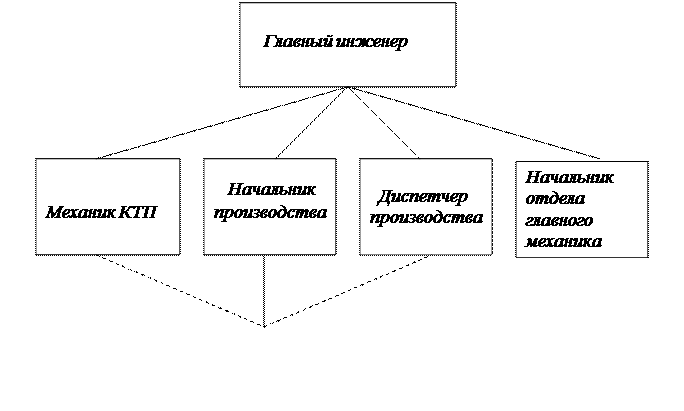
|
|
|
|
|
|
![]() |
|
Схема управления производством при агрегатно-участковом
методе технического обслуживания и ремонта.
При агрегатно-участковом методе в
автохозяйстве организуют производственные участки, на которые возлагаются все
работы по техническому обслуживанию и ремонту подвижного состава. При этом
каждый производственный участок выполняет работы по одному или нескольким
агрегатам и механизмам автомобиля во всех видах воздействия (ТО-1, ТО-2 и ТР).
Так, например, рабочие производственного участка, выполняющие работы по
двигателю, производят их на постах технического обслуживания (ТО-1 и ТО-2), на
постах текущего ремонта и отделении ремонта двигателей агрегатного цеха.
Производственные участки, специализирующиеся на обслуживании и ремонте определенных агрегатов, механизмов и систем автомобиля, считаются основными, а специализирующиеся по видам работ (жестяницким, сварочным, медницким, кузнечным, слесарно-механическим и др.), обслуживающие основные участки, — вспомогательными.
Для крупных и средних автохозяйств организуют восемь производственных участков с соответствующимраспределениемработ между ними, например:
1 - техническое обслуживание и ремонт двигателей;
2 - техническое обслуживание и ремонт сцеплений, коробок передач, ручного тормоза, карданной передачи, редуктора, самосвального механизма;
3 - техническое обслуживание и ремонт переднего моста, рулевого управления, заднего моста, тормозной системы, подвески автомобиля;
4- техническое обслуживание и ремонт систем электрооборудования и питания;
5 - техническое обслуживание и ремонт рамы, кузова, кабины, оперения и облицовки. Медницкие, жестяницкие, сварочные, кузнечные, термические и кузовные работы;
6 - техническое обслуживание и ремонт шин;
7 - слесарно-механические работы;
8 - моечно-уборочные работы.
При незначительном среднесуточном пробеге и малом количестве автомобилей в автохозяйстве, определяющих малый объем работ производственных участков и недоиспользование на них рабочих, количество производственных участков за счет их объединения может быть сокращено до четырех.
В этом случае объединяются 1 и 2 участки, 3 и 4 и 5 и 7. Моечно-уборочные работы в самостоятельный производственный участок не выделяются. Данный вид обслуживания выполняется водителями.
Работы, закрепленные за основными производственными участками,выполняются на постах технического обслуживания и ремонта автомобилей.
При выполнении технического обслуживания на поточных линиях его организуют в самостоятельный участок (например, ЕО и ТО-1) илизакрепляют за соответствующими производственными участками
специализированные посты линии или рабочие
места, если возможна их полная загрузка.
При данной организации производства технического обслуживания и ремонта повышается ответственность исполнителей, а значит, и качество работы и надежность автомобилей.
Управление производством технического обслуживания и текущего ремонта автомобилей в автохозяйствах при агрегатно-участковом методе осуществляется по схеме (стр. 33 ПЗ)
В соответствии с данной схемой главный инженер осуществляет общее руководство, производством. Начальник производства организует производство и эффективный его учет. На него возлагаются мероприятия, направленные на повышение качества технического обслуживания и ремонта подвижного состава, снижение простоев автомобилей в текущих ремонтах, снижение стоимости технического обслуживания и ремонта и др.
Диспетчер производства осуществляет оперативное руководство всеми работами на постах технического обслуживания и ремонта автомобилей и отвечает за своевременную подготовку автомобиля к выпуску. Механик контрольного пункта контролирует техническое состояние автомобилей как по возвращении с линии, так и при выпуске после технического обслуживания или ремонта. Начальник отдела главного механика (мастер, бригадир) обеспечивает ремонт оборудования, зданий и сооружений.
Производственный участок возглавляет и руководит им бригадир, мастер или начальник (в зависимости от назначения и объема работы участка). Руководитель организует работу участка, закрепляет рабочих по видам технического обслуживания и ремонта, перемещает рабочих с одного вида работ на другой, обеспечивает их неснижаемым фондом запасных частей, материалов и агрегатов и проводит мероприятия по повышению качества технического обслуживания и ремонта.
3.2 Режим
труда и отдыха
1. Пятидневная рабочая неделя.
2. Начало рабочего дня в 800 часов, конец рабочего дня в 1700 часов.
3. Обеденный перерыв – один час: с1300 до 1400.
4. Выходные дни – суббота, воскресенье.
5. Число дней основного отпуска в году – 18 дней (см.табл. 2 приложение 1 {4}.
ЗАКЛЮЧЕНИЕ
Исполнитель: Гладышев Е.В.
Тема: Проект зоны текущего ремонта
в АТП г. Омск
Основная модель, число единиц, ЛиАЗ 6212 109
КТГ - 0,86
КИП - 0,82
Годовая программа зоны, чел-час. 8608
Технологически необходимоечисло рабочих, их разряд
1 человек-Vразряда, 1 человека -IV
разряда, 1 человека -IIIразряда,1 человек-IIразряда
Площадь участка, м2 36
Число единиц оборудования,ед.- 34
Стоимость оборудования, руб. 396320
Процент трудоемкости участка, % 8,5
Среднесуточный пробег, км 254
Категория условий эксплуатации III
ЛИТЕРАТУРА
1.Алябьев С.А. Технологическое проектирование подразделений по техническому обслуживанию и ремонту подвижного состава на АТП. [Текст]: методические указания по выполнению курсового проекта / авт.- сост:С.А. Алябьев – Мариинск: ГПОУ МПТ 2016.-75с..2016 г.
2. Бернацкий В. В.Специализированный подвижной состав грузового автотранспорта. Часть 1 / В.В. Бернацкий. - М.: НИЦ ИНФРА-М, 2015. - 48 с.: 60x90 1/16 ISBN 978-5-16-103673-0 (online).[Электронный ресурс] / Электронно-библиотечная система. - Режим доступа:
http://znanium.com.
3. Бойко Н. И. Организация, технология и производственно-техническая база сервиса строительных, дорожных и коммунальных машин: Учебное пособие для специалистов / Бойко Н.И., Санамян В.Г., Хачкинаян А.Е. - М.:УМЦ ЖДТ, 2014. - 424 с.: 60x84 1/16. - (Высшее профессиональное образование) (Переплёт) ISBN 978-5-89035-630-7,[Электронный ресурс] / Электронно-библиотечная система. - Режим доступа: http://znanium.com.
4. Виноградов В. М.Техническое обслуживание и текущий ремонт автомобилей. Механизмы и приспособления : учеб. пособие / В.М. Виноградов, И.В. Бухтеева, А.А. Черепахин. — М. : ФОРУМ : ИНФРА-М, 2017. — 272 с. — (Среднее профессиональное образование).[Электронный ресурс] / Электронно-библиотечная система. - Режим доступа: http://znanium.com.
5.
Виноградов В. М.Устройство, техническое обслуживание и ремонт
автомобилей : учеб. пособие / В.М. Виноградов. –
М.: КУРС: ИНФРА-М, 2017. – 376 с.[Электронный ресурс] / Электронно-библиотечная
система. - Режим доступа: http://znanium.com.
6. Епифанов Л. И.Техническое обслуживание и ремонт автомобилей : учеб. пособие / Л.И, Епифанов, Е.А. Епифанова, — 2-е изд., перераб. и доп. — М. : ИД ФОРУМ : ИНФРА-М, 2017. — 352 с. — (Профессиональное образование) [Электронный ресурс] / Электронно-библиотечная система. - Режим доступа: http://znanium.com.
7.Оборудование для автосервиса и гаража. [Электронный ресурс]:- Режим доступа:http://www.vseinstrumenti.ru/avtogarazhnoe_oborudovanie//, свободный. - Загл. с экрана.
8. Туревский И. С.Техническое обслуживание автомобилей. Книга 1. Техническое обслуживание и текущий ремонт автомобилей : учеб. пособие / И.С. Туревский. — М. : ИД «ФОРУМ» : ИНФРА-М, 2017. — 432 с. — (Среднее профессиональное образование).[Электронный ресурс] / Электронно-библиотечная система. - Режим доступа: http://znanium.com.
9.Туревский И.С. Дипломное проектирование автотранспортных предприятий : учеб. пособие / И.С. Туревский. — М. : ИД «ФОРУМ» : ИНФРА-М, 2015. — 240 с. — (Среднее профессиональное образование). - Режим доступа: ZNANIUM.COM, по паролю.
10. Туревский И. С.Техническое обслуживание автомобилей зарубежного производства : учеб. пособие / И.С. Туревский. — М. : ИД «ФОРУМ» : ИНФРА-М, 2017. — 208 с. — (Профессиональное образование).
[Электронный ресурс] / Электронно-библиотечная система. - Режим доступа: http://znanium.com.
Нормативно-правовые
акты
11.Положение о техническом обслуживании и ремонте подвижного состава автомобильного транспорта. Издательство «Транспорт»1988 г.
12. Положение об организации и защиты курсового проекта. [Текст]: положение ГПОУ «Мариинский политехнический техникум» разработано специалистом по менеджменту качества Ходус Л.А 20.01.2016г., согласовано с заместителем директора по учебной работе Вершининым В.В 20.01.2016. Утверждено директором ГПОУ МПТ Кожемяко Н.Н. 22.01.20016г., приказ № 9 от 22.01.2016г, 20016.-6с.